Distributed automation options have been improving for many years. Networked electro-pneumatic solenoid banks give machine builders smart and convenient choices.
Kevin Kakascik, Technical Marketing Engineer, AutomationDirect
Most automated machines and systems incorporate some number of enclosures and panels for housing controls components. However, these centralized devices typically must interconnect with many more field sensors and other equipment which could be some distance away. Many years ago, hardware designers knew it made good sense to push some of the control elements out of main control panels and closer to the field devices they connect to, minimizing field wiring and installation costs.
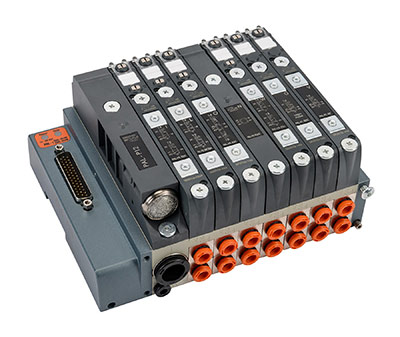
This concept of distributed control for industrial automation has been around for some time, developing just a while after the programmable logic controller (PLC) was invented. Available distributed control options have expanded greatly over the years, with many new device types and other capabilities, such as advanced networking and fieldbus protocols.
One example is intelligent electro-pneumatic solenoid manifolds, which can be distributed throughout a machine or system, and networked to a controller. But before we examine these solutions, let’s take a look at how we arrived at these advances.
Going the distance
Distributed control started as input/output (I/O) blocks located remotely from the controller, allowing automation to reach relatively distant areas that might only need a small number of I/O. Each location where an I/O block was located was sometimes called a drop. These first I/O blocks came in a few fixed sizes, point counts, and signal types (discrete or analog), giving engineers and designers some flexibility as systems and I/O counts grew larger and more dispersed.
One initial problem was a lack of modularity and a one-size-fits-all mentality. It was great to reach remote areas using a single communications cable, instead of needing an electrician to install multiple wires and cables to something 400 feet away. However, if only a few I/O points were needed, or if the point count did not conveniently match available modules, then there would be excessive spare points, which made remote I/O less economical. So sometimes remote I/O was a little wasteful, but this was what was available at the time.
Another problem with these older I/O blocks was the simple serial networks they supported. Modbus RTU was common with many vendors, but quite a few used proprietary serial networks. Serial networks of any type could be very reliable, but also experienced or required:
- Noise and grounding issues, which slowed or disrupted communications.
- Specific topology layouts and termination requirements.
- Low limitations on the number of nodes.
- Architectures which could constrain convenient future expansion.
- Non-compliant installations that could run for many years, then unexpectedly fail.
Modularity modernization
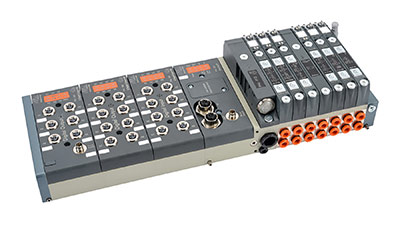
PLCs and automation distributed control went through some growth and evolution as manufacturers saw the need for modularity. PLCs were already becoming more modular — with remote racks, CPU cards, and separate communication adapter cards — providing more flexibility to mix-and-match configurations.
Soon manufacturers developed products specifically designed for distributed field I/O, and then smarter and more modern networks and protocols to support these devices. CANbus for DeviceNet was one example, but today the most popular choice is Ethernet media for distributed I/O, with protocols such as Modbus TCP and EtherNet/IP.
Eventually, field I/O systems became more compact and affordable, reinforcing the benefit of installing remote I/O devices closer to field equipment. Today, these distributed I/O systems are scalable, affordable, and supported by many different industrial communications networks and vendors. Small, low-density I/O modules — often known as point I/O or slice I/O — are ideal for locations like a start/stop pushbutton station with just a few I/O points. Other high-density options might use a larger rack configuration and handle large amounts of I/O.
Another advancement was improved environmental ratings, which enabled I/O components to be installed outside of control panels as direct machine-mounted devices, even in washdown environments. This can save even more design and installation costs, while making it easier to maintain equipment.
Enlightened electro-pneumatics
One need not spend much time around industrial machinery or automation to learn that pneumatics go hand in hand with control systems. Pneumatics are one of the most common ways to perform physical actions and movements with automated equipment. Whether it is performing a press action, lifting, indexing, or diverting with a pneumatic cylinder or airbag — pneumatics are everywhere on automated equipment.
