By Josh Cosford, Contributing Editor
The evolution of hydraulic filters from basic, pleated cellulose or paper into today’s synthetic depth media material has been slow but sure. This is because there are only so many ways to trap microscopic particles while offering little resistance to even smaller oil molecules. But engineers are continuing the advance towards high-efficiency filters capable of high dirt-holding capacity with little sacrifice in flow rate.
For ages, our filters were improved with ultra-fine media (5 microns or less), and we continue to improve the dirt-holding capacity of depth media elements. With that in mind, the advancements in filtration are not related to the filter micron rating but the ancillary technologies that improve user experience.
To help me elucidate the progression of trends in hydraulic filters, I asked MP Filtri Canada’s Stephanie Lamb to step in with her expertise on the subject. I asked her how the construction of modern filter assemblies and elements has changed from decades. “Filter housings have been continuously improved to be more compact and lower in weight, while offering equal or better performance.
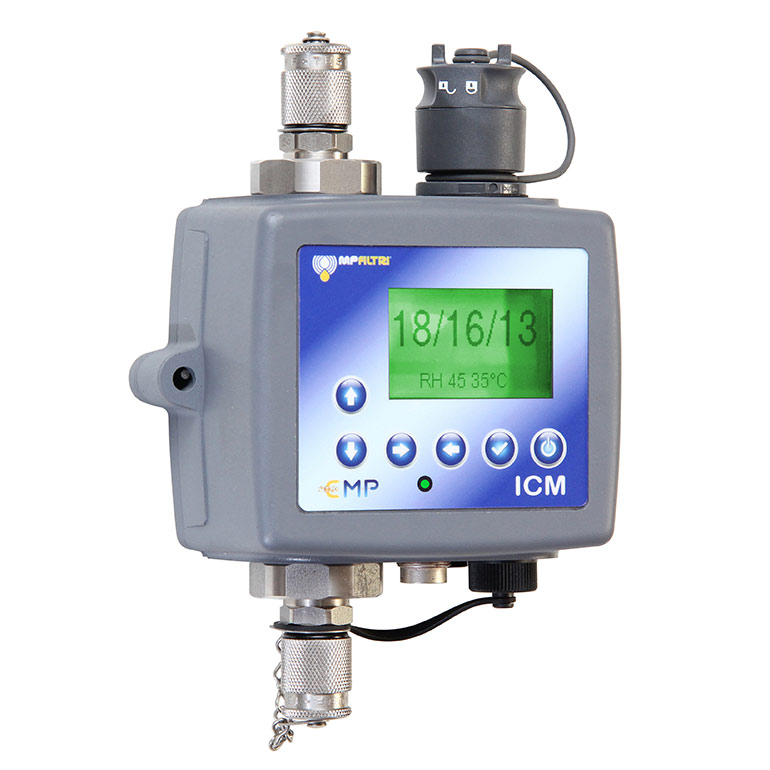
“Filter elements have seen many improvements that provide lower pressure drop, increased dirt holding capacity and single pass efficiency by way of adding one or more additional layers of high-performance filtering media,” Lamb said. “Advancements in media construction specifically in microfiber elements allow for filtering to a lower micron rating resulting in cleaner oil. This has been critical as over the years hydraulic components have evolved to require a much higher performance than in the past to meet the cleanliness requirements of servo and proportional valves.”
Lamb also predicts further advancements in environmentally friendly fluid and filters. Likewise, changes in hydraulic fluid due to environmental concerns have introduced many fluids with lower conductivity. This increases the risk of electrostatic buildup and damaging discharge within the filter. The higher the velocity of the oil moving through the filter element, the more likely this is to occur. Due to this aspect, we now see filters that dissipate these accumulated electrical charges by incorporating conductive material into their design.
The choice of fiber used to make the element’s fabric is not ignored by filter manufacturers pushing the boundaries of what’s possible in a filter. I asked Lamb about new media technology, and she added, “New proprietary media is always being developed and tested to offer the best performance versus cost. The structural design is always under continuous improvement for efficiency, for example, modifying the size of holes in the support tubes and adjusting the pleat design.”
