Machinery builders and OEMs save space and improve functionality by applying electro-pneumatic I/O and solenoid systems throughout their equipment.
By: Chip McDaniel, AutomationDirect
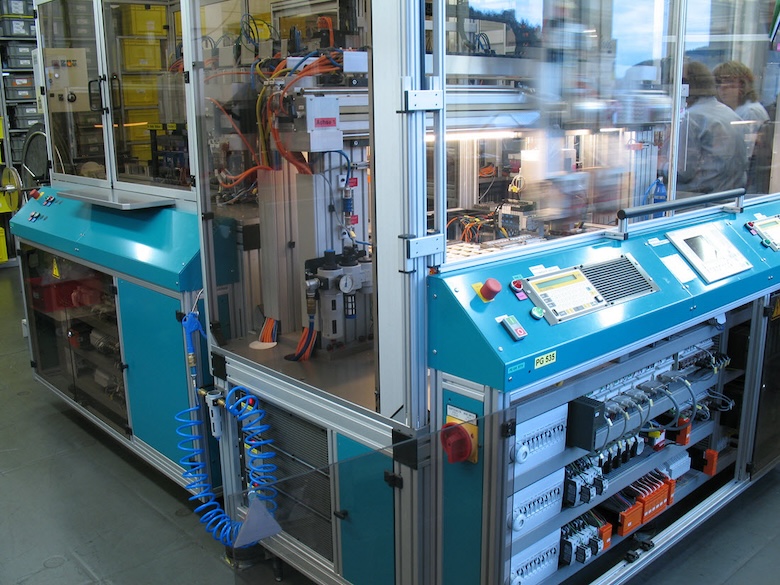
For machine builders and original equipment manufacturers (OEMs) alike, there is an increasing push to deliver smarter, more modular, and physically compact systems. Among the many design choices required to make this approach a reality is a corresponding need to distribute automation intelligence, signaling, and control elements throughout the physical system arrangements, instead of following conventional design practices of mounting all components in the main control panel.
Making OEM systems more intelligent calls for increased numbers of sensors and controlled elements. Modularity implies convenient options for both physical and logical connectivity, which can also lend itself to scalability, and compactness requires new products that lend themselves to innovative installation.
Because so many types of equipment rely on pneumatics and electrical signals, it makes sense to look for solutions compatible with both and with standard industrial automation communication interfaces. For these and other reasons, electro-pneumatic input/output (I/O) and solenoid valve bank systems have become a preferred method for distributing signaling and pneumatic automation throughout equipment of any size.
Centralized versus distributed automation
Manufacturing machines and production equipment are commonly automated by programmable logic controllers (PLCs), which use I/O modules to monitor sensors throughout the equipment and control devices such as motor controls and solenoids. A traditional design approach has been to centralize all PLCs with local I/O into a main control panel or, in some cases, a few control panels.
While sensors and motor controls predominantly use electronic signaling, pneumatics controlled via solenoids are popular for operating mechanisms and actuators because they are simple, powerful, clean, and cost-effective. Because sensors and pneumatics are usually dispersed throughout the equipment — although there are often some localized concentrations of these elements — a corresponding amount of wiring and pneumatic plumbing is involved. Automating these components via one or more main control panels requires all this wiring and tubing to be routed from the field device to the control panel, entailing significant costs in materials and labor.
An elegant way to overcome these problems and simplify equipment designs is to use electro-pneumatic automation assemblies distributed throughout the equipment.
Electro-pneumatic assembly essentials
Electro-pneumatic assemblies incorporate subcomponents that accommodate a flexible variety of I/O and solenoid valve requirements (Figure 2). They are modular, so designers can configure just what they need from a catalog of standardized options.
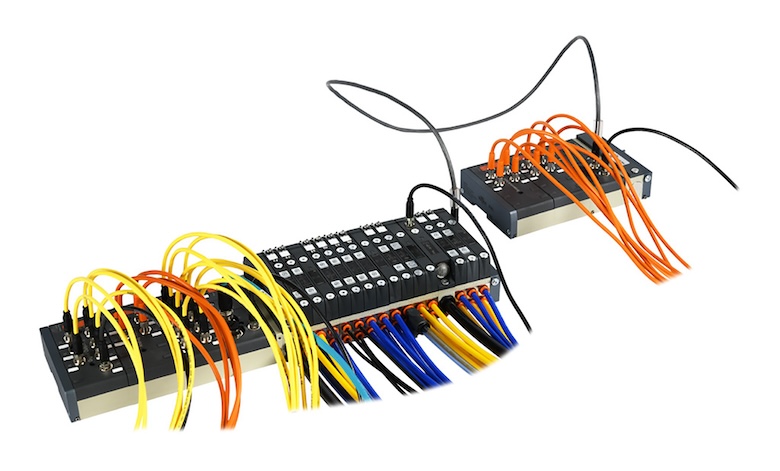
Furthermore, some products are available in completely connectorized versions — using M8 and M12 quick-disconnect electrical connectors and push-to-connect pneumatic fittings — so they can be rapidly installed and easily maintained. In fact, once the assembly is physically mounted, users don’t even need a screwdriver to make wiring connections or a wrench to plumb air connections.
