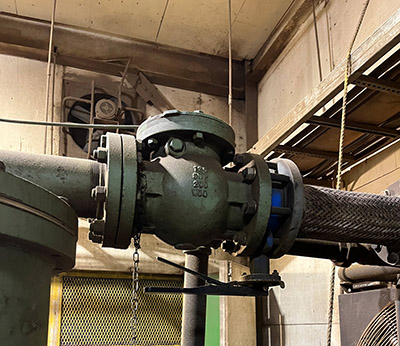
A metal products company had a system of multiple compressors arranged in two compressor rooms. The maintenance workers were having constant problems setting up their compressors to run in a logical sequence. For some reason, the main compressor would never turn off in automatic start, which would allow them to save energy. The big compressor was not needed during evening and weekend load, it was much too large to run at low loads, but it would always stay running.
A compressed air auditor investigated and found the problem was check valves. Each compressor room had a desiccant air dryer to condition the air and there was a piping connection between the wet side of the dryers. To isolate one room from another (so the flow of the large compressor would not go through the small dryer), a check valve was placed in the interconnection. There were also check valves in the desiccant dryer to prevent the back flow of air It turned out that these check valves made the compressor control blind to the true system pressure.
When the compressor would unload and start to time out (go into Auto mode if it remained unloaded for 10 minutes), the various leaks and drains within the compressor room would pull down the local pressure within a few minutes and reload the compressor back up. During light loads, the large compressor would constantly cycle, never really loading much, but remaining running and consuming about 35% of its full load power.
It turns out the check valves were preventing the compressor from “seeing” true system pressure and were interfering with the compressor control. A small hole was drilled into the check valve plate to allow some sensing air to flow back to the large compressor and solved the problem. A large flow was still prevented from going through the small dryer but the compressor could now sense system pressure.
If you are having similar compressor control problems, be sure to observe the location of any check valves in relation to the compressor control sensing point.
Filed Under: Components Oil Coolers, Compressed Air Technologies, Pneumatic Tips, Valves & Valve Manifolds