There is no problem, goes the current wisdom, which some federal program won’t try to solve by throwing money at it. That is, unless it means devoting dollars for research on traditional manufacturing processes.
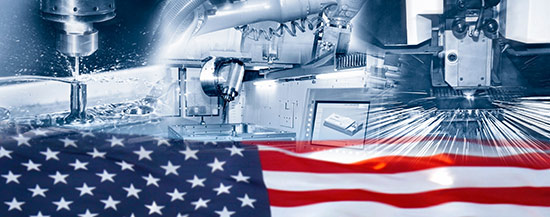
Image courtesy of AdobeStock
Take, for instance, the National Science Foundation, a government entity that supports fundamental research and education in all the non-medical fields of science and engineering. It has an $8.8 billion budget and awards hundreds of millions of dollars annually in so-called “next-generation” projects — this year $900 million for climate change and clean energy technology, $636 million on artificial intelligence research, $435 million on nanotechnology and $220 million on quantum information science. It will even spend $50 million for new STEM workforce diversity initiatives.
But when it comes to funding research for more-conventional operations like forging and casting, support is harder to come by. Meanwhile, countries like China and Germany spend generously on manufacturing R&D, labs and researchers because they understand investments that advance manufacturing technology ultimately strengthens their economies, fosters growth and maintains their standing as export powerhouses.
That’s why the NSF’s recent announcement of up to $52 million in funding for a new Engineering Research Center is a big deal. Dedicated to developing and commercializing advanced, intelligent production systems, the Hybrid Autonomous Manufacturing, Moving from Evolution to Revolution (HAMMER) ERC — of which fluid power promises to be a key contributor — will help grow a next-generation American manufacturing industry and ease national security and supply chain issues, according to the NSF.
HAMMER’s primary goal is to create hybrid manufacturing systems such as for metamorphic manufacturing. MM is essentially autonomous open-die forging where servohydraulic-driven tools repeatedly and incrementally form a piece of metal that is precisely positioned by a robot. It is seen as a cost-effective way to craft intricate parts with specific engineering properties and locally defined microstructures based on well-understood metal-processing methods, and is suitable for rapid customization of everything from small medical implants to extremely large structural components.
Proponents say compared to CNC machining and additive manufacturing, MM is faster and produces parts with higher strength and toughness, with less waste and requiring less energy. And it could lower the economic barriers many small- and medium-sized manufacturers face and help expand domestic production capacity.
On the development curve MM is just in its infancy, akin to CNC machining in the 1940s. But it is building upon a well-established knowledge base encompassing sensors, heat-treating methods, hydraulic actuators, robots and high-speed processors. Experts say that given adequate funding, there is no reason these various elements cannot be quickly melded together as a useful and practical manufacturing technology. After all, the idea of integrating robots and tools with sensors and software, the essence of IoT, is increasingly being embraced across the industrial landscape.
The Defense Department is paying attention, too. It views forgings and castings as one of the most critical vulnerabilities to national security. Forged and cast components are essential in everything from ships and subs to aircraft, combat vehicles and weapons systems. But due to offshoring and industry consolidation there are relatively few domestic suppliers of many mission-critical components. Thus, DoD counts on foreign countries, including China, for very large cast and forged products found in some defense systems. They’re also essential components that go into many of the machine tools and presses used to make such parts.
Industry and government leaders alike view as a major problem the fact that the U.S. has ceded much of its manufacturing base to China. It puts us in a precarious position vulnerable to supply chain disruptions and security threats. Producing critical goods domestically, which HAMMER envisions, would go a long way toward creating a more-vibrant domestic industrial capacity to bolster national defense and ensure long-term economic competitiveness.
Filed Under: News, Trending