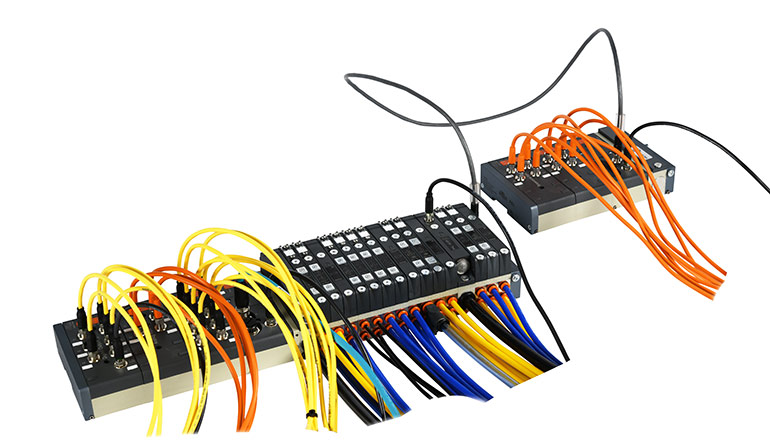
Standard solenoids are individual devices, each requiring air tubing connections and wiring. Many solenoids could be grouped into a single manifold, called a modular pneumatic valve bank, to simplify the air supply tubing somewhat, but each still needed hardwiring (Figure 1).
Therefore, just as with I/O, there was a growing need for better ways to install distributed pneumatic solenoid valves, especially for small to medium quantities of actuators in more remote areas. As with I/O, the best case would be a system needing just one network connection.
Of course, pneumatic modularity remains important, both for the number of solenoids at a drop and the ability to choose among 3-, 4-, and 5-way, and 2- or 3-position configurations. The system also needs to accept one or more air supplies for each drop, and each solenoid must offer a high enough Cv rating to support the flow needed to operate the equipment.
The solution is known as a modular electro-pneumatic valve bank, which allows multiple individual valve modules to be installed in one manifold assembly. This assembly will typically need only one air input, although additional inputs may be optional if other pressures and flows are needed. All of the electrical wiring is concentrated at this location, simplifying installation, reducing wiring errors, and making the system much easier to troubleshoot.
Distributing multiple valve manifolds around a machine can also simplify tubing runs and shorten airlines to cylinders and actuators, resulting in simpler integration and faster actuator response. Some manifolds are available with environmental rating options so they can be installed away from electrical panel hazards and right on machines, even in washdown environments.
Not only do these modular valve manifolds work with popular Ethernet industrial protocols, but some provide the option to add I/O modules in conjunction with pneumatic modules. Pneumatics and instrumentation exist together on machines, so the ability to group solenoids and I/O in one drop is a great benefit. A single assembly combines various solenoid valve types, digital and/or analog I/O, and common power sources for all of the above. Many different configurations can be created using a limited variety of basic components, with the I/O providing local control and monitoring.
Flexible fit
Electro-pneumatic systems are very versatile as they can be used for just field I/O or pneumatic solenoids, or a combination in one unit (Figure 2). This comes in handy for OEM machine builders and system integrators, who can standardize on designs, vendors, protocols, parts ordering, and products to meet all their automation needs.
The field I/O side of electro-pneumatic systems are comparable to other remote I/O systems in terms of scalability, footprint, and cost. The same can be said for the solenoid valve side of these systems when compared to hardwired modular pneumatic valve banks. Valves are compact, yet they have high flow ratings (Cv) and good performance.
Environmental ratings for modular electro-pneumatic systems also align with the other types of individual devices. Some require installation in an enclosure, while others can be machine mounted, with suitable environmental ratings.
Electro-mechanical systems can usually be split into separate physical subsystems while still using only one network connection. Designers can take advantage of this modularity feature for best operational performance and installation simplicity. This especially makes sense where systems are organized into zones or cells, and each section should have localized automation components. These production lines can be shop-assembled and tested as a whole, and then broken down into convenient sections for shipping and field installation. Only minimal network and pneumatic connections are required in the field when this approach is used (Figure 3).
Some installations — such as packaging lines and the associated box forming, conveying, filling, labelling, and palletizing equipment — are organized through a spread-out area with relatively low I/O densities and pneumatics needs. These applications are ideal candidates for applying electro-pneumatics precisely where they are needed.
Electro-pneumatic manifolds deliver choices
Electro-pneumatic systems are a versatile solution for providing I/O connections and pneumatic solenoid valves in a modular form factor at remote locations. This gives designers far more options for building effective automation systems. Intelligent manifolds also save space and reduce the need for control enclosures, while minimizing the effort and cost of wiring and plumbing.
Electro-pneumatic systems are easier to maintain, and they deliver more information to and from supervisory automation systems for better control and diagnostics. Installations using this approach are very neat and clean, with future expansions easy to implement. For these and other reasons, designers should work with suppliers of electro-pneumatic manifolds to see how they can improve their machine automation systems.
AutomationDirect | automationdirect.com
Filed Under: Pneumatic Tips, Valves & Manifolds