By Josh Cosford, Contributing Editor
When installing hydraulic hose assemblies, if tight is good, then tighter is better, right? To be sure a hydraulic hose never accidentally loosens during operation, should we get the biggest pry bar we can find to help lock that hose fitting in for good? Not precisely — torquing your hose fitting is not like desserts at the buffet. More is not better.
The correct answer is, of course, that we want the appropriate torque value for the fitting style, thread form and diameter we’re tightening. Hydraulic hoses connect to ports and adaptors, in most cases, by a thread. Some threads provide only compressive force for thread locking (think ORB, JIC, BSPP and Metric), while others employ a self-sealing taper to both thread lock and provide a pressure seal (think NPT). How torque is applied to the two types of thread forms is vastly different.
In North America, a popular thread form is JIC, which is constructed with conical seats on the female side and a conical face on the male side. When the female is installed onto the male, the mechanical threads are tightened to compress the two conical surfaces to provide a positive metal-on-metal seal. The JIC connection is reliable and reusable, and with the female swivel nut typically installed onto the hose end, the system allows easy installation from various angles.
We use two torque methods for JIC — the flats method and the torque method. The flats method first requires installation of the hose end and subsequent light tightening by hand using a wrench. The technical requires some feel, but expect that if your open-ended wrench had a torque gauge, you would want to aim for the 25-35 in.-lb range. This level of tightening efforts provides a baseline we call the wrench resistance position, so you may continue tightening using the flats method.
From your wrench resistance position, you now refer to the chart below that compares thread size to Flats From Wrench Resistance (FFWR) recommendations. The flats refer to one of the six hex sides of the nut on the hose end. Each movement of a flat position to the next is 60 degrees of rotation, so one full rotation equates to six flats. You can see that every thread size is fully torqued by only 1-2 flats turned. More torque than required will damage or stretch the threads, preventing subsequent resealing or allowing leakage.
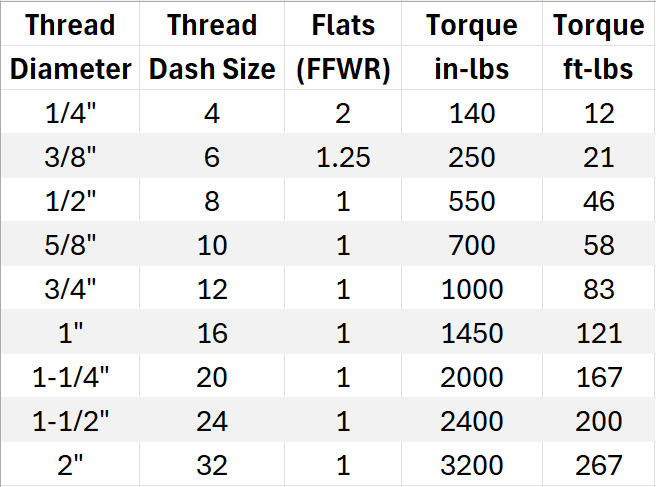
Of course, one can still use a torque wrench, albeit one equipped with a crowfoot wrench, so I’ve also provided the torque values in both in.-lb and ft-lb (note, actually torque can be ± 5%). You can see that for larger sizes of fittings, you’ll need a large wrench and likely an assist bar or tube. The challenge with using the torque method alone is the lack of precision when all the torque factors are unknown. Dirt, finish (plated or not), material (stainless or carbon steel) and oiliness all play a part in achieving accurate torque rather than just excessive friction.
You can use this system for other threads such as BSPP, flat face and ORB. Still, in the less frequent case you have a male NPT thread on your hose, installing it directly into the port requires a similar consideration for torque, but how many turns are applied is vastly different than straight threads.
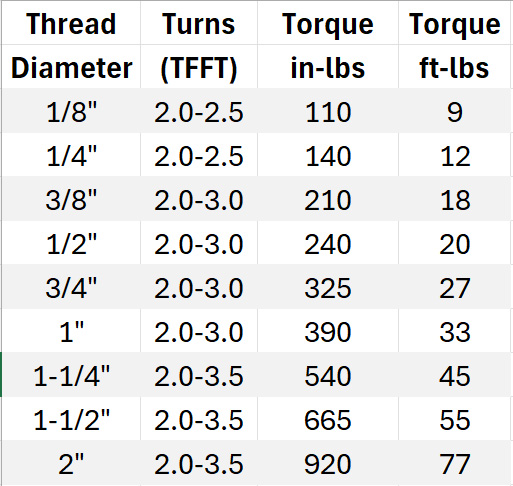
With NPT fittings, we first tighten the thread by hand, which will apply very little torque unless you’re The Hulk. From there, we continue to tighten by full turns to adequately torque the threads. Many technicians have a feel for this, but for the rest of us, the number of turns is provided in the second chart. So, for ½ in. NPT, for example, you’ll need to continue tightening using a wrench until the thread has completed between two and three rotations.
Again, we can use a torque wrench just like with straight threads. The torque values are provided in the chart and are, again, nominal values that may require ±5%. Also again, you must consider how new and clean the threads in question are. Clean, new threads may appear to require more torque to achieve a specified number of turns compared to an old, oily connection that has been torqued previously.
One final tip about torquing hydraulic hose assemblies: be mindful that at least one end of the hose must have a swivel. Trying to tighten one fitting clockwise would otherwise untighten the opposing end counterclockwise. For JIC female ends commonly found on hoses, the nut already swivels. However, for male NPT hose ends, you must request the swivel construction on the last one end.
Filed Under: Components Oil Coolers, Couplings & Fittings, Engineering Basics, Fittings, Couplings & Adapters, Hose & Tubing, Hose Assembly Tips, Technologies