One recent example is melt-blown fabric, a relatively new method of creating filtration media from melted polymers. The process involves the heated material extruded through a small nozzle by high-velocity gas, creating nanofibers that are wrapped onto a drum before processing like many other fabrics. This material provides your usual fine filtration (down to 3 microns) while offering high production capacity without using solvents.
Because the polymer recipes may be altered easily, some melt-blown media also offers water absorption capacity. The limitation of old, cellulose-based water-absorbing filtration was the negative effect on pressure drop. As the water was absorbed into the filter media, it became more difficult for oil to pass, thereby increasing pressure drop. With the melt-blown media, water is absorbed with little effect on the flow rate. Moreover, old cellulose elements were terrible at removing particles, while the new melt-blown elements still enjoy the absolute filtration rating down below 5 microns.
Electrostatic discharge is a problem not often associated with hydraulics. Mineral oil has high electronegativity, which tends to readily attract and rob electrons from other materials. In a nutshell, the movement of oil through the glass fibers of the filter element may create a static charge that could eventually dissipate dangerously. The result may lead to burned and damaged filters, increased oil varnish, or damage to electronic components.
Because of the increased proliferation of electronics in fluid conditioning, ensuring the simple process of oil filtration avoids potential pitfalls. Pressure transducers, temperature sensors, contamination sensors, and other sensitive equipment we use in our Industry 4.0 world must be protected from electrostatic discharge. To spend thousands on a particle counter to supplement your predictive maintenance practices would be wasteful if you took steps to guarantee reliability.
Many high-end filter manufacturers now offer filter elements that reduce electrostatic charging. A combination of filter media and housing materials with neutral electronegativity makes sense when most top filter manufacturers also offer sophisticated electronics for fluid condition monitoring. With such a proliferation of electronics, one would hate to see the basic filter as the prime suspect in electronic failures.
Even with hydraulic machinery operating without electronic support, an electrostatic charge may still cause degradation to the oil itself. As a charge exceeds the fluid’s limit to contain electrons, a spark discharge from the oil to a grounded component creates a localized hot spot. These hot spots may burn or block filter elements but also increase the rate of fluid oxidation. Severe cases lead to varnish or sludge, possibly damaging other system components.
Modern environmentally friendly hydraulic oils eschew conductive additives such as zinc, preventing the fluid itself from carrying away any charge. Unfortunately, ash-free oils also conduct electricity poorly, and the same static charge may occur.
The major filter manufacturers offer elements that do not encourage static buildup in oil. Made from materials that offer little or no charge potential, you no longer must worry about the destructive potential of electrostatic discharge. Electronics, oil, and filters themselves no longer risk spark damage.
Such protection from potentially harmful electrons is necessary for the effort going into Industry 4.0 to be smooth. Lamb had plenty to offer because MP Filtri is a leader in filter-related electronics, adding, “Customers are recognizing that real-time contamination monitoring allows for proactive maintenance.
“For example, as a complement to hydraulic filtration in a system, MP Filtri offers contamination monitoring equipment which measures contamination, temperature and relative humidity in real time and communicates real time data in a variety of communication protocols such as CANBUS and MODBUS, which can be easily adapted into both industrial and mobile equipment.
“Filter indicators, which used to be simple on-off differential pressure switches to advise when an element was at the end of life, are now being designed as transducers, and some are incorporating IoT technology. Customers can see the gradual increase in pressure drop across the filter and monitor on a PLC or even on an app to closely monitor the filter element as it progresses from clean to completely full. Filters in remote locations can be monitored and maintained easily.”
Although appearing simple at first glance, it’s clear that more goes into the design and manufacture of hydraulic filters than first meets the eye. Being such a critical element (pun intended) in any hydraulic system, filter assemblies will continue their path towards higher flow, and finer filtration while offering technology users need to stay relevant.
Filed Under: Components Oil Coolers, Filtration/Contamination Control, Fluid Conditioning, Sealing & Contamination Control Tips, Trending