Water and particulate matter receive much attention for their impacts on hydraulic fluid quality. But there’s another less-famous troublemaker causing problems right under OEMs’ noses.
Just like any contaminant, air can be introduced into hydraulic fluid through various means. Common sources include leaks, loose connections, worn seals, and agitation or turbulence within the reservoir. Even regular maintenance tasks, such as changing filters or replacing oil, can inadvertently add air to the fluid.
Air contamination can cause the following problems:
- Gaseous cavitation. As air bubbles coalesce, grow, and collapse inside a hydraulic system, it causes loud noises and can damage the internal hydraulic components.
- Spongy hydraulics. Unlike hydraulic fluid, air is compressible. As a result, too much air contamination can cause a delayed response or “spongy” feeling in a hydraulic system instead of an instant reaction. The result is inefficient, unpredictable, and potentially dangerous system performance.
- Oxidation of hydraulic fluid. When oxygen reacts with hydraulic fluid, it produces varnish, a sludgy byproduct. This varnish increases fluid viscosity and can build up around valves, causing sluggish performance, damage to system components, blocked return lines, and other concerns.
Between safety issues, poor performance, and costly repairs, addressing this contamination is vital for safe and efficient hydraulic operations. Schroeder Industries’ new Air Fusion Technology (AFT) is an in-tank air filtration solution engineered to increase machine reliability and efficiency, protect components, and enable downsized hydraulic reservoirs.
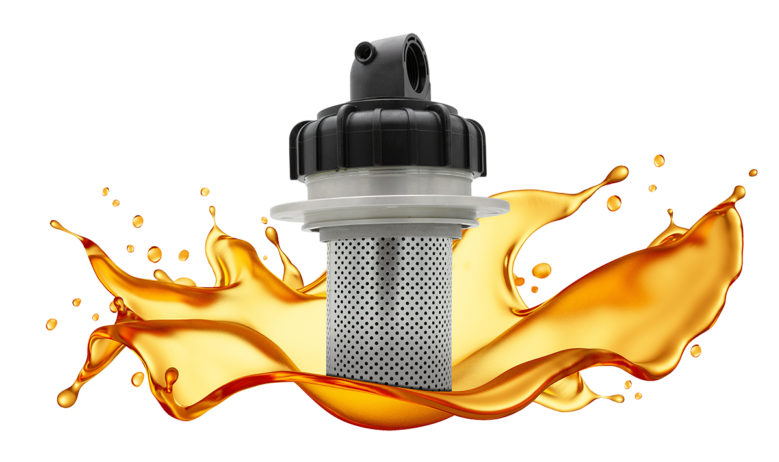
Compared to a standard out-to-in flow in-tank filter, the AFT reduces the amount of air that enters the suction line on the first pass by 20%. As the AFT decreases fluid turbidity, it channels fluid upwards and promotes rapid bubble coalescence. These bubbles quickly rise to the surface of the reservoir and dissipate. Contrarily, the traditional filter is less effective at reducing turbidity, allowing air bubbles to stay suspended lower in the reservoir and enter the suction strainer.
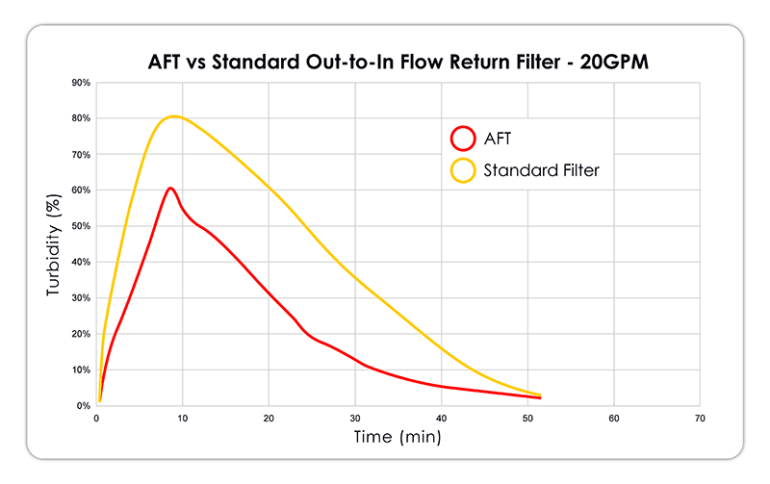
“Within a hydraulic system, the only way to remove air from the hydraulic oil is to get it to rise to the surface of the fluid within the reservoir and dissipate it out the breather. Everywhere else is a pressurized closed system,” said Jeremy Crookshanks, product manager of Hydraulic & Lube Filtration at Schroeder Industries. “When we started our tank optimization program, we originally set out to use our existing filters to help gain performance and reduce the size of hydraulic reservoirs. But through CFD modeling and other analyses, we found ways to tweak the filter and came up with the next generation of filter families.”
The AFT’s unique filter head is 100% injection molded and swivels independently of the inlet port, allowing toolless element change-outs. A specialized bypass valve in the head of the filter allows the filter to de-aerate fluid even when in bypass for greater filtration efficiency.
