By Josh Cosford, Contributing Editor
We use metric fittings to connect and seal hydraulic valves, pumps or actuators to their respective plumbing in a metric-based circuit. They prevent leaks in hydraulic systems by providing a leak-free seal at the component’s fluid port.
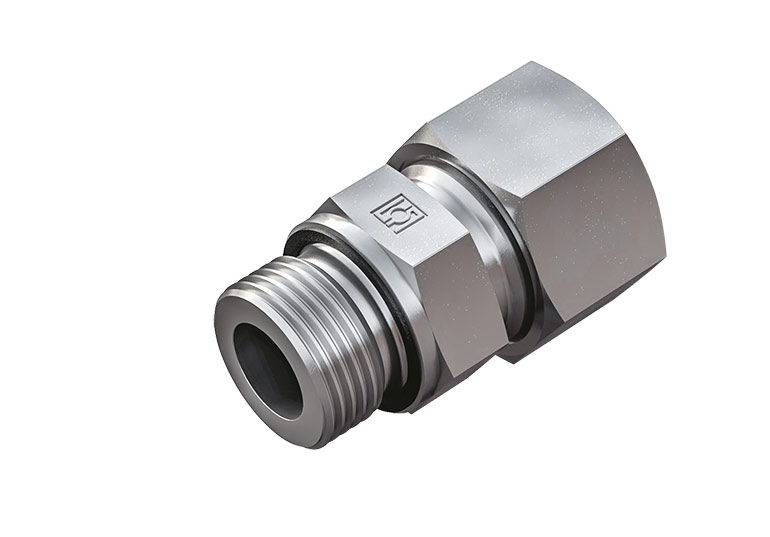
There are several types of metric fittings, including compression fittings, flare fittings, bite-type fittings, and hose fittings. Each fitting type provides fitment to a specific type of connection and is made from different materials, such as mild steel, stainless steel, or plated steel. In addition, most metric fittings employ a polymer seal, such as Buna Nitrile, which helps achieve a leak-free connection.
Metric fittings work by providing a tight seal between hydraulic components. The fitting is inserted into the respective fluid port and tightened to encapsulate the seal, which resides under the thread shoulder just above the threads. In addition, most metric fittings use a seal bonded to a metal washer, which is resistant to extrusion and prevents fluid from leaking out between the clearance between the fitting and port.
The benefits of using metric fittings include increased reliability, improved performance, and reduced maintenance costs. Metric fittings are specifically designed to provide a tight seal despite frequent disassembly, reducing the risk of leaks and improving the overall performance of the hydraulic system. This can result in lower maintenance costs over time, especially since its seal is easily replaced should it degrade over time.
How do I choose the correct metric fitting for my hydraulic system?
When selecting a metric fitting for your hydraulic system, consider several factors, including the system’s pressure rating, the fluid used, the ambient and operating temperature range, and the specific type of connection required. It is essential to consult the equipment manufacturer’s recommendations or seek advice from a qualified hydraulic technician to ensure the correct fitting is chosen if you’re not already familiar.
While using different types of fittings in the same hydraulic system is generally not recommended, it is possible to use metric fittings with other types of fittings if they are compatible, such as with adapters. However, care must be taken to ensure that the fittings were correctly chosen since more than one metric fitting standard exists.
Metric fittings can be made from a variety of materials, including steel, stainless steel, brass, and aluminum, although the latter two are not suitable for high-pressure hydraulics. The material used to make the fitting will depend on the specific application and the environment in which the hydraulic system is used.
Filed Under: Components Oil Coolers, Couplings & Fittings, Engineering Basics, Hose Assembly Tips