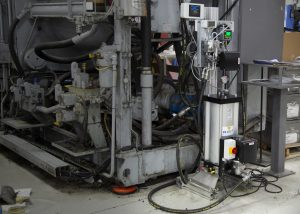
Using a RMF varnish removal system from Des-Case improved uptime in an appliance manufacturer’s plastic injection molding machine.
Hydraulic fluid is one of the most important components in an injection molding machine, which is why contaminated fluid cannot be overlooked. 80% of all hydraulic failures are caused by contaminated fluid. The common types of contaminants are solid particles and water, but varnish is just as destructive for hydraulic systems.
The constant pressure and temperature fluctuations of the hydraulic fluid can lead to mechanical and thermal stress of the fluid. This instability results in a breakdown of oil molecules leading to the creation of a sticky residue (varnish by-products). This residue, combined with other contaminants, can cause friction and wear, which can shorten component oil life and cause unnecessary downtime of the system.
Additionally, the forming of varnish can be accelerated by a chemical reaction between metal solid particles and water. This reaction results in corrosion of the components, changes in fluid properties, and oil degradation.
A large appliance manufacturer in the United States reached out to Des-Case regarding an increase in unplanned maintenance, blocked line filters, and frequent oil changes on their Toshiba plastic injection molding machine. All of these symptoms were in line with severe varnish problems and was further confirmed by an oil lab analysis. The results of the test showed a Membrane Patch Colorimetry (MPC) value at a critical level of 63.4 and an ISO cleanliness level of 25/20/14.
To solve the varnish problem, Des-Case offered its RMF Varnish Removal System, which acts as a kidney loop, continuously pumping fluid through the high-efficiency varnish removal cartridges.
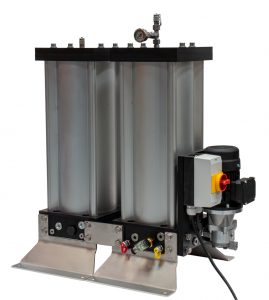
Long fiber cellulose/PP cartridges in Des-Case’s Varnish Removal System are specially designed for the removal of varnish by-products which are dissolved in the fluid.
The Varnish Removal System combines varnish removal with oil quality monitoring and prevents varnish from forming by removing solid contaminants and water.
The Long Fiber Cellulose/PP cartridges are specially designed for the removal of varnish by-products which are dissolved in the fluid. These cartridges adsorb polar acids through special compacted fibers, which create an intricate internal flow path. Unlike other technologies, the cartridges do not add water to the fluid. They remove water and other solid contaminants.
During the operation time of the system, samples were taken frequently and sent to a laboratory for analysis. Next to a standard fluid analysis, an MPC and gravimetric solids (MPC weight) test was done to measure the varnish potential. After three weeks of filtration, the varnish potential (MPC value) went from a critical level of 63.4 to 7.8, and the MPC weight decreased from 0.0182 to 0.0072 g. In the following five weeks, the MPC dropped even lower to 1.6 and weight down to 0.0038 g. The ISO cleanliness levels also dropped from 25/20/14 to 17/14/11 in three weeks. Five weeks after that, the ISO code dropped even further to the target level of 15/13/10.
As the data shows, the cleanliness and health of the lubricant improved significantly in a short time and will improve the uptime of the machine.
Des-Case
descase.com
Filed Under: Sealing & Contamination Control Tips