By Josh Cosford, Contributing Editor
Hydraulic hose failures are much like vehicle collisions — they’re not accidents. No longer can you blame weather, road conditions or distractions because it’s always someone’s fault. Unless a meteorite slams into your windshield, causing you to blow through a red light, there is always a cause of collisions. The same holds for hydraulic hose failures. Anything from poor design to improper maintenance will have resulted in your hose failure, but you can avoid unforeseen downtime by heeding these tips.
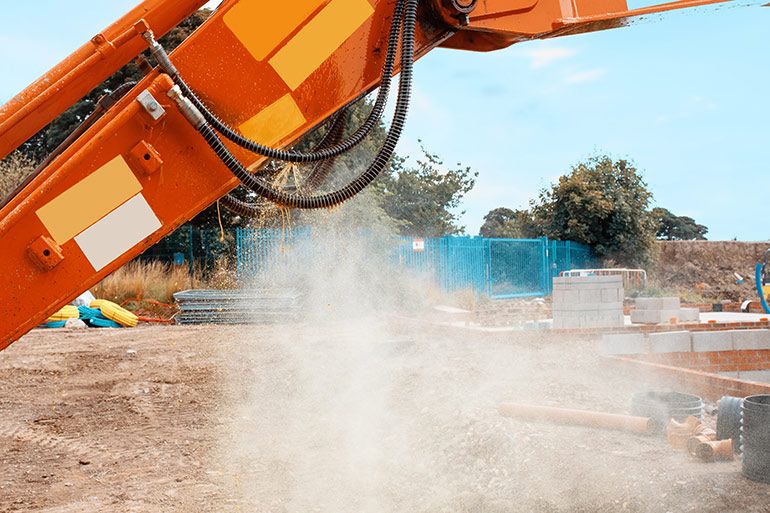
- No consideration was paid to material choice. This consideration includes the inner tube and carcass, which both have exposure potential to chemicals or fluids capable of breaking down the hose’s synthetic rubber material. Hydraulic oil contaminated with water also increases oxidation and breakdown of the tube. Conversely, ambient and caustic chemicals may break down the cover, including industrial fallout that settles upon the hose surface.
- Poor routing decisions. A hose resting perpendicular to the fitting end creates stress at the crimp. Because the hose is subjected to a bending moment, any cycles that cause the hose to move or vibrate will stress this joint. You must route the hose to prevent pinching or bending at the fitting, so using hose clamps and intelligent routing will prevent blowouts at the hose’s crimp joint.
- Abrasion from vibration. This category is prevented partially from # 2, but even well-routed systems are subject to modifications over the machine’s service life. For example, sometimes, the tube from a hard-piped system is replaced by a hose and never fixed in place to prevent vibration and rubbing. The abrasion could even take place inside a loose clamp or a carrier. If abrasion (or excuses) is unavoidable, abrasion-resistant sleeves may be wrapped around the hose to prevent damage.
- High temperature. Even if one through four are heeded, excessive temperature accelerates hose failure because the tube and cover can no longer maintain the rubber’s firm yet flexible nature. As a result, the tube can start to extrude through the reinforcement, and the cover is more prone to abrasion, oxidation and peeling.
- Poor assembly practice. In most cases, an improperly assembled hose will fail quickly. The most common mistakes in hose assembly are under-crimping, over-crimping and low crimp engagement. An under-crimped hose will not effectively hold the hose end onto the cover and could easily pop off under pressure. An over-crimped hose could bite through the reinforcement layer, possibly shearing the wire with a subsequent blowout. Finally, by insufficiently inserting the hose into the fitting, a poor “bite” allows the hose to pop out more easily under pressure.
Each of the above examples is a failure due to human error or incompetence. Hose failures will be avoided if proper training begets experience because I’ve never seen a meteorite take down a hydraulic system.
Filed Under: Components Oil Coolers, Engineering Basics, Hose & Tubing, Hose Assembly Tips