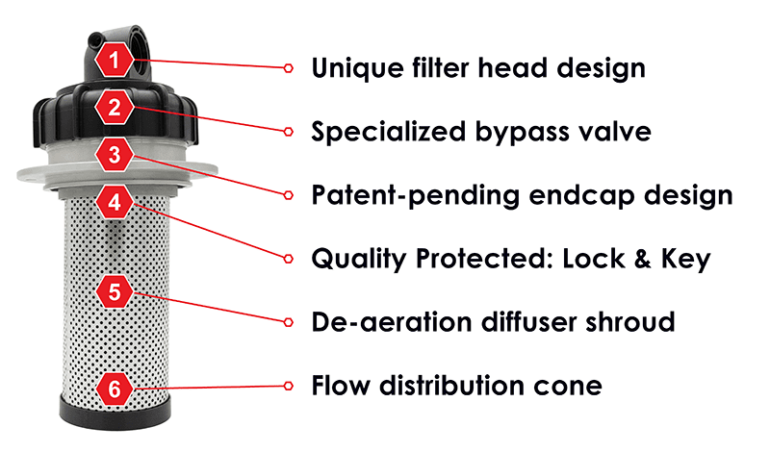
“A lot of other filters have a bypass valve in the bottom of the element, and all the dirt and contaminants come to rest on that bypass dish. Then, in a cold-start scenario when the oil is heavy and more viscous, all the contaminants flush right into the tank,” said Crookshanks. “The filter’s supposed to clean things up, not let stuff back down into the reservoir. So, we moved the bypass up into the head of the filter, and the contaminant stays down in the element itself.”
The patented endcap design allows bypass flow to enter the top of the element while still being subjected to the diffuser shroud to maximize filtration. Additionally, the patented Lock & Key Quality Protection element design ensures that only high-quality elements are used to ensure that the AFT performs at its full potential.
“The nice thing about Lock & Key is, just like making unique keys for a house, we can do special locks and keys for different customers. And if we do that, then it moves from quality protection or a patented solution to intellectual property. So, maybe an OEM owns that, and only that OEM can use those elements,” said Crookshanks.
Other notable design features include the de-aeration diffuser shroud that significantly reduces fluid turbidity. Less turbulent fluid allows for faster bubble coalescence and improved air filtration. Also, the internal flow distribution cone redirects fluid toward the top of the reservoir, allowing air to exit the hydraulic fluid more easily.
“If you think about air bubbles, the smaller the air bubble, the slower it moves through the hydraulic fluid,” said Crookshanks. “So, if you use the shroud to coalesce small air bubbles up into larger air bubbles, they’ll rise faster to the surface — just general buoyancy.”
The filter design also includes windows at the top of the element so that even in bypass mode, fluid flow is still pushed down into the coalescing area to help de-aerate the fluid.
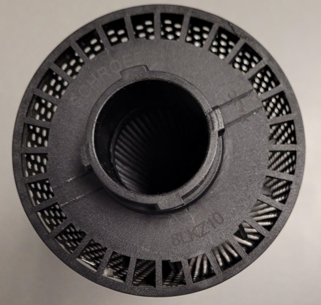
“At Schroeder, we can inject air into a customer’s hydraulic tank and monitor how quickly that air dissipates out of the reservoir. And we can test the hydraulic tank design versus our optimized design,” said Crookshanks. “We also have an air content sensor that we take to the field and hook up on a machine to check the air content. Then, we can either change to a filter like the AFT to see if that cleans up the issue. If it doesn’t, we can work together on a CFD simulation of the reservoir to see what changes we could make to improve the overall tank performance.”
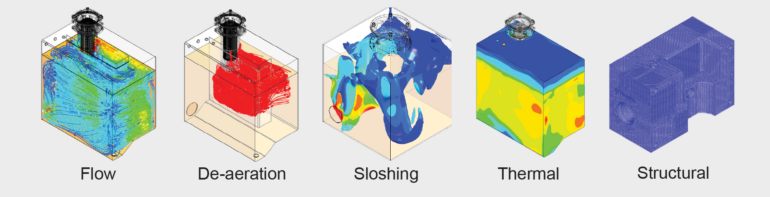
Energy efficiency is a major component of Schroeder’s Energy Sustainability Initiative. With the AFT, the goal is to create a smaller, more efficient hydraulic system to help OEMs get the most out of their fuel sources, whether diesel, hydrogen, or electricity.
“One of our goals is to reduce the size of the reservoir because less oil and less steel is less cost on the machine and less environmental and carbon footprint,” said Crookshanks.
The AFT is so effective and efficient in its filtration capabilities that it can downsize a machine’s hydraulic reservoir by up to 60%. A smaller reservoir results in a lighter system, which can improve energy efficiency. With less room taken up by the hydraulic tank, space becomes available for a larger fuel tank, additional batteries, or other useful components.
Schroeder Industries
schroederindustries.com
Filed Under: Components Oil Coolers, Filtration/Contamination Control, Sealing & Contamination Control Tips