Today’s hydraulic fluids are forced to operate in hotter environments. But the right formulation can help reliably moderate temperatures, creating significant operational benefits for end users.
By Blayne McKenzie, Technology Development Manager, Industrial Products, The Lubrizol Corp.
Mobile and stationary hydraulic systems have gone through major changes in recent years. Widespread efforts toward higher efficiency and cost savings have spurred dramatic technological evolutions, and such developments have implications in every area of modern machinery.
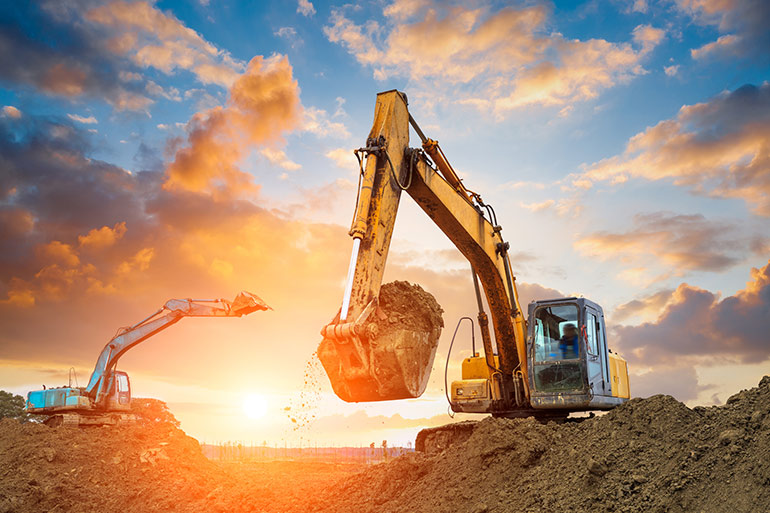
Hydraulic fluids are one of those areas. Several increasingly common design choices have created increasingly severe operating conditions. Today’s fluids must contend with hotter temperatures and must provide high levels of performance in smaller volumes.
Traditional formulations may not be up to such tasks without contributing to costly downtime and abbreviated equipment life spans. Thoughtful fluid selection — taking into account new chemistries and polymers that provide high levels of performance — can in fact reduce total cost of ownership for hydraulic equipment owners and operators. This article will explore why that is and what hydraulics professionals should consider into the future.
How new designs impact fluids
Hydraulic machinery OEMs have two driving imperatives when designing new equipment: cost control and higher efficiency. Often, those imperatives intersect in ways that can create new challenges for hydraulic fluids.
For example: Many new hydraulic machines are smaller and lighter than they have ever been. Certain components are downsized to reduce the total cost of materials required to manufacture the machine. Meanwhile, a smaller, lighter machine that can do the same work as a bigger, heavier machine is fundamentally more efficient, requiring less fuel to perform the same function.
One component that has been a primary target of downsizing is the hydraulic fluid sump. And while this has been an effective weight-reducing strategy — oil sumps are traditionally a large and heavy component on such equipment — it also means that a smaller volume of hydraulic fluid is used in the machine. Less fluid being asked to provide the expected functionality creates more severe operating conditions. Fluids become hotter, and because there is less time for those fluids to cool between circulation routes throughout the machine, they stay hotter for longer periods of time.
This excessive heat can cause several issues for the hydraulic fluid, which not only protects equipment but provides the machine’s essential functionality. Some of the impacts include:
- Viscosity loss. The hotter conventional hydraulic fluids become, the greater their potential to lose viscosity. And as protective film layers become thinner and thinner due to this phenomenon, the fluid’s protective capabilities can become compromised.
- Premature oxidation. Sustained hotter temperatures can also cause the fluids to oxidize more quickly. This further reduces their protective and performance capabilities, which has the potential to damage parts.
And beyond the impact on the fluid’s capabilities, higher levels of heat in any part of a piece of hydraulic equipment will essentially cause the equipment to age more quickly. Given these circumstances, a hydraulic fluid’s ability to mitigate heat increases inherent to new designs can be of major benefit to operators of modern hydraulic equipment.
Weighing the capabilities of performance polymers
A reliable method for overcoming the challenges associated with more severe operational conditions is to select a hydraulic fluid formulation that includes performance polymer technology. Performance polymers can enhance a wide range of performance attributes in many different fluids and oils that help modern equipment reach its full potential.
