In 2015, the UN’s Intergovernmental Panel on Climate Change predicted that, by 2050 the net carbon emission of the global aviation industry could reach as high as 15% from the existing 3.5%. In this context, many major aerospace manufacturers are pursuing the philosophy of more electric, fuel-efficient, green aircrafts. One of the many technologies which really is pushing this idea forward is implementation of electrohydrostatic actuators (EHA) in flight control applications.
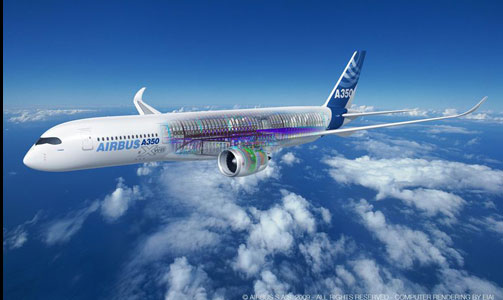
Airbus’ A350 XWB jetliner has set the standard for next-generation efficiency from design to operation.
In most conventional aircraft, flight control is accomplished by an electrically operated directional-control valve working in conjunction with a double-acting actuator. The pressurized fluid to the directional control valve is routed through steel tubes by a centralized engine-driven pump. A position feedback loop is also used for precision actuation. The directional control valve is activated upon reception of pilot command and routes pressurized hydraulic fluid to the actuator until the desired actuation is obtained. However, in electrohydrostatic actuation systems, the centralized pumps, lengthy tubing and the power dissipating directional control valves are completely eliminated.
EHA actuators are compact, self-contained and placed locally at the site of flight control surface. They typically consist of a servomotor, a fixed displacement pump, accumulator, series of check valves and pressure relief valves all packed into one integrated unit for plug-and-play kind of operation. These modular systems convert the electrical input command into actuator movement by routing hydraulic fluid into it via a fixed displacement pump attached to a servomotor. The direction of movement of the actuator depends on the direction of rotation of the servomotor driving the pump. As the power is generated only upon reception of electrical input command, EHA systems are also referred to as ‘power-by-wire’ type actuation systems.
By eliminating the continuously running centralized pump, electrohydrostatic actuators ensure that unnecessary power generation (say during aircraft cruise) is avoided. Further, since the long steel tubing along with other valves are also eliminated, the overall structural weight of the aircraft is reduced. These factors result in increased fuel efficiency and reduction of operation costs of an aircraft.
Most modern day aircraft like Airbus A350, A380, Lockheed Martin’s Lightning etc., have already implemented EHA systems for flight control systems and have reported weight saving of up to 5 kg per EHA actuator. As Denis Eckile, the Program manager – Joint Striker Program Lockheed Martin had predicted way back in 2001, EHA systems have definitely proved to be GenNext and is a technology which is here to stay!
Contributed by Harshavardhan Joshi, Aircraft Hydraulic Systems Engineer, CSIR – National Aerospace Laboratories, India
Filed Under: Mobile Hydraulic Tips, Slider