High pressure defines hydraulics, and the linear actuator we call the cylinder is the pièce de résistance of our industry. Other methods of creating rotational force may closely mirror the performance of a hydraulic motor. Still, a hydraulic cylinder has no peer for linear force (I’m looking at you, electric linear actuator). The force advantage grows when so too does the pressure.
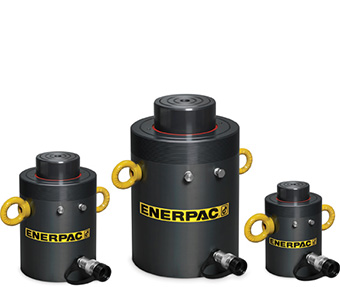
High Tonnage Cylinders from Enerpac
High pressure is subjective. If you balance a small car on a 1.15-inch diameter pole, only a fool would say the pressure under that single square inch area isn’t high. Yet, even at 3,000 psi, many do not even consider this the realm of high-pressure hydraulics. Indeed, even some construction equipment runs upwards of 6,000 psi. A truly high-pressure cylinder is one compressed to upwards of 10,000 psi or more.
The high-pressure hydraulic tool industry runs its components at 10,000 psi all day long. The “jaws of life” you see so quickly decapitate a sedan after a collision are provided with their superpowers by high-pressure actuators. These duckbill-looking tools spread door frames like Play-Doh, and the cutting tool is their cousin, which can slice through roof pillars like butter. The high-pressure tool industry does away with describing their cylinders by their bore size or pressure capacity and jumps right into describing them in tons.
The high-pressure tool industry’s favorite cylinder design is the ram. A ram uses a rod with no piston, making its construction quite simple. So long as the fluid is sealed around that rod, pumping in oil from any location will force the rod to extend, albeit very slowly. The tradeoff with high-pressure cylinders is speed. An actuator moving quickly at extreme pressure is a recipe for seal failure through extrusion, which is why these tools often move slowly.
The higher the pressure you run in a hydraulic actuator, the more force it can offer, so long as it’s constructed to handle that pressure. As a result, the hydraulic tools are fairly compact and portable. In fact, the cylinders and pumping system used to lift an entire house will fit into the back of a pickup. These single-acting rams are placed at structurally critical locations under the foundation of a house to either work on its foundation or move the entire structure to a new location.
Making these high-pressure cylinders with double-acting construction would reduce their force capacity in both directions, requiring a smaller rod for the differential area on the piston, which also reduces its column strength and force capacity upon extension. High-pressure cylinders retract with springs, requiring only the valving in its pressure line switchable to tank. Some applications offer double-acting actuation, of course, but grow in size and complexity. However, they offer a high-pressure option for tensioning applications, such as a bearing puller or vehicle frame straightener.
Of course, not all high-pressure cylinders are used in the tooling industry. For example, I recently worked on a cylinder application for an aerospace customer who needed a hydraulic actuator capable of withstanding more than 20,000 psi of static, load-induced pressure. Used for testing, the cylinder positions a test fixture and then is subjected to high force loads, which are transferred to the cylinder.
Run by a standard 3,000 psi power unit, we only tested the cylinders to 10,000 psi. It is made from extraordinary, high strength, heat-treated material and employed tie rods as thick as the piston rod. We machined the rear clevis lap from a single piece of raw material, each taking over 30-hours of CNC milling time alone. High-pressure tie-rod cylinders are rare because tie-rod stretch becomes a problem, but this cylinder was designed to remain sealed even at a ¼ in. of tie-rod stretch.
Filed Under: News