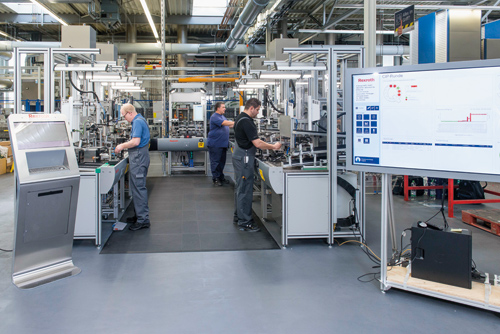
Rexroth’s Smart Automation assembly line and Active Cockpit are seen here at Holmburg/Saar, Germany. The new concept was given the Industry 4.0 Award for pioneering the practical implementation of Industry 4.0.
Smart factories are about more than sensors communicating with each other and with networks. They are about employee safety and comfort, energy efficiency, streamlining operations, automation and so much more.
That’s the message that came through during a recent visit to Morrell Group in Auburn Hills, Mich., as it played host to Bosch Rexroth for “The Smart Factory is Now” tour, an automation open house that brought some of Rexroth’s cutting edge technologies to the United States for the first time.
Morrell and Rexroth invited media to a special preview on Tuesday prior to its open house for 300 customers Wednesday. Scott C. Hibbard, Vice President of Technology for Rexroth began the press conference by saying that a good smart factory will always take into consideration the human in the loop.
Good smart factories, said Hibbard, will optimize all resources via Open Core Engineering—people, energy, machines and raw materials. They will be environmentally smart, using the tools at hand to reduce worker fatigue, pollution, noise and waste. In addition, work must be recorded and measured, and finally, said Hibbard, the predictive element is necessary, as it will help improve processes.
Initially, we learned about Rexroth’s Smart Automation Demonstrator and its “Active Cockpit” concepts, which are both designed to simplify automation work cells. This is the first time the concepts have been shown in the United States. While they are not a particular product line available for purchase, they are concepts being used in Rexroth facilities to demonstrate how its customers can take advantage of its products for smart automation designs.
The Smart Automation Demonstrator features integrated and connected technologies for assembly operations, highlighting many of the company’s linear, electric drive and control, tightening products, RFID tagging and more technologies in one cell. In it, Rexroth employees were able to manufacture a USB drive or a flashlight, showing the versatility in manufacturing as well as simplicity in controls. In addition, it was easy to switch out between a completely automated operation and one with a manual process, which is critical, as most operations require some sort of human intervention. Finally, all of these functions can be monitored via Rexroth’s numerous apps.
The Active Cockpit replaces the traditional whiteboard, mimeograph sheets and the individual reporting functions used on a factory floor and brings all data together in one place, directly to the shop floor. For example, team meetings can be held in which live data from the machine is shared directly with manufacturing and assembly employees. It offers a responsive design and a secure digital connection between the operator, product and workstation, said Rexroth representatives.
Also on display were a variety of newer components and technologies from Rexroth as well as interesting applications from Morrell customers using Rexroth technology. Key to these many designs was the Rexroth technology that can streamline an operation, making it safer for operators and more efficient, whether they used less energy or less time for assembly.
For example, Mark Majewski, Vice President of Automation and Defense Sales for Morrell and Markus Tegethoff, Product Manager for Rexroth, highlighted the company’s Sytronix variable-speed pump drive.
Hydraulic variable-speed pump drives are slowly gaining in popularity in industrial applications, as their power-on-demand design greatly reduces energy and noise output. Using these pump drives can reduce energy usage from 30-80%, with noise reductions of about 15-20 dBA on average. Hearing it run on the Morrell floor, you could hardly tell that a hydraulic power unit designed for clamping operations was just a couple feet away.
Numbers like these make you think everyone would be running out to buy a product that can pay for itself in energy savings in a few years, right? But that’s not the case, said Majewski, who urges more higher-level factory managers to understand the long-term effects of ignoring energy waste in plants.

Rexroth’s Sytronix variable-speed pump drive is used on a hydraulic power unit, offering extreme noise reduction and energy efficiency. Morrell and Rexroth are urging users to learn more about smart hydraulic options such as Sytronix.
As Majewski said, plant managers understand the energy savings but with energy costs being as low as they are and purchasing focusing on cost savings, it’s almost impossible to convince people to try these energy-efficient designs.
Energy efficiency is just the start of what these components can bring to the table. We need to “educate people on what’s available and what could be available,” Majewski said, while Steven Tallman, Morrell’s President, added that energy is cheap here, while our European counterparts are paying sometimes six times higher than what we pay. There they see the need for energy-efficient components. What he said it would come down to in the U.S. will likely be the issue of carbon output and pollution.
Used throughout the Rexroth exhibits was Rexroth’s Assembly Technology. Here is where the very important human element is taken into consideration in smart automation, as users can customize work stations, focusing on designs that are ergonomic, flexible and safe for operators, choosing only the functionality required for their particular operation. This is used in Rexroth’s own facilities and shows how important the person is in what so many consider an automated environment. For example, designs can automatically self-adjust to fit the employee’s height. So even though we’re talking about smart automation, there is always a need for the human element.
As Erwin Wieckowski, P. Eng., Vice President, Factory Automation, concluded, “It (Industry 4.0) has a lot of applications that are hard to imagine right now. (But) the person is still the best machine there is.”
Filed Under: News