Technology advancements enable smaller, quieter, and more energy-efficient hydraulic power units that save space and reduce the total cost of ownership.
The common perception of conventional hydraulic power units is that they are large, loud, and inefficient. Such claims are valid for facilities that still use power units from the 1960s and 1970s and among engineers unaware of the latest technology. However, the notion that hydraulic system designs are static in time is an outdated misconception. With the new CytroBox and CytroPac, Bosch Rexroth aims to educate machine builders on modern hydraulic power unit advancements and inspire a shift in perspectives.
The CytroBox and CytroPac defy traditional hydraulic power units with their compact, quiet, and energy-efficient designs. They include small “smart” pumps and motors that only run when needed and at low torque when not in use. The smart pump and motor group reduce heat generation and makes the system run more efficiently.
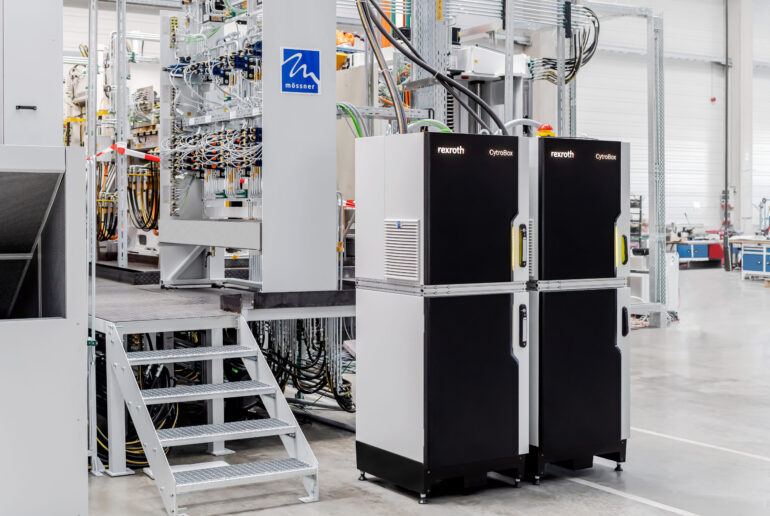
Modern hydraulic power units are compact, quiet, and energy efficient. Image courtesy of Bosch Rexroth.
While common industry opinions may deem it difficult to work with such newer technology, modern units like the CytroBox and CytroPac require less maintenance and reduce the total cost of ownership compared to older, conventional units. Though newer technology might incur higher upfront costs, long-term cost savings related to maintenance, commissioning, and energy add up. Not to mention, the new systems are quiet and simpler to control.
Compact size without compromising power
For some applications, space is scarce, and systems require smaller footprints. Conventional hydraulic units vary in size and can be as large as Olympic swimming pools, necessitating vigilant monitoring and maintenance to cover the physical span.
In contrast, the CytroBox looks more like a refrigerator, standing just under 8 ft high. Its maximum pressure is 315 bar, and machine designers can tie multiple tanks together to create a tandem system and increase flow. Each unit’s performance ranges from 7.5 to 30 kW and can be installed into existing production lines.
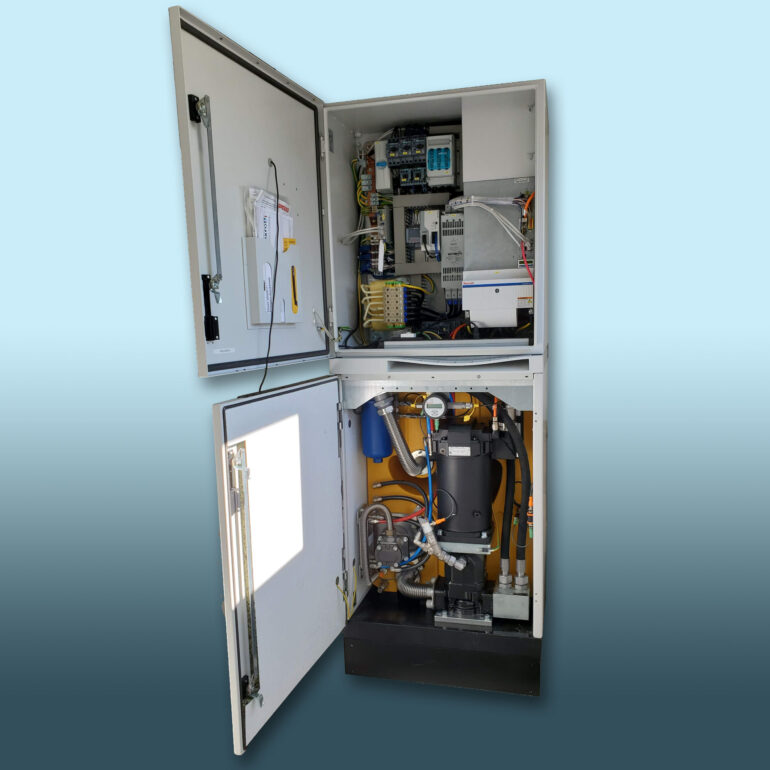
The CytroBox stands just under 8 ft high and uses a small motor and variable-speed pump to reduce energy consumption. Image courtesy of Bosch Rexroth.
