An O-ring is a polymer seal most often used in fluid power as either a dynamic or static seal. For light-duty pneumatic applications, an O-ring is a suitable seal technology used in pistons, piston rods, valve spools and other locations in air systems. O-rings best suit the sealing of static surfaces in hydraulic applications, such as cylinder barrel end seals, pump covers, and manifold interfaces, to name a few.
Static O-ring seals have but one job; prevent air or hydraulic pressure media from escaping cylinders, valves, pumps and other components. You must correctly design its cavity and choose the correct seal diameter and cross-section to suit that pocket. An O-ring must be squeezed upon installation, but not so much as to damage it. Additionally, the seal’s rubber compound must be selected with fluid and temperature in mind since even correctly sized seals will fail when poorly matched to its ambient conditions.
Understanding the top five reasons O-rings fail will help you ensure long-lasting designs.
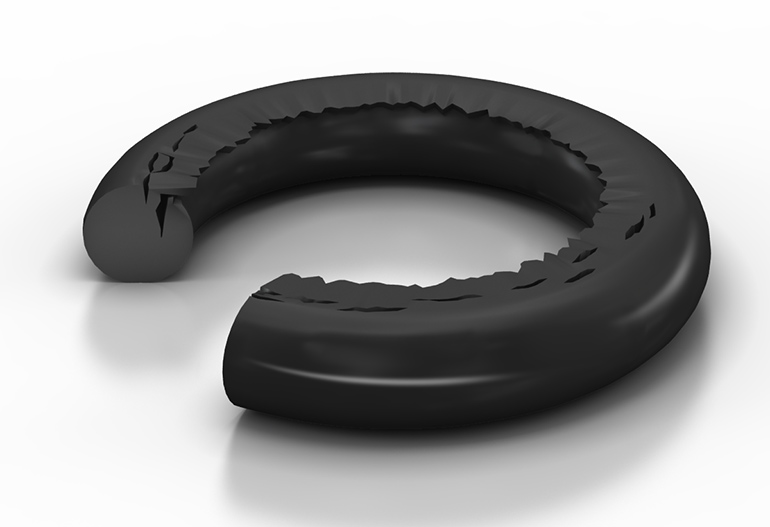
- Improperly designed seal pocket. A seal must reside slightly compressed within a cavity to prevent extrusion through the clearance between each surface. The space between the two sealing surfaces is called the extrusion gap, which cannot be too large. If the “E-gap” is too large, the pressure internal to the component may squeeze the rubber material out through that gap. This “nibbling” of the seal takes the form of a delicate ribbon of rubber trailing off the O-ring circumference.
- Seal too small. A seal too small for its designed pocket will not crush effectively and simply allow fluid to pass. This type of failure tends to occur quickly as the seal cannot form effectively to the pocket to prevent fluid bypass. Even if the size is marginally smaller than required, the seal will fail sooner than the correct one.
- Seal too large. If a seal is too large for its cavity, the component may never seal properly to begin with. For example, installing a piston rod into a cylinder head may be impossible if the O-ring is too large. A marginally larger seal may still allow installation to occur but will fail as the seal is compressed tighter than designed. An O-ring must be compressed enough to fill its cavity, but too much compression deforms the seal into a rectangular shape as it loses its elasticity.
- Incorrect temperature compatibility. The polymer of the O-ring must be selected to work within the specific temperature range for the application. A Buna Nitrile seal used in a cold environment results in the hardening of the O-ring, and it loses the elasticity required to conform to the shape of its cavity.
An example of thermal degradation O-ring failure, damage caused by excessive heat. Image courtesy of Trelleborg Sealing Solutions Conversely, when you expose a seal to hot ambient conditions, it may become too soft. A hot O-ring may turn gooey and will easily extrude through small E-gaps, especially in applications where the E-gap can change, such as with O-rings used as end-seals in hydraulic cylinder barrels.
- Incorrect fluid compatibility. Not all seals work with all fluid media, and your seal polymer must be compatible with the fluid type. Many hydraulic applications using urethane seals and standard hydraulic oil will see no issues regarding compatibility. But if the fluid turns out to be water-glycol, for example, the urethane seals will crack or break apart.
Filed Under: Sealing & Contamination Control Tips