By Josh Cosford, Contributing Editor
Air hoses are vital for many pneumatics-heavy industries, serving as lifelines transporting air to power machinery and tools. However, leakage is a common and frustrating issue that often arises in many pneumatic distribution systems. Leaks hinder efficiency and lead to unnecessary energy wastage and increased operational costs. Thankfully, preventing pneumatic hose leaks is an attainable goal through a combination of proper maintenance, careful usage and the right equipment. Follow these nine tips to prevent air hose leaks.
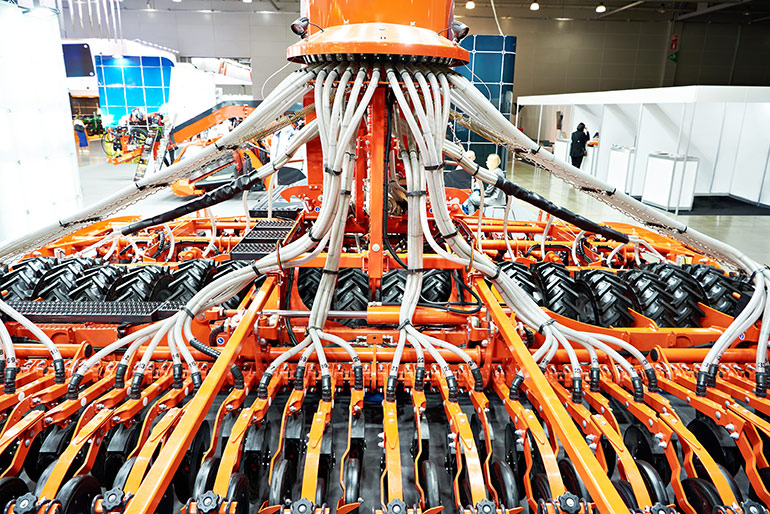
- Select quality hoses:
The foundation of preventing pneumatic hose leaks lies in choosing high-quality hoses from reputable manufacturers. Select only hoses manufactured from durable materials that are resistant to wear, suit your application and are suitable for the ambient and operational temperatures of your plant and machine. Reinforced rubber or hybrid polymer hoses are recommended, as they are less prone to kinks and punctures while offering excellent flexibility and pressure-holding capacity.
- Proper storage and handling:
Improper storage and handling may significantly contribute to pneumatic hose leaks should the hose be damaged from falling objects or long-term UV exposure. Store hoses indoors, away from direct sunlight, chemicals, and extreme temperatures. When a loose hose is not in use, coil the hose neatly, preferably using hose reels, to avoid twists and kinks that can weaken the hose structure over time.
- Regular inspections:
Frequent visual inspections are crucial in catching potential leaks early. Look for signs of wear, cracks, abrasions, or bulges along the hose’s length. Additionally, pay close attention to the hose’s connections, including fittings, couplings, and connectors, as these are common leak-prone areas where the flexible hose meets the rigid metal.
- Secure fittings and couplings:
Properly installed fittings and couplings are essential for preventing air leaks. Ensure that connections are tight and secure, but avoid overtightening, which can damage the hose or fitting threads, especially when softer material is used for the fittings and adapters (such as brass). Use thread sealant or Teflon tape on threaded connections to create an effective seal. Also, remember that NPT should be considered a “one and done” thread connection and is not meant for repeated or frequent installation and removal.
- Minimize abrasion:
Air hoses are often subjected to friction and abrasion against surfaces and objects, weakening the material and leading to leaks. Use protective covers or sleeves to shield the hose from abrasive surfaces whenever possible. This is particularly important in environments where hoses may come into contact with rough edges or moving parts.
- Maintain proper pressure:
Operating pneumatic hoses within their recommended pressure range is vital to prevent leaks, as exceeding the hose’s maximum pressure can lead to stress and ruptures, causing leaks or even hose bursts. Implement pressure regulators and pressure gauges to ensure the air pressure remains within safe limits.
- Address kinks and bends:
Kinks and sharp bends not only impede airflow but also weaken the hose structure, as the kink creates internal stress in the polymer. Avoid bending the hose at acute angles and minimize kinks to prevent potential leaks. If you notice a kink, carefully straighten the hose to restore its integrity, but if your hose maintains a permanent deformation from a long-standing kink, replace the hose before a leak inevitably occurs.
- Replace damaged hoses promptly:
No matter how well you maintain your air hoses, no pneumatic system enjoys infinite plumbing life. If you discover significant damage or wear during inspections, do not hesitate to replace the hose because prompt replacement can prevent unexpected leaks and reduce the risk of operational downtime. Pneumatic hoses are inexpensive compared to the loss of revenue when machines are not producing product.
- Train users:
Proper training for individuals who operate pneumatic tools and machinery is essential to preventing air hose leaks. Ensure your team understands the importance of careful handling, correct storage, and regular maintenance. Educated users are more likely to contribute to the longevity and leak-free performance of your air hoses, especially when they understand the repercussions of a failure.
Preventing air hose leaks demands a proactive approach that encompasses the selection of high-quality hoses, proper storage, regular inspections, and careful usage. By adhering to these practices and taking swift action when damage is identified, you can ensure that your air hoses remain efficient and leak-free, contributing to a more productive and cost-effective operational environment.
Filed Under: Components Oil Coolers, Engineering Basics, Fittings, Couplings & Adapters, Hose & Tubing, Hose Assembly Tips