By Josh Cosford, Contributing Editor
Hydraulic hose enjoys the title of go-to fluid conveyance of choice for many hydraulic machines. Although steel tube is also popular and provides a tidy, permanent solution to plumbing, it is less easily serviced and replaced. Hydraulic hose, when properly manufactured, routed and installed, offers a tidy and permanent solution to plumbing.
Besides using an appropriately selected hose based on your application’s fluid, temperature, pressure and ambient conditions, the way you route your hydraulic hose plays a huge reliability role. Avoiding bending, vibration, and abrasion provides the end user with a reliable and safe machine.
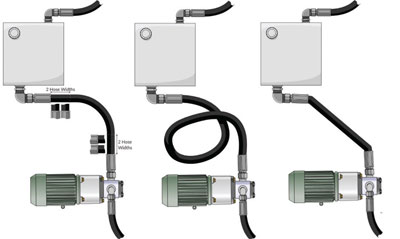
Hydraulic hose clamps fix the hose to a given machine surface to prevent movement and subsequent abrasion while helping dampen vibration. These clamps are mandatory to protect a hose from premature failure, but the location of such clamps must not offend the practical routing considerations for plumbing hydraulic hoses.
The hydraulic hose must provide only the length required to plumb between two port connections without excess slack or narrower than the minimum bend radius. A hydraulic hose manufactured too long for an application costs the manufacturer more in material but also increases the chance of slack hose rubbing against machine surfaces or another hose.
Hose manufactured too short for the application results in early failure more often than excess hose length. Hose routed between two ports creating a semicircle with the hose must avoid bend radii too tight for the construction type of the hose. When a hose’s bend radius is too tight, pressure exerts upon the joint at the hose end, which stresses the steel wire reinforcement. The hose will eventually fatigue and rupture at these joints, so be sure to respect the minimum bend radius of the hose, which you can reference in the manufacturer’s literature.
Even straight hoses too short for the application will fatigue and eventually fail. Hot and cold cycles expand and contract the hose, so when no spare room exists to allow this slight movement, the hose may fail early or even catastrophically if a hose rips from its hose end. Provide a small amount of slack in a straight hose to ensure a reliable assembly and ease installations where the technician has to stretch the hose to install.
A hose that moves between oscillating planes must take advantage of geometry to avoid hose-damaging torque. Instead of mounting a hose horizontally to allow torque, the hose should be routed upwards like a rainbow. As one plan moves higher or lower, most are easily accommodated, like a slinky between your two hands. Should a horizontal installation be unavoidable, run excess hose length and secure the middle against a stationary bracket using a hose clamp. This routing allows one end to torque slightly while the other remains fixed.
Care must be provided to cylinders with hoses connected at 90 degrees to the work port. Rather than allow a hose to connect horizontally to a vertically mounted cylinder, the hose should be allowed to hang relaxed and parallel to the cylinder. Using 90-degree port adapters or hose ends on the perpendicular port of the cylinder prevents the hose from bending and chaffing at the hose end joint.
Any cylinder with tricky installation requirements may use additional hardware to ease the stress on the hose end connection. A swivel joint, for example, allows the hose to twist, preventing any torque damage to a hose fixed between otherwise moving points. When adhering to intelligent hose routing guidelines, there is no reason a hydraulic hose cannot last as long as a hydraulic tube.
Filed Under: Engineering Basics, Hose & Tubing, Hose Assembly Tips