By Josh Cosford, Contributing Editor
If you’ve ever been (un)lucky enough to open up a 30-year-old hydraulic reservoir, you know how shockingly grimy they can be. I’ve seen 3 in. of sludge, filings and particles sedimentate enough to clog the suction filter. That hydraulic power unit had a return filter in addition to its clearly unhelpful suction filter. So, if the power unit was assumed to be sufficiently filtered, how did so much junk find its way into the reservoir?
Fluid is the lifeblood of your hydraulic system, and both the circulating and stored oil should be treated equally as a homogenous resource. By stored, I’m referring to the oil residing in the reservoir, which typically provides three to five minutes of dwell before charging forth to transfer force through the hydraulic system.
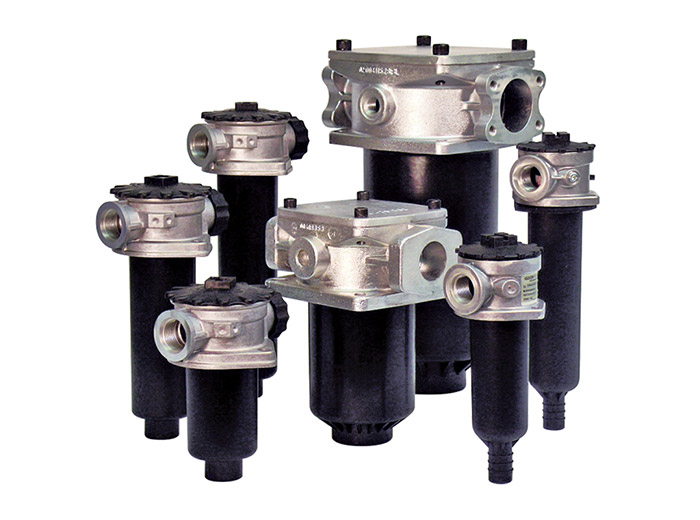
To answer my original question, the obvious reason for the reservoir landfill is that we provided contamination with a VIP backstage pass. The existence of a return filter offers no guarantees of cleanliness, and I’ve been touting the uselessness of the suction filter for well over a decade. On top of poor filtration, you and I both know you just pour new hydraulic oil in your reservoir straight from the bucket. “Put me on the right path, Josh,” I hope you’re saying. Even if you’re not, I will just go ahead and do it anyway.
Every hydraulic system I’ve seen outside compact hydraulic power packs was installed with a return line filter. The venerable spin-on filters provide the lowest level of protection, especially those equipped with paper or cellulose filter media. You can, however, secure a few spin-on cartridges with upgraded media, and I’ve seen some with beta ratios upwards of 200 (a higher number is better). Buy the highest beta ratio (the ratio of particles before and after the filter) possible to protect your precious hydraulics, and if the filter manufacturer doesn’t publish these data, move on.
Trapping as many possible particles from entering the reservoir prevents what is essentially a lapping compound from pumping back into the circuit to create more dirt once again as it wears precious valves, actuators and pumps. Aside from selecting an efficient return filter large enough to trap a lot of dirt without going into bypass, every other reservoir orifice should be respected like a patient on the operating room table.
Any method of adding oil should include a way of filtering new oil before filling, and the filling method itself must not introduce particles as part of its process. A filter cart employing filter media at least as powerful as your return filter should transfer the dirty new oil from its place of bulk storage into the reservoir. Just as important is how the fluid enters the reservoir; removing the breather cap to drop in a steel downpipe at the end of the cart’s output hose gets you a C+ on your exam, but a dedicated flat face coupler on your reservoir providing a sealed fluid path scores an A every time.
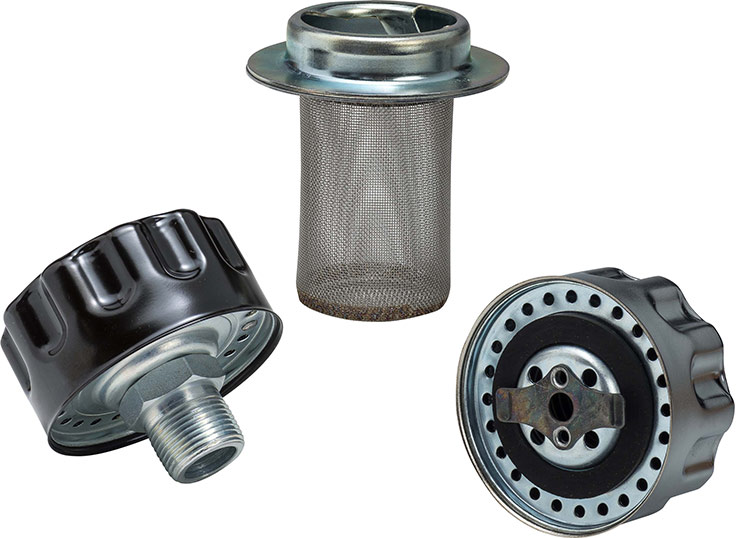
Even if your reservoir still has a breather cap, it’s best left in place. The filter/breather caps are economical methods for vital breathing functions while offering a convenient location to fill the tank. But any time you open that cap, you invite airborne contaminants into your life, so it’s best to select more securely sealed options. A threaded connection with an O-Ring or gasket ensures all air passes through the breather’s filter element, preventing dirty air from making dirty oil.
Heeding these tips on reservoir filtration systems avoids any need for pump suction filters, which do more harm than good, anyway. Plus, why have a mesh screen try to trap particles too large to damage the pump when you can simply avoid any and all opportunities to introduce particles to begin with?
Filed Under: Components Oil Coolers, Engineering Basics, Filtration/Contamination Control, Sealing & Contamination Control Tips