Machine manufacturers are increasingly looking for ways to improve the efficiency of fluid power systems, both for sustainability reasons and for the bottom line. At last month’s NFPA/FPIC quarterly meeting, Neal Gigliotti, Manager, Applications at Bosch Rexroth Corp. discussed some environmentally friendly techniques for advancing industrial machinery designs, and why they’re important.
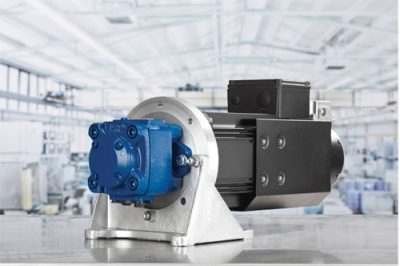
Variable speed pump drives, such as Bosch Rexroth’s Sytronix SvP drive, can reduce energy consumption and noise in industrial settings.
“Making hydraulics eco-friendly saves energy, which is direct cost savings,” said Gigliotti. “It also reduces carbon footprint, which in many corporations, especially the larger ones, is a high priority item nowadays. You can only replace so many light bulbs with LEDs before you need to do something different, and running hydraulic systems can be costly from a carbon footprint standpoint.”
According to Gigliotti, traditional hydraulic systems used in industrial machinery are designed to be inefficient. It’s a provocative statement, he said. “But it’s not untrue. In almost all applications, using fixed-speed electric motors to drive pumps adds a significant energy offset, meaning you need extra energy. That’s because if you’re not using full flow from a pump, then running that pump at full speed the full time is inefficient. You’re not doing work, you’re just generating heat.”
For instance, traditional solutions often involve a fixed-speed motor driving a pump and throttling flow with a valve to move a cylinder. The motor draws high current and heats up because it runs constantly at full speed, even under partial load. The pump sustains losses because it continuously rotates a fairly heavy mass that’s not doing anything for significant periods of time. Constantly running at full speed and full flow leads to pressure overshoots and relief valves cracking open. And proportional or other valves used to control speed in the system generate throttling losses.
As a result, industrial machinery with fixed-speed hydraulic pumps wastes between 20% and 80% of the average power consumed, he said. That’s traditional hydraulics.
Reducing motor speed when the system doesn’t need full flow would reduce energy consumption and heat generation. While some system losses are unavoidable — for instance, decelerating a large mass moving at high speed requires a throttle valve or pressure-relief valve, which generates heat — in many cases engineers can improve the efficiency of the system greatly, by design.
Servo-pumps
At the other end of the spectrum are high-efficiency circuits — called energy-on-demand systems — which involve variable-speed pump drives. Here, a closed loop, servomotor-driven pump powers a cylinder directly, essentially rotating in one direction to extend the cylinder and in the opposite to retract. No throttling valves are necessary.
The cylinder is controlled thanks to the capabilities built into the servo drive. Rexroth’s system, called Sytronix SvP — servo variable pump — has hydraulic intelligence built into the drive that lets users simply send a profile for position, velocity and force to the drive, which converts that information into commands needed by the servomotor to control the cylinder.
A system like this greatly reduces heating and losses because the motor and pump only rotate when needed. When no cylinder motion is required, there’s no motor motion, either. There are no throttling losses, a sizeable speed reduction on typical machine cycles, and the motors and pumps run substantially cooler because they don’t operate at full speed all the time, said Gigliotti. There are small converter losses, but the overall energy savings are somewhere between 40 to 80% compared with a traditional system.
A good example of this is seen in the plastic injection molding industry. Decades ago virtually all machines were hydraulic powered, typically involving fixed-displacement pumps and fixed-speed electric motors running at 100% speed and flow all the time. In the 1990s that industry embraced variable-displacement type pumps, either simple pressure-compensated or advanced closed-loop electronically controlled displacement type pumps, which offered a significant savings in energy consumption. But around 2012-2013 electro-mechanical injection molding machines — with no hydraulics — became popular, as they were deemed to be much more efficient and quieter. Hydraulics had to evolve to compete, as even designs with variable-displacement pumps didn’t compare well from an efficiency standpoint.
The answer was to merge servomotor and pump technology and develop hydraulic “intelligence” so servo drives could rotate a pump in both directions, with no throttling valves or relief valves necessary for pressure control. That technology is much more affordable than electromechanical, but virtually just as efficient, reducing energy consumption of injection molding machines by about 80% versus original fixed-speed designs.
Add-on benefits included reducing operating temperatures and virtually eliminating bulky and costly cooling systems. Today, auxiliary cooling systems are only needed to maintain a constant fluid temperature. This innovation transformed the entire industry within the space of two or three years, so that most every new machine built was using some form of servomotor-driven pump technology.
Other side benefits include noise reduction and longer life as the components spin at a much lower average velocity during the machine cycle. A system involving servomotors costs more to build, but due to the energy savings, return on investment over traditional hydraulics in plastic injection molding machines is typically about one year, said Gigliotti.
Smart asynchronous
Another example of saving energy via a sophisticated drive system doesn’t involve servomotors. Hundreds of thousands of hydraulic systems around the world still use asynchronous motors and variable-displacement pumps. These pumps vary the swashplate angle and, therefore, pump displacement, based on a fixed motor speed. When the system reaches the set point for pressure, the swashplate destrokes and pump displacement decreases while holding pressure, as the motor continues to spin at say 1,800 rpm — even with little flow demand from the system. That’s inefficient, said Gigliotti.
To address this, Bosch Rexroth developed a drive package, called the Sytronix DRn, that has the software and hydraulic “smarts” to drive a standard asynchronous motor and control speed based on algorithms managing the variable-displacement pump operating state. The drive knows the type and size of the attached pump, system pressure based on transducer signals, and motor torque based on the current and voltage it is supplying to the motor.
The system is programmed to target the ideal swashplate angle, depending on operating conditions, and it will slow the motor when there is little flow demand. The DRn has been shown in waterjet-cutting machines, as one example, to reduce energy consumption by 50%.
Thus, adding intelligent speed control for the motor can significantly reduce energy consumption in a system. This type of technology is applicable to almost all hydraulic systems already in use and does not require a major redesign.
Bosch Rexroth
www.boschrexroth.com
Filed Under: News, Pumps & Motors, servohydraulics