Moog has received certification according to NEC 505 from FM Approvals for its full line of Digital Control Servo Valve products including the D636K to D639K, D671K to D675K and D941K to D945K series, which customers can use with onshore and offshore oil and gas drill rigs. This product family also holds the ATEX and IECEx certifications.
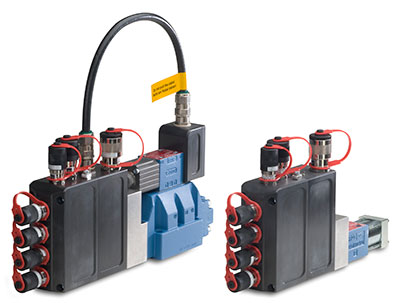
D672K (left) and D636K (right) series digital control servovalves from Moog
Moog explosion-proof digital control servo and proportional valves provide intelligent closed-loop motion control (with either analog or fieldbus interfaces) and optimize equipment functionality. The product family includes designs for flow control and pressure and flow control; Moog also has axis control versions available. The pressure and flow control valves have a pressure transducer integrated in the valve to access the optimum sampling position. On-board electronics monitor the valves in an internal closed loop control to create the pressure control. This capability often enables the user to use one valve instead of two, (i.e., defining minimum or maximum pressure, while controlling flow or controlling pressure with defined limits to the flow) offering users flexibility and cost-savings.
Rated flow depends on option selected either at ∆pn 35 bar/spool land (500 psi/spool land) or at ∆pn 5 bar/spool land (75 psi/spool land). They are rated for maximum operating pressure 350 bar (5,000 psi). They are available as 2-way, 3-way, 4-way, 5-way and 2×2-way versions.
These explosion-proof Moog digital control servo and proportional valves can be used for a range of applications in offshore and onshore oil and gas exploration and production, including control of:
- A rotary table on the deck of a rig during the drilling process, which provides rotational torque to a drill string throughout the process of drilling a borehole.
- A draw-works which are used to hoist and lower drilling pipe into a borehole.
- An iron roughneck that connects and disconnects pipe segments used in a borehole.
This product family provides CAN/CANopen, EtherCAT and PROFIBUS fieldbus connections, which equipment builders and operators find easier for controlling drilling machinery at a high-performance level in potentially explosive environments.
Moog has extensive experience designing and manufacturing products for demanding environments and first introduced certified valves for use in explosive environments in 1972. Advanced digital technology with parameter setting, condition monitoring and remote diagnostics enables equipment builders and operators to maximize uptime in operations.
“In North America, it’s critical for oil and gas manufacturers, operators and technology suppliers to meet NEC 505 — the electric code for locations where hazardous, flammable gases may exist,” said Craig Jackson, regional sales manager for Moog’s oil and gas market. “With this series of Moog explosion-proof servo and proportional valves having passed the full-hazard area test protocols, machine operators can rely on us to build a compliant system on their rigs.”
“We’re not just selling certified servo valves,” added Jackson. “Moog is a solutions provider with engineers across North America and the globe who assist customers to identify their application requirements. Moog engineers are experts in designing motion control components that meet the customers’ application parameters and stringent hazardous area requirements.”
The newly certified D636K to D639K, D671K to D675K and D941K to D945K series digital control servo and proportional valves are also suitable for applications in potentially hazardous environments like power generation and chemical processing.
Moog Inc.
www.moog.com/industrial
Filed Under: Valves & Manifolds