No one wants air compressor oil contaminating production. And in food processing applications, quality and safety are essential.
E2M Kitchen, a fresh and ready-to-eat meal provider, knows this all too well. The Charlotte-based company significantly evolved its food preparation and packaging process for creating gluten-free, dairy-free, and preservative-free meals. Every tool used in its production process was scrutinized to ensure food safety.
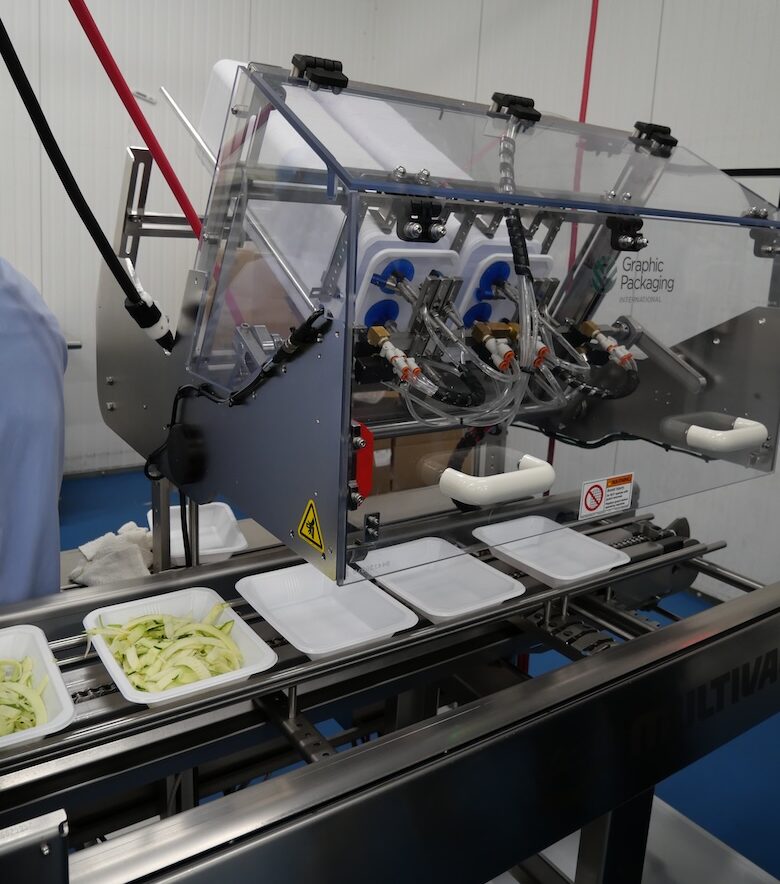
To meet growing demand, the company needed an automated system driven by compressed air — often dubbed “the fourth utility” in production plants. The air compressor powers the company’s conveyor belts and machines, including its:
- Robotic arm that places food trays on the conveyor
- Pneumatic food depositor that portions food onto trays
- Vacuum sealer that packages trayed food
- Metal detector with piston-driven air to remove trays from production if metal is detected
- High-speed printer that labels the final product
The company worked with Pattons, a southeastern ELGi distributor, to install an ELGi AB37-125 as the heart of its food production system. The air compressor can provide 216 cfm of compressed air at 100 psi. This power output aligns with the requirements for maintaining consistent air quality throughout E2M Kitchen’s comprehensive food preparation and packaging processes. ELGi’s unique rotor design reduces pressure loss and increases stage efficiency, allowing the compressor to maintain peak operational efficiency. E2M Kitchen can produce approximately 10,000 meals daily during periods of maximum production.
“The ELGi oil-free air compressor has become the cornerstone of our manufacturing line, enabling a seamless transition from manual, hands-on food preparation to an automated system,” said Levi Barbee, president at E2M Kitchen. “It has accelerated our production volumes, enabling us to cater to growing demand without compromising our strict standards of food quality and safety.”
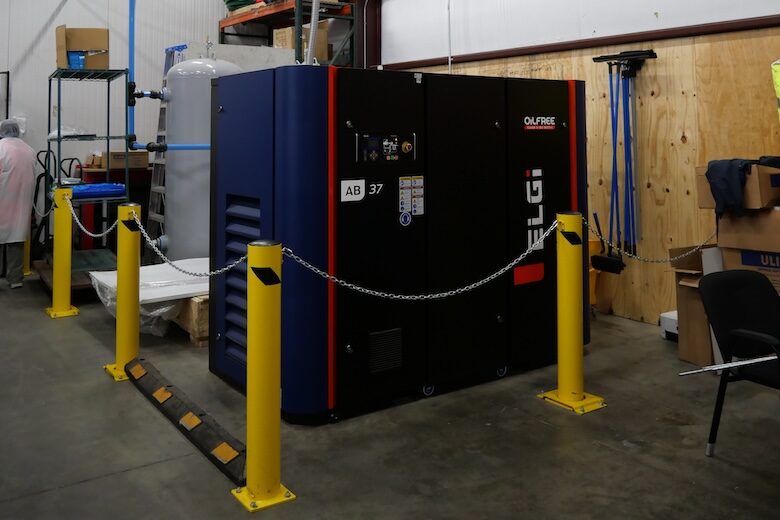
The food production industry has seen a key shift in air compressor choices. Historically, oil-flooded air compressors were the go-to, but they come with a built-in problem: oil contamination. Lubricating oil could end up in the compressed air, pushing tiny oil particles into the food, packaging, and production facilities. This oil contamination compromises product quality and introduces potential health threats to consumers.
