A good exercise for any compressed air system is to find and fix compressed air leaks. And if the system compressors are well controlled, some significant energy savings can be gained by doing leak audits and repairs on a regular basis; this is generally recommended quarterly. Some excellent tools to use in the process are the traditional ultrasonic leak detector gun and the newly developed acoustical image detectors.
An ultrasonic compressed air leak detector gun is a sophisticated device designed to pinpoint leaks in compressed air systems by detecting high-frequency sounds emitted by escaping air. These sounds, which are typically beyond the range of human hearing, are produced when compressed air moves from a high-pressure area inside the system to the lower pressure of the surrounding atmosphere through cracks or holes.
The leak detector gun uses a sensitive microphone to capture these ultrasonic frequencies and converts them into a frequency that can be heard by the human ear through headphones, or visualized on a display. This allows leak auditors to audibly or visually locate the source of a leak. These devices can be used to detect the general location of leaks, making them invaluable for routine maintenance and ensuring system efficiency.
One problem with these, however, is when leaks are behind barriers (Fig. 1) and at heights (Fig. 2), where safety rules prevent the precise location of the leakage. For these problem areas, a new acoustical imaging type of leak detector can be used.
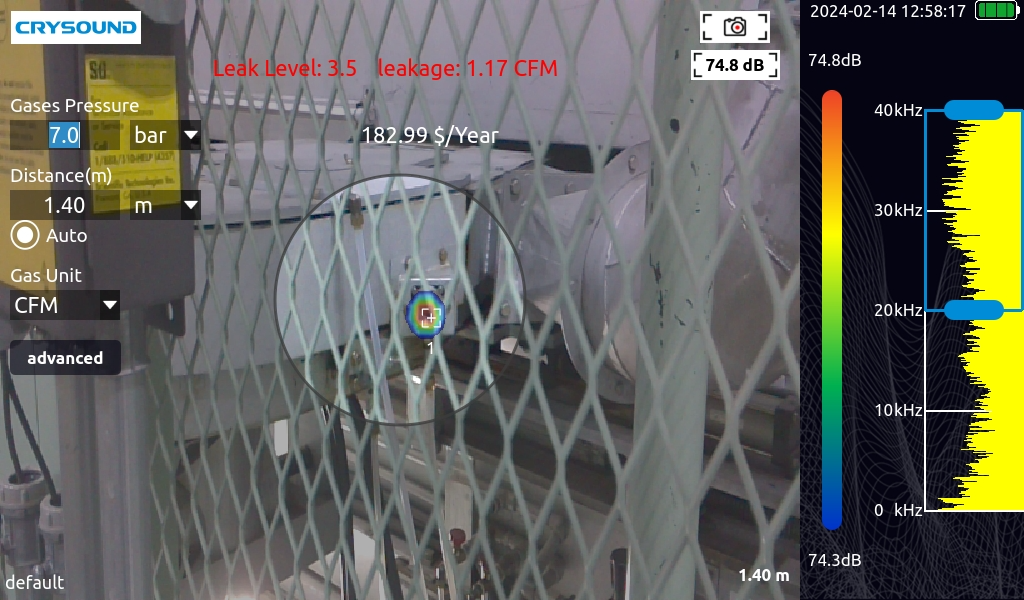
Acoustical imaging air leak detectors utilize advanced technology to visualize and locate air leaks within compressed air systems. This tool combines highly sensitive and directional microphones that detect sounds produced by the turbulence as air escapes from leaks at high velocities using sophisticated imaging software. The device captures these frequencies and processes them into a visual format displayed on a screen, often overlaid on a live video of the machinery.
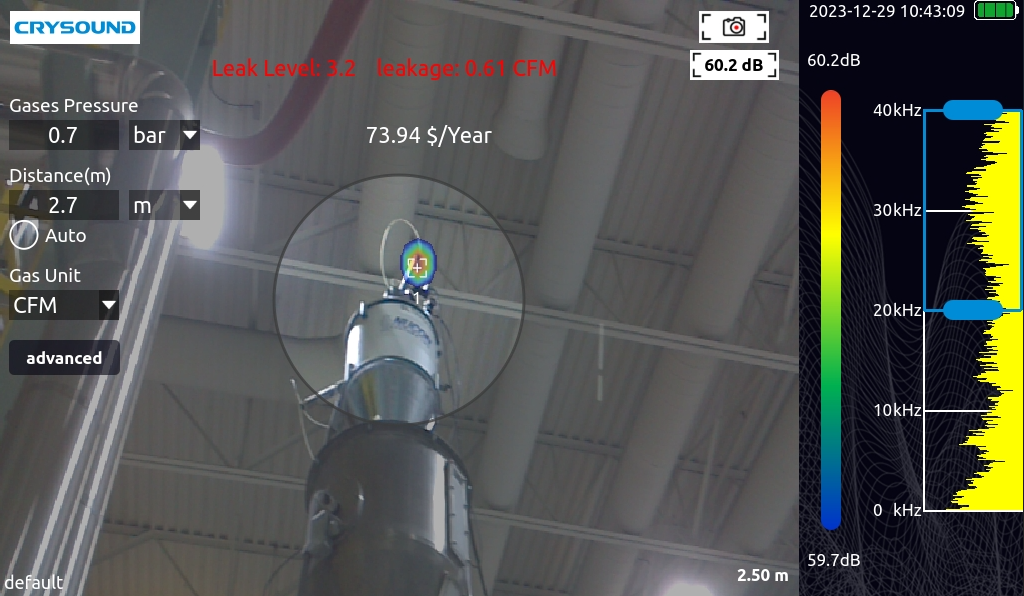
By providing a visual representation of the sound, it enables users to see the precise location of air leaks. This visual approach not only simplifies the detection process but also enhances accuracy, making it easier for maintenance teams to identify and repair leaks quickly and efficiently, thereby optimizing the system’s performance and energy usage.
Some leak auditors have found that efficient leak detection can be performed using both style of detectors, using simple and inexpensive guns to quickly locate general leaks and the acoustical variety to identify exactly the leakage point, capture it on a photograph and calculate the potential savings for the repair, all placed in a database for easy reporting.
Consider the new tools developed for leakage detection, this may save you some significant dollars.
Filed Under: Air Compressors, Components, Components Oil Coolers, Pneumatic Tips