For extra space savings, the CytroPac is nearly 24 in. high with a diameter slightly greater than 14 in. The CytroPac provides up to 240 bar of pressure and a performance range of 1.5 to 4 kW. “You could probably stack six or seven CytroPac units in the corner of a plant and not take up any space,” said Tyler Stahl, application engineer and Cytro product specialist at Bosch Rexroth.
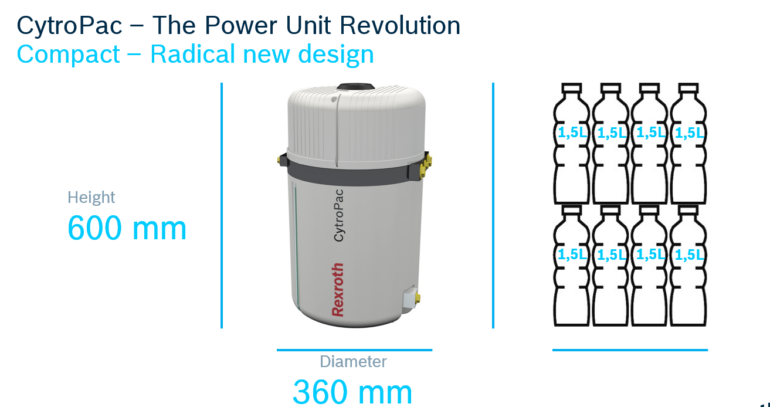
The CytroPac is small but mighty and simpler to operate without needing complex hydraulics knowledge. Image courtesy of Bosch Rexroth.
Quiet operation with visual indicators
Hydraulic units are typically loud, which causes safety hazards and requires anyone near them to wear earplugs. However, the CytroBox is so quiet that its operation can go audibly unnoticed. This means testers can sit next to the unit instead of in a different room for test applications, and operators can hold conversations without yelling at each other.
The significant noise reduction is attributed to advanced motor and pump designs and system components that help dampen noise within the box. The CytroBox uses small motors and pumps that operate at high speeds and reduce motor torque. Improved piston pump designs, quieter internal gear pumps, and reduced average motor operating speed decrease the average hydraulic system noise levels by more than 10 dB without requiring sound enclosures. Additionally, the CytroBox has a special housing that helps capture noise, and the bottom of the box is made of polymer concrete to help dampen motor vibrations.

The CytroBox reduces oil consumption by 75% and noise levels to less than 75 dB. Image courtesy of Bosch Rexroth.
To monitor operation, LED lights outside the CytroBox and CytroPac indicate green when the system is running, yellow when it’s stalled, and red when it’s not running. Replacing audible cues with visual indicator lights may concern those who favor more conventional systems, which often “speak” to operators and maintenance engineers through various pitched hums. However, LEDs provide discrete and immediate monitoring capability, which is common and favorable among electromechanical drives and other modern equipment.
Smart pumps provide energy efficiency
Pumps and motors in older hydraulic units constantly run at full capacity regardless of the application’s requirements. Therefore, a few decades ago, engineers developed “smart pumps” to run at variable speeds and improve energy efficiency. These pumps were designed to control flow and pressure in a system by varying the displacement (volume per revolution) as needed. Advanced calculations within the pump controller determined the flow and pressure. Widespread use of variable-speed hydraulic drives propelled improvements to this smart pump technology.
Newer versions can calculate the most efficient combination of pump displacement and motor speed based on flow demand. The smart pump electronics send a speed command directly to a motor VFD without the need for any programming in the machine PLC.
More recently, smart pump advancements include speed-controlled fixed displacement pumps, which use efficient variable drive speed but can’t vary the pump displacement. In some designs, the machine PLC must include the needed hydraulic calculations for motor speed based on both flow and pressure. However, the Bosch Rexroth version of this type of smart pump includes flow and pressure calculations in the electric drive (both VFD and servo drives), eliminating the need for complex PLC programming.
Software tools that compare hydraulic drive solutions and display the energy consumption differences allow hydraulic system designers to model a machine cycle and optimize the pump and motor to achieve the highest possible energy savings.