Field-wireable connectors are available, but most users prefer ready-made “patch cables” for the ultimate installation simplicity and speed. Connectorized and modular designs also greatly improve the troubleshooting experience because users can rapidly swap cables and sensors to pinpoint where the problem is located.
Users should look for electro-pneumatic assemblies that are surface-mountable and IP65-rated to withstand dust and light-pressure water sprays, ensuring the assemblies can be mounted openly anywhere they are needed on equipment. The main control panel size is significantly reduced, as much or all of the I/O is located remotely, and the remote electro-pneumatic assemblies do not need any enclosures — although they can be installed within a control enclosure if it suits the design.
Connectorized I/O modules are commonly available as 24 VDC discrete and analog inputs and outputs. Each I/O module supports a certain number of these points, and a complete assembly may have a maximum I/O count. Similarly, push-to-connect pneumatic valve modules are usually available as common 3/2, 5/2, and 5/3 center-closed variants, which connect to various base sizes. As with the I/O, there will be a limit to the number of modules supported by an assembly.
Another key point for electro-pneumatic assemblies is how they communicate so much concentrated I/O and solenoid data and commands with the host controller. This is most efficiently accomplished using a standard industrial Ethernet communication protocol, such as EtherNet/IP. To do this, designers simply choose an EtherNet/IP master for the assembly and then ensure that the PLC controller is compatible, which is typically not an issue as this is a fairly common PLC capability today. An electronic data sheet (EDS) file defines how the EtherNet/IP device will interact with the host.
Depending on the electro-pneumatic system make or model, many installation topologies are possible, depending on equipment requirements (Figure 3).
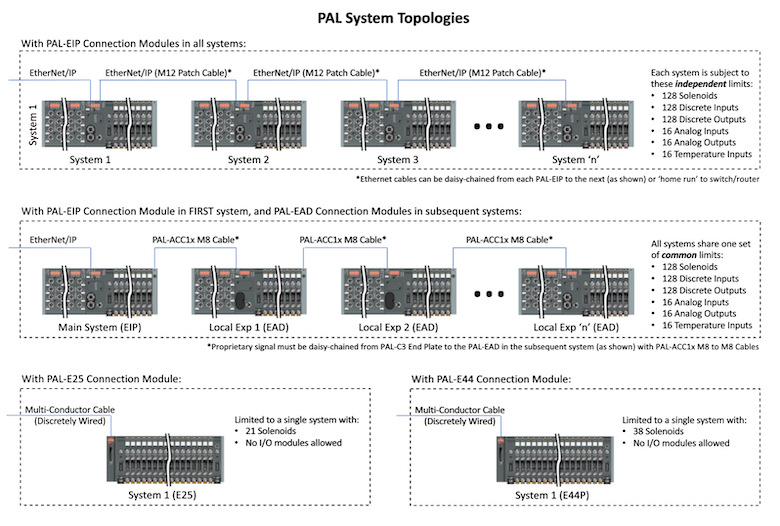
Using an industrial communications bus means that basic on/off signals and commands are available, and other extended diagnostics can be transmitted to the main controller. Therefore, electro-pneumatic assemblies are a compact and organized way to improve the intelligence and capability of I/O and pneumatics on any machine.
Making the connection
While modularity is generally considered a positive benefit, some designers are rightfully concerned about the difficulty of properly selecting and integrating from among too many options. For this reason, designers should look for suppliers offering configuration software to support this effort.
Effective configuration software will make selecting the communication controller, I/O signal modules, and solenoids easy. Furthermore, the software will identify the EtherNet/IP mapping for all signal, control, and diagnostics data, and provisions should be available for scanning and discovering any electro-pneumatic assemblies on the network and facilitating the configuration of these devices.
Availability of a flexible portfolio of components and easy-to-use software configuration tools accelerates the ability of designers to apply electro-pneumatic assemblies to any application. Small machines will realize space savings as control panels shrink in size because the I/O and solenoids are moved closer to target devices. Large machines can be fully shop-assembled, factory-tested, and rapidly broken into shipping splits. The splits can be quickly reconnected in the field — requiring only EtherNet/IP, power, and air supplies — with little risk of errors.
One company designed parts fabricating machines for the auto industry, including the automation aspects. They had embraced electro-pneumatic assemblies several years prior, using them to operate actuators for holding down parts, removing scraps, and similar operations. Designers could take advantage of the flexibility and expandability of using these EtherNet/IP devices and realize savings on troubleshooting. However, they struggled with specifying all needed components from a catalog and with supplier availability of parts, especially through the COVID-19 pandemic.
This situation improved significantly once they identified and standardized on a supplier with a comprehensive online method of selecting parts, which also showed the available stock levels and competitive pricing. Not only did these factors streamline the work, but they also served as a strong selling point for end-user customers.
Equipment designs evolve with electro-pneumatics
As machinery builders and OEMs look to deliver equipment more efficiently with greater intelligence, electro-pneumatic I/O and solenoid systems are leading methods for hitting these targets. By enabling more instrumentation and control points, simplifying installation and maintenance, and saving valuable space, these assemblies satisfy many design goals while providing overall cost savings. Modularity can increase the complexity of certain design aspects, but a flexible product portfolio and helpful configuration software will help designers effectively apply these systems.
AutomationDirect
automationdirect.com
Filed Under: Components Oil Coolers, Engineering Basics, Pneumatic Tips