In response, E2M Kitchen quickly embraced oil-free air compressors. The main benefit of such compressors is evident in their name: no oil. This means no risk of lubricants or oils tainting the food or the production site. However, the advantages extend beyond avoiding contamination.
The oil-free compressor also demands less maintenance than oil-flooded compressors, reducing the chances of oil spills and leaks — costly incidents that can halt production. Plus, it ensures pure air in the employee workspaces. With less required maintenance, there’s a reduced need for oil changes and filter swaps.
Minimizing oil spill and leak risks and conserving time and resources align with the company’s environmentally friendly approach and sustainability goals. E2M Kitchen is also free to consider greener packaging alternatives since there is no concern about oil or moisture affecting food trays or packages.
In a similar story, an Iowa-based flexible packaging company serving North America’s food, beverage, and pharmaceutical industries went oil-free by replacing six oil-flooded rotary screw air compressors with three ELGi oil-free air compressors.
For this company, downtime was a major concern. Oil-flooded air compressors use oil to seal, lubricate, and cool during the compression stage. Even with proper filtration, oil vapor can be passed downstream, build up in the system, and eventually jam components, leading to facility shutdowns. Moreover, the oil vapor could reach the equipment from other factory areas and cause irreversible damage, significantly driving up costs.
To remove downtime risks, this company worked with Modern Compressed Air to create a redundant system with three ELGi OF170 compressors. Demand is met with two, and the third is used to take one offline without disrupting production.
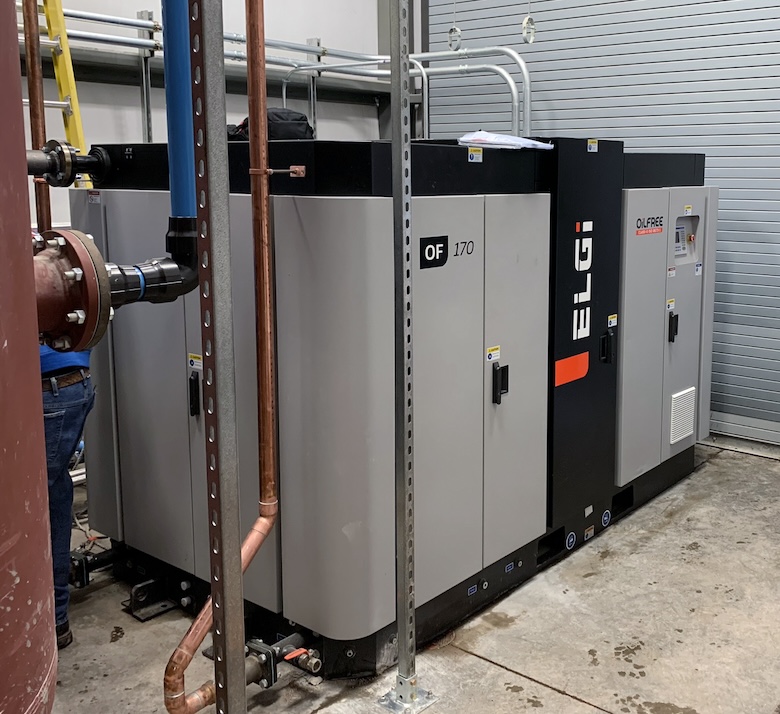
ELGi is one of the few compressor companies to design and manufacture air ends for oil-free air compressors. The units are designed to provide class zero oil-free air and meet ISO8573-1 class zero oil standards. The rotors and housing are coated with PTFE-based food-grade PP coating to resist corrosion and endure high temperatures up to 482° F.
Another appreciated feature is the variable frequency drive (VFD). Unlike traditional fixed-speed compressors, variable-speed compressors equipped with VFD can vary the speed of the motor and ensure that the compressor does not consume excess energy. This means compressors with VFD save up to 35% of energy costs compared with a fixed-speed unit. More importantly, VFD allows the facility to maintain stable pressure throughout.
“The equipment in the facility is from all over the world, and they all have different requirements in terms of energy. So, when the processes turn on and off all over the plant, it becomes difficult to react and maintain a stable airflow plant,” said Tanner Hilton, sales manager at Modern Compressed Air. “The VFD enables us to smooth the process and keep the compressors in the idle mode without turning them off.”
In this and E2M Kitchen’s case — and any food, beverage, and pharmaceutical application relying on compressed air — going oil-free is a smart move that will benefit the companies and customers in the long run.
Elgi
elgi.com
Filed Under: Components Oil Coolers, Compressed Air Technologies, Pneumatic Tips