Static sealing elements are used practically everywhere in daily life, although they typically go unseen. And while sealing technology expertise is limited to a relatively small group of specialists, mechanical and fluid-power engineers must be able to apply the fundamentals to ensure successful designs.
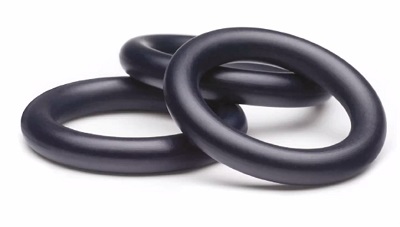
In a recent webinar, “Sealing Solutions for Static Applications,“ Thomas Braun and Christoph Meissner with the Prädifa Technology Div. of Parker Hannifin’s Engineered Materials Group, provided insights into the wide variety of available static seals and influencing factors that affect seal selection. These involve both technical and economic considerations, such as the type of fluid, operating conditions and environment; material formulation, properties and production methods; and design of the mating surfaces and seal geometry.
Based on a customer’s requirements, engineers can define the preferred polymer families, said Braun. “Subsequently, the final selection of the sealing material and seal design will be influenced by other factors such as geometric limitations, ease of assembly, and expected service life, plus fluid compatibility as well as chemical and physical material properties,” he said.
To select a suitable sealing element it is imperative to know, at a minimum, the system pressure, temperature range from lowest to maximum, and the type of fluid and its additives. “In addition, up to roughly 200 other influencing parameters, plus their combinations, may be relevant for the operational reliability of a sealing system,” said Braun.
Fortunately, a wide variety of static sealing solutions are available today, he continued. Static sealing can basically be achieved by inseparable connections, for example adhesives, bonding and welding; and by separable elements that rely on resilient components. Here’s an overview of resilient seals for radial and axial applications across a wide range of pressures.
O-ring benefits
“The O-ring, no doubt, is the most commonly known and used type of seal,” said Meissner. “There are a range of good reasons for this. Let’s start with the simple design. The whole geometry can be defined by two dimensions: a diameter and cross section. In addition, the round cross section offers optimal functional prerequisites for ensuring high sealing performance combined with ease of handling.”
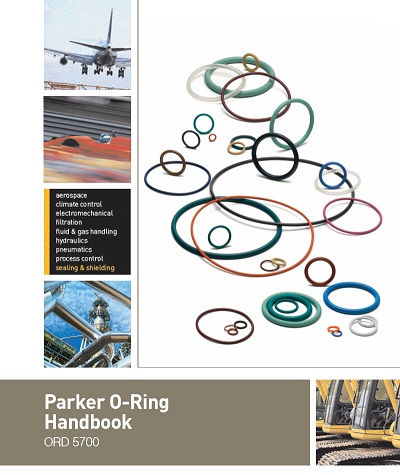
The elastic material generates a sealing force when squeezed during installation. “This force can equalize irregularities in the sealing areas and compensate for slight movement between components. In this way, a wide range of media from greases to liquids to volatile gases can be reliably sealed off. When such media are pressurized the resulting force is optimally transferred via the round cross section to the sealing areas,” he said. This pressure-generated force combines with the compression force inherent in elastic material, resulting in value that is always higher than the pressure. “This is the principle which the reliable sealing performance of O-rings is based on,” said Meissner. “Pressure supports the sealing function.”
The seals require minimal space and are highly economical. Standard O-rings are generally available for pressures to 160 bar (2,321 psi) and with an operating temperature range from -50° to 300° C (-58° to 572° F).
The variety of O-rings is as wide as their range of applications, Meissner continued. That’s why efforts to standardize dimensions have been underway for a long time. The most important series of dimensions have their origins in the U.S. aviation industry and the AS568 Standard covers most O-rings, materials and applications. ISO 3601-1:2012-03 also provides O-ring dimensions, tolerances and designation codes.
“Conformance of the component design to the technical specification is of crucial importance,” said Meissner. Likewise, selecting the proper material for the relevant application is also critical. Unfortunately, a universally usable sealing material does not yet exist. “Even the most expensive variants have technical disadvantages that make them unsuitable for some applications,” he said.
Thus, Parker makes rubber O-rings across a number of material families, including butyl-butadiene, chloroprene, EDPM, FKM, nitrile, polyacrylate, polyurethane, SBR, silicone and fluorosilicone. Parker Prädifa has more than 200 different formulations that are actively being used, he added.
“A number of criteria have to be observed in the selection of the right O-ring material. They include the minimum and maximum operating temperatures well as the media to be sealed and system pressure in the application,” said Meissner. Basic elastomers can be roughly classified with regard to operating temperatures. The minimum operating temperature is determined by the material’s cold flexibility, as elastomers become harder at low temperatures and lose their elastic properties. Select the wrong material and the O-ring may leak. “However, this effect is reversible. Typically there will be no damage to the seal. As temperature increases elasticity and sealing performance return, so that low transportation or storage temperatures do not normally pose a problem,” he said.
“On the other hand, very high temperatures have a lasting effect on elastomer materials.” These materials become softer at high temperatures and are more prone to damage due to mechanical loads such as media pressure. And high temperatures accelerate aging of the material. In this context the correlation between temperatures and media is of crucial importance, said Meissner. In addition, harmful influences such as water in the hydraulic oil can accelerate aging, particularly at high temperatures.
To assist engineers, the Parker O-ring Handbook contains the fundamentals of O-ring use as well as key material and design recommendations, he said. And the company’s O-ring Selector software serves as a quick guide and design aid, and it recommends materials based on application data.
Back-up rings
Next let’s consider anti-extrusion back-up rings. Relatively soft seals, like most O-rings, are particularly effective, but they are prone to damage by high pressures. And mating parts rarely fit perfectly together. Instead, there is a small gap that must be sealed to prevent leaks. While the gap can be minimized in the design, this is often undesirable and costly. So at high pressures, a soft seal heavily deforms and behaves like a liquid, fully filling the available space. If pressure pushes the seal into the gap, the seal may fail. This is called gap extrusion.
Using a harder material is a possibility, said Meissner, but it may have negative effects, such as a loss of flexibility that increases leakage. “A division of labor is another possible solution. In this case, the seal exclusively performs its sealing function while a back-up ring performs the task of resisting the pressure.” The back-up ring can be a much harder material, and the seal can deliver long service life, even at high pressures and high temperatures.
A back-up ring ensures that the gap remains closed. Under pressure, it is pushed in front of the gap by the seal, which closes the gap. Even if the backup ring itself should slightly extrude, the seal function would be retained and the sealing area would remain intact. It’s important, of course, that the backup ring is installed correctly on the non-pressurized side. Two backup rings are needed for double-acting applications or to avoid improper installation, said Meissner.
Thus, the hard back-up ring prevents extrusion, increases pressure resistance and extends the life of heavily loaded sealing systems. Depending on the application, temperatures and pressures, there are various materials and designs of back-up rings. Particularly common are simple rectangular PTFE rings, slotted or unslotted, and Parbak rings which, adapted to the standard O-ring dimensions, are low cost and readily available.
In special applications with equally special requirements, high-performance polyamide or PEEK plastics are sometimes used. For instance in the oil and gas sector extremely high pressures, sometimes up to 1,500 bar (21,756 psi) along with aggressive media, are not uncommon.
In Part 2, we’ll look at alternatives to O-rings for static sealing.
Parker Hannifin
www.parker.com
Filed Under: Sealing & Contamination Control Tips