By Josh Cosford, Contributing Editor
A hydraulic pump is literally the heartbeat of your hydraulic system. If you’re new to hydraulics, you’d be surprised at how many ways you can push fluid under pressure. The rotating and/or reciprocating of gears, vanes or pistons offer a designer constrained by any performance or budget envelope the options to best suit any application, especially since each of the primary pump construction styles offers unique options within each series.
Piston pump technology exclusively employs axially or radially reciprocating pistons relative to the input shaft. Fixed and variable displacement pumps are offered in all three primary construction variations — axial swashplate, bent-axis and radial. For both axial and bent-axis piston pumps, you will notice their pistons reciprocate in parallel as the rotating group orbits the shaft. Radial piston pumps look more like old wartime engines from aircraft, with their pistons reciprocating perpendicular to the input shaft. Although the most complicated design, piston pumps enjoy power and efficiency not possible in gear or vane pumps.
Axial-piston styles
The fixed-displacement piston pump offers designers a relatively inexpensive entry point to the piston pump. They provide reliable, high-pressure fixed flow for open-circuit hydraulic systems with no fancy controls. However, the control options available to piston pumps offer many clever tactics to control your hydraulic system, from pressure compensation to electrohydraulic proportional control with onboard pressure transducers.
