Hard-to-access locations aren’t hard to come by these days. With wars, natural disasters, and political unrest, people worldwide suffer from wounds, illness, and famine in harsh environments. Though local and global organizations gather food and supplies to deliver to those in need, sometimes the aid can’t get there, or the mission puts crews at risk.
Flowcopter, a developer of industrial heavy-lift drones, has a solution — and it’s based on hydraulics.
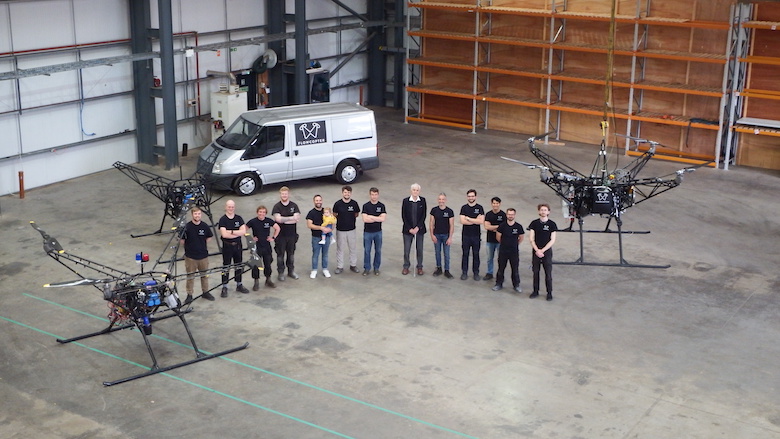
Before the company was founded, Peter McCurry and Uwe Stein spent about 15 years developing digital displacement technology in Edinburgh at Artemis Intelligent Power, which Danfoss acquired in 2021.
At Artemis, McCurry and Stein aimed to solve hydraulics’ most complex problems: efficiency and control response. Typically, if a hydraulic system is designed for control response, it won’t be efficient. Likewise, if the system is efficient, it won’t respond quickly. So, Artemis developed digital displacement technology to accommodate, and Stein was instrumental in leading the pump development team.
They approached market launch a few years ago and focused on mobile off-road machinery. But the team also reevaluated the technology and looked for other possible applications of interest, namely hybrid multicopters.
“We were very aware of the limitations of battery electric systems. They’re incredible for some applications, but there are hard electrochemical limitations on what you can do,” said McCurry, Flowcopter’s managing director. “If you accept that you’ve got to carry a battery system when you fly, then you’re going to be really limited with electric aviation in the future.”
They assumed that most systems trying to scale up from small battery electric drones would start looking at hybrid options, such as liquid-fueled engines driven by a net-zero synthetic fuel. And they figured the one rotating shaft on the engine would turn into multiple rotating shafts on the propellers with speed control. However, an electric transmission weighs and costs substantially more than the engine and creates reliability issues when trying to lightweight it for aerospace.
“We had a transmission that looked like it might be quite useful for this,” said McCurry, “but we weren’t sure if we had the control bandwidth. So, I led a team at Artemis to build some single-axis test rigs, and they worked pretty much out of the box. We had a controlled response — we could control a single-axis arm that could pivot, control the position, and do a step from one height to another. And all of this was controlled by a digital displacement pump.”
Flowcopter received a patent to use the technology for aerospace propulsion and raised some capital to build a demonstrator platform. But the general aerospace audience wasn’t so convinced. Many industry experts understood why McCurry and Stein wanted to use hydraulics. Still, they didn’t think hydraulics would have fine enough control and fast enough control response for a multicopter. However, once the demonstration platform was up and running, Flowcopter caught the attention of many big aerospace companies.
“There’s a real need for a robust industrial solution that sits between drones and helicopters, and that’s exactly the market we’re trying to address,” said Stein, Flowcopter’s CTO. “In our latest video, you’ll see we can take about 130 kg of payload on board. We plan to do more optimization to increase the payload further.”
The idea is to put the Flowcopter drone on a trailer, drive out in the field, and immediately launch and deliver 100 kg of cargo up to 100 km away.
“It’s small enough to be mobile but big enough to have a meaningful impact on the area you’re trying to supply,” said Stein.
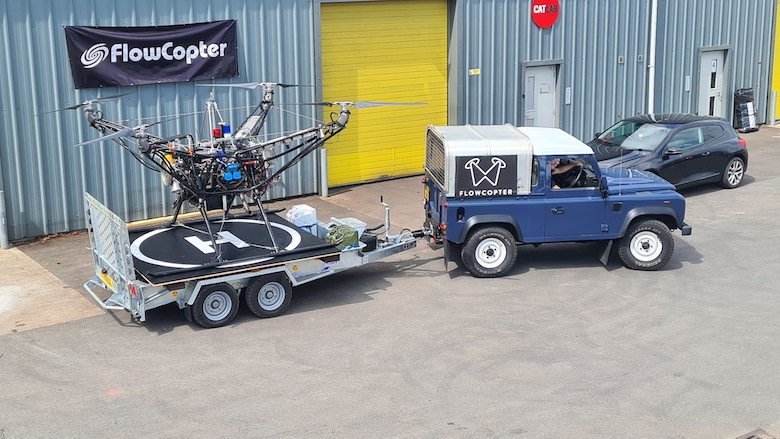
Though the technology can be used for dozens of applications, such as logistics, crop spraying, tree planting, or firefighting, aid delivery is a notable application of interest.
“We have an Innovate-UK-funded project where we’re working with a company called Air Logistics, which does a lot of work for the UN World Food Program,” said McCurry. “What they see is that any aid delivery is inherently risky. You’re risking crew to operate in austere and uncertain environments. If you’re driving down a road, that road could be blocked. Some people on the road might fancy taking your truck or whatever you have in your truck. So, the ability to fly means you avoid damaged infrastructure, risky roads, and local situations to deliver the aid where you want it to go.”
However, the cost of flying-in aid must be very low, as the UN World Food Program lacks the budget to send expensive systems into harsh environments. That’s why Flowcopter’s low-cost transmission technology turns heads.
“Hydraulics has always been a bit trapped because it’s seen as a sunset industry by some people,” said McCurry. “You talk to people in drone land, and they don’t know anything about hydraulics or think hydraulics is something you might find in your grandfather’s tractor.”
Though many intend to electrify, McCurry points out that lightweight electric transmissions with exposed copper wires won’t satisfy an industrial use case running continuously at full power for 6,000 hours, eight to 10 hours per day, despite weather conditions.
“If you want to develop something that has to work 10 hours a day, seven days a week in the field, it must be robust, maintainable, and usable in very harsh environments. So, our basic design is much closer to what you would expect in a helicopter but at a much lower cost,” said Stein.
Flowcopter continues experimenting with materials and modifying the design to earn aerospace certification while keeping costs low.
“2022 was a year to explore the technology and prove that it works. This year, we developed our first product, the FC 100. Next year, we want to go out into the world and engage with pilot customers,” said Stein. “Our plan is to start small-scale production and gain field experience — it might be food delivery in South Sudan, crop spraying, or a logistics application. Next year is the year our Flowcopter gets out into the real world.”
Watch Flowcopter’s latest demonstration at its new test facility:
Flowcopter
flowcopter.com
Filed Under: Mobile Hydraulic Tips, Trending