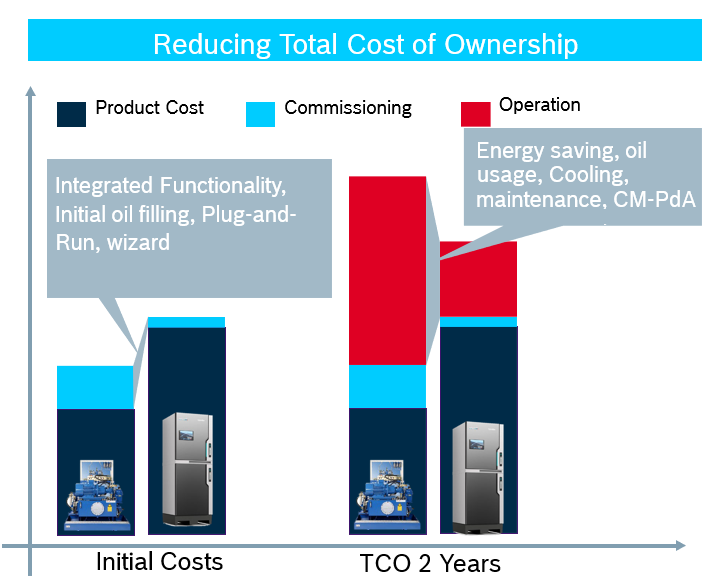
Though the modern hydraulic power unit may have greater upfront costs, the total cost of ownership is less than conventional units. Image courtesy of Bosch Rexroth.
Simplicity yields more space savings
The CytroBox is more of a valveless design that eliminates the need for proportional valves, which help control flow and pressure but can be expensive. Machine builders can still mount valves on the back of the unit if desired or needed. The CytroBox also has a built-in, sand-casted manifold that helps optimize flow and reduce pressure loss and heat emission.
Both the CytroBox and CytroPac use mineral oil HLP, which is a commonly used fluid. Being more compact, these systems use less oil, reducing the quantity facilities need to maintain. The CytroPac has a 20-L tank, and the CytroBox has a J-shaped, 150-L reservoir designed to help degas any trapped air bubbles in the fluid.
The CytroBox comes with either a 4- or 10-kW cooling option. The bottom of the cabinet has a built-in heat exchanger with a kidney loop that distributes cooling water. Add-on packages and products can also be installed on top of the CytroBox to create a fully closed cooling system if a facility doesn’t have water to supply to the unit.
Industry 4.0 integration
In conventional units, machine builders manually wire the motor, pump, cooler, and reservoir to an HBU control for the motor conductor, sensor analysis, and the safe torque off (STO). Comparatively, the CytroBox and CytroPac are prewired and include a multi-ethernet connection for integration with any network.
Additionally, all Cytro units include CytroConnect, a digital monitoring system that displays a unit’s operation and performance dashboard. System owners can pull up the dashboard on any desktop, laptop, tablet, or phone to locate the unit and assess operation in real time. Optional paid add-ons are available to monitor fluid cleanliness, system overheating, and other system parameters.
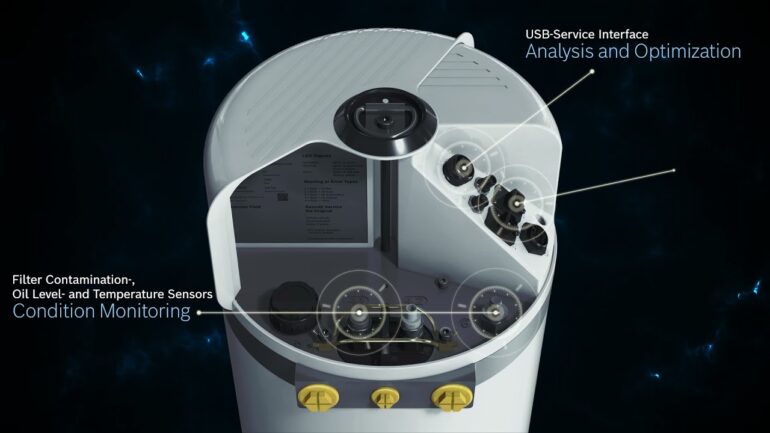
Sensors inside the CytroPac unit detect fluid contamination, oil level, and temperature for continuous monitoring and maintenance scheduling. Image courtesy of Bosch Rexroth.
“There have been cases where someone logged into CytroConnect to look at a unit while the shop was down during a holiday break and noticed that the heat was rising above their preference,” said Stahl. “A technician went out and observed that the cooling water was dumping backward. This saved them from destroying the whole unit and losing money on machine downtime.”
Paid monthly add-ons are more advanced and help detect when a part will fail. For example, a leakage sensor can notify when a part is determined to fail so that owners can predict maintenance, downtime, and component ordering and replacement schedules.
Holding high pressure longer
The compact hydraulic power units, especially the CytroPac, were initially intended for machine tool applications. Manufacturers can keep 10 to 15 CytroPac units on hand because they’re smaller, convenient to store without taking up much space, and easy to swap out as needed.
Pressing applications benefit immensely from CytroBox’s power and energy efficiency, as the pump and motor group help hold pressure for longer. Holding high pressure with equal-sized traditional hydraulic systems consumes approximately 5 kW of power. With its servo motor technology, the CytroBox can hold high pressure while consuming extremely low power (less than 0.5 kW), potentially yielding 90% energy savings during pressure holding compared to a traditional system.
Bosch Rexroth
boschrextroth.com
Filed Under: Industry 40, News, Pumps & Motors, Trending