Using non-welded flange systems, such as Parker’s High Performance Flange connectors, reduces errors and saves hours on installation in mission-critical marine applications.
Hydraulic high-pressure connections in the marine market must withstand harsh conditions, vibrations and other environmental impacts. Traditional welded connections do not always withstand these rigorous demands, and often require time-consuming and costly post-welding pipe inspections and cleaning processes.
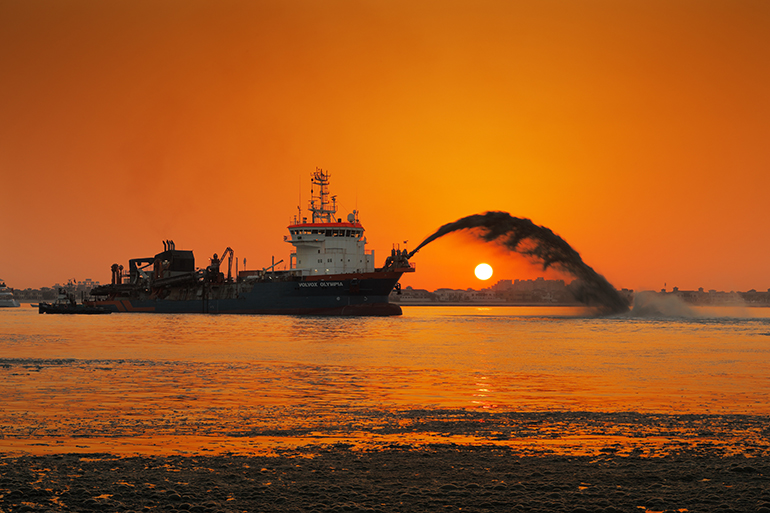
To solve these problems, one can use a non-welded flange system, such as Parker Hannifin’s High Performance Flange (HPF) connectors, which have been relaunched and qualified for marine applications. Within the past year, the HPF has been certified for marine type approvals DNV/GL, LR. The one-piece flange design reduces mistakes and saves time during installation.
These welded systems are used heavily throughout marine applications — from winches to hydraulic doors, engine covers to mooring lines and heave compensating systems and more, on ships used in dredging and oil field development and operations.
Parker‘s HPF System is generally applicable for working pressures up to 420 bar. But the design opens the door to go even beyond this pressure rating: by choosing a suitable combination of flange, insert and tube the pressure rating can be increased to 500 bar. The system is adjusted to standard tube dimensions with diameters from 25 to 150 mm and wall thickness up to 20 mm. It is designed for flange patterns according to ISO 6162-1 (SAE J518, code 61), ISO 6162-2 (SAE J518, code 62) and ISO 6164.
Quick successes are easily proven
According to Thomas Rüdiger, product unit manager (piping), High-Pressure Connectors Europe Division, Parker Hannifin, “We had some great success with a customer in the Netherlands who has now implemented this in their application as a standard way of connecting high pressure pipes. In the Netherlands, they are quite experienced in building different types of ships which you may call dredging vessels. Basically, what they do, they are working on the sea ground, on the sea bed, to move earth to different places.
“On these ships, large poles are lifted up and down, so they are moved down into the ground and then in the front they have some kind of rotating cutter. The ship then rotates around the poles, and then cuts away the sea ground, moving it away to some other place. As you can imagine, there is a lot of hydraulics involved here.”
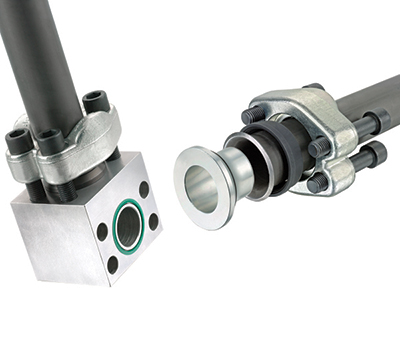
Applications such as this require tough hydraulic systems that can provide extremely high pressures while withstanding extreme vibrations. The HPF is robust, and has good performance when it comes to pressure spikes and vibration. “In these dredgers, as you can imagine, there is a lot of stress because this cutting head is going down into bedrock and it’s working really hard,” Rüdiger said. “If you are using welded flanges or different types of connections, this can lead to weakness, so it can lead to the pipe itself bursting due to wrong welding and so on.”
Ramiz Selimbasic, Project Manager Piping – Parker Hannifin Manufacturing GmbH, added that with the HPF systems, the user cold bends the pipe and cold forms the connection rather than welds the joints. “This is a huge benefit for the customer. You are not adding any additional risk when you are forming rather than welding,” he said. “This was basically the driver behind this customer from the Netherlands. They wanted a system that is safe, robust, and that could handle very high pressures and vibrations.”