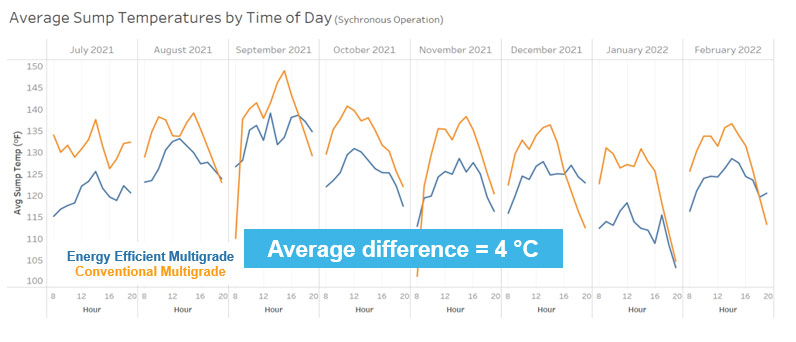
For example, Lubrizol has recently identified and thoroughly tested an energy-efficient ethylene-propylene copolymer (OCP), which has demonstrated significant improvements in viscosity retention and shear stability while helping to reduce operating temperatures. Our teams compared an ISO 46 formulation including OCP against a standard multigrade fluid containing polyalkyl methacrylate (PMA) additive and a conventional ISO 46 monograde baseline. Testing was performed in benchtop viscosity and tribology equipment, total hydraulic system test rigs, and in real-world mobile and stationary hydraulic equipment.
Our results were significant. In laboratory pump testing that evaluated the OCP fluid against the PMA fluid, thermal imagery cameras captured a difference in surface temperature of ~3 °C, suggesting significantly cooler operation within the pump using the OCP fluid. In a full-scale mobile hydraulic field trial, similar results were recorded. Hydraulic sump temperatures were reduced by an average of 4 °C over eight months of operation when using the OCP fluid, with even greater reductions in peak temperature spikes observed. The molecular structure of the performance polymer in the energy-efficient hydraulic fluid generates less heat-inducing fluid friction, or traction, throughout the hydraulic system resulting in cooler operation and, ultimately, longer fluid and equipment lifetimes.
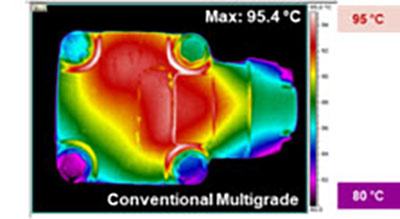
This reduction in friction also allows the machine to perform its intended tasks more efficiently. In controlled experiments on-site and in climate-controlled laboratory settings, our teams evaluated many different modes of off-highway hydraulic equipment. Compared to a conventional ISO 46 monograde, formulations including OCP demonstrated efficiency gains ranging from 1.4%-8.5% in a variety of applications, including laden lifts, front unladen lifts, backhoe loaders, wheel loaders, injection molding equipment, and more.
Operational benefits for end users
The ability of a high-performance hydraulic fluid to significantly decrease operating temperatures throughout the sump and hydraulic lines in critical equipment can translate to significant operational and maintenance benefits for end users.
More moderate temperatures over a sustained period of operation help mitigate the concerns around heat-related viscosity loss and premature oxidation as outlined earlier in this article. With these problems taken care of, a high-performance fluid will maintain its protective and performance properties over longer periods of time, helping to protect the equipment.
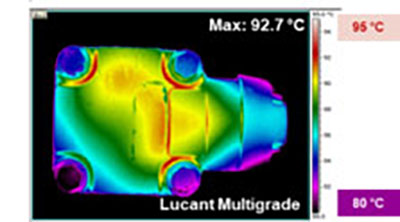
This durability and temperature reduction performance contribute to an extended oil drain interval, meaning that required fluid changeouts can be extended, thereby reducing the Operator’s Total Cost of Ownership. For end users, the potential here is significant. Fluid changeouts are one of the most time-consuming parts of regularly scheduled maintenance for many forms of hydraulic equipment, which in some instances requires flushing lines that may extend throughout the entire piece of equipment.
Consider a mobile excavator: Old fluid must be evacuated from lines that extend from the cab throughout the arm and the boom, and doing so can be a labor intensive process. And taking any equipment out of service for any period of time in critical environments — commercial mining equipment, for example — can result in massive losses in productivity and profitability. In contrast, a higher-performing hydraulic fluid can help such equipment remain productive in the field for a significantly longer period of time on an annual basis.
Meanwhile, the energy efficiency gains provided by a higher-performing fluid can help any operation improve its productivity, profitability, and sustainability. Annually, our estimates suggest that such a formulation can help equipment move hundreds of thousands more tons; save tens of thousands of dollars on fuel and utility costs; and eliminate hundreds of tons of carbon dioxide generation. These can all be major bottom-line impacts for any organization.
Modern hydraulic equipment has driven the need for higher-performing fluids, and it’s only reasonable to expect that such machinery will continue to evolve in the coming years. High-performing fluids that have been formulated with the right chemistry can help new equipment meet its full potential over the course of its lifetime. And by reducing the need for excessive, labor-intensive maintenance, these fluids have major potential to help operators significantly reduce their total cost of ownership. Work with your fluids supplier to identify and adopt such formulations — it can have a major impact.
Lubrizol
lubrizol.com
Filed Under: Components Oil Coolers, Engineering Basics, Fluid Conditioning, Fluids, Sealing & Contamination Control Tips