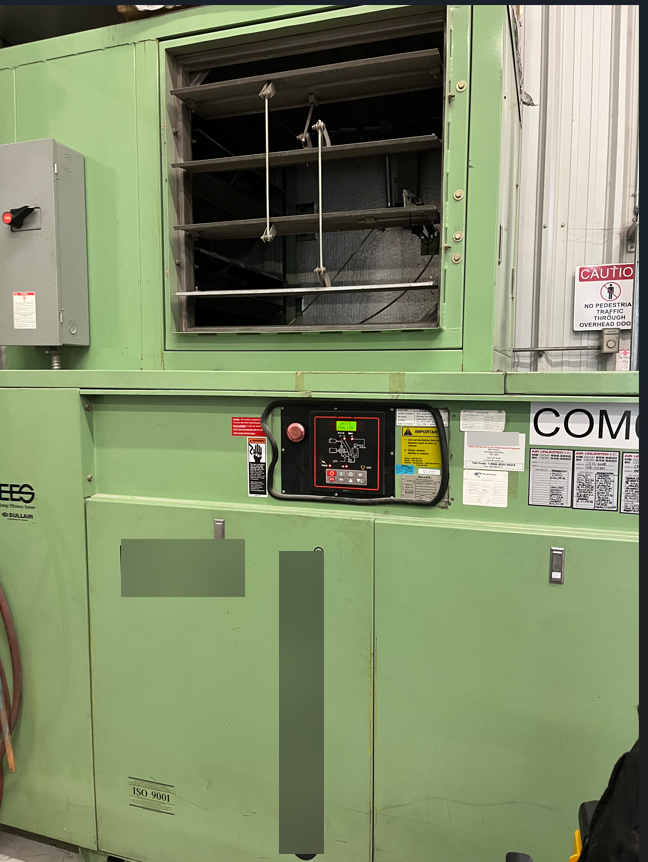
Most of the energy that goes into an air compressor comes out as heat, so it is always a good idea to direct the hot air produced to a location that needs heat — like into a plant in the winter season. The compressor in the photograph has a specially designed heat recovery system that takes care of this automatically, saving the customer money on their natural gas heating.
But it turns out this compressor is producing much more heat than desired. It is running in a mode called load/unload, where internal pressure switches load the compressor when the compressor needs to pump up the pressure in the plant and unloads the unit when the pressure is satisfied. If working normally, the compressor consumes full-rated power when loaded and reduces its power to around 25% when unloaded. This compressor, however, has internal problems that cause it to consume extra energy.
A compressed air auditor did an energy study of this facility and placed some measurement instruments on the power input. This revealed that the compressor consumed about 5% more energy than normal in the loaded state — and 50% more power in the unloaded state. This significantly increased the annual operating cost of the compressor. What’s worse, it was causing it to overheat and trip off on occasion. Additional energy consumption amounted to $5,600 in annual electrical costs.
This compressor had never been measured by an auditor, so the plant manager had no idea of the extra costs being consumed. A saving grace was that the additional energy reduced the plant heating costs by a small amount. However, this plant only needed the heat four months per year.
It pays to measure compressor operation on a regular basis to ensure internal circuitry is working. In this case, the failure of the internal sump blowdown circuitry and high pressure drop across the internal air/oil separator caused the problem. This was an easy fix that resulted in some excellent energy savings — that both paid for the repair and the audit in a short period of time.
Filed Under: Components Oil Coolers, Compressed Air Technologies, Pneumatic Tips, Technologies