Easy, safe installation
“Additionally, what is good is that a customer can do this forming themselves. With the HPF it’s much more flexible, which leaves customers to form themselves and make connections very fast. It’s fast, it’s safe, and it’s easy. This is a big benefit the customers are appreciating,” Selimbasic said. “If you compare the traditional connecting of pipes and also flanges, what has been taking hours we are doing in minutes. If you are welding a single connection on a 4-in. pipe, it can take between four and five hours. With our system we can do this in 30 seconds and it’s 100% every time. And most important, it’s repeatable. It does not require heavy training. It’s simple, so you can find a guy on the street and show them how the machine works and this guy is able to operate it. There is almost zero potential failure for these kinds of connections.”
The HPF system has been well-proven in the heavy press industry, where presses are running 24/7 and at pressures from zero up to 420 bar. To make a connection which can handle this, it needs to be robust and durable, Selimbasic said. “This was the only connection which was able to hold these heavy loads and repeatable surfaces. We were already proven to be robust and reliable. With this new type of approval, we simply are able to sell in the marine and offshore market, because we are certified,” he said.
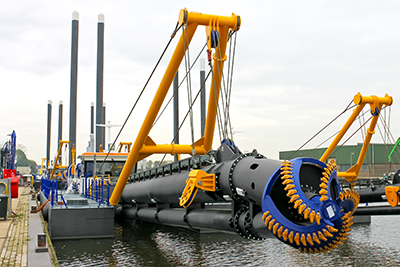
HPF flanges are equipped with a specially designed and hardened inner grip contour, providing excellent additional tear-off safety for the connection. A smooth transition of the flare to the tube and no sharp edges helps reduce any impact from vibration. With the soft sealed system, you simply place an insert in the front of the tube. This insert features an O-ring which is then connected to the tube. The flange itself has a hardened groove and contour inside the flange, which prevents the tube from slipping during operation.
On the port side, sealing is guaranteed by an O-Ring or by the special profile F37 Seal. The F37 Seal was developed especially for use with SAE flanges. These special seals guarantee a high form of stability. Compared to standard O-Rings, their mechanical properties prevent gap extrusion, even when the flanges “breathe” under pressure. The special profile of the F37 Seal is ideally adapted to higher pressures or unsuitable surface finish of the flanges. The application of these soft-sealing elements both on the port side and tube side guarantees the gas leak tightness of the HPF connector. As the insert does not have a toothed profile, it can be easily assembled repeatedly.
Benefits over welded systems
Because mistakes can occur in welded systems, each weld must be tested, which requires extra time before operation and cost increases. High Performance Flanges offer various advantages compared to the welding solution:
- Welding galvanic zinc-plated tubes is always critical. With HPF, zinc-plated tubes can be used, so there is no further painting necessary.
- Welding seams must be descaled and often be stained. Dealing with this process and substances is an environmental risk.
- Welded tubes need to be intensively cleaned inside. HPF tube assemblies do not require any special cleaning, reducing flushing time and costs during initial system startup.
- The flanging process does not cause noxious gases, thus eliminating explosion risks and fire hazards.
- The HPF tube forming is a machined cold forming process. Therefore, there is no need for X-raying the connection.
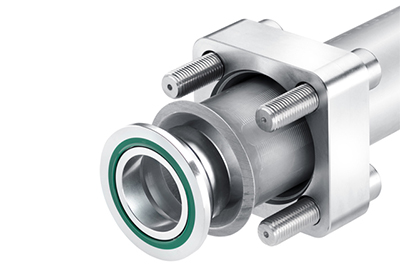
Selimbasic added, “When enlisting customers, what’s mostly appreciated is how easy it is to make big connections, which I already mentioned can take hours and now it takes minutes. You get every time 100% result, and this is what some of the customers are really appreciating, that it is really so easy and fast and it gives you the safest connection that is currently available on the market.”
Additional benefits include:
- No vapors are created in comparison to conventional welding processes.
- Stress corrosion cracking generated during welding operations is non-existent and the life of the finished tubing system is increased.
- Cold formed Parflange technologies save power and energy compared to welding and require neither degreasers nor anti-corrosion agents.
- When galvanized tubes are used, post-galvanization can be omitted because the zinc-coating is not impaired by flaring.
Conclusion
HPF hydraulic connections serve as cost-saving, durable replacements for welded systems. Complete solutions for hydraulic piping systems include the piping layout, drawing design and documentation, the preparation of hydraulic lines in terms of pipe bending, flanging and cleaning up to installation. The service ranges from on-site construction management and assembly to testing, flushing and documenting the entire system.
Parker Hannifin
parker.com
Filed Under: Hose & Tubing, Hose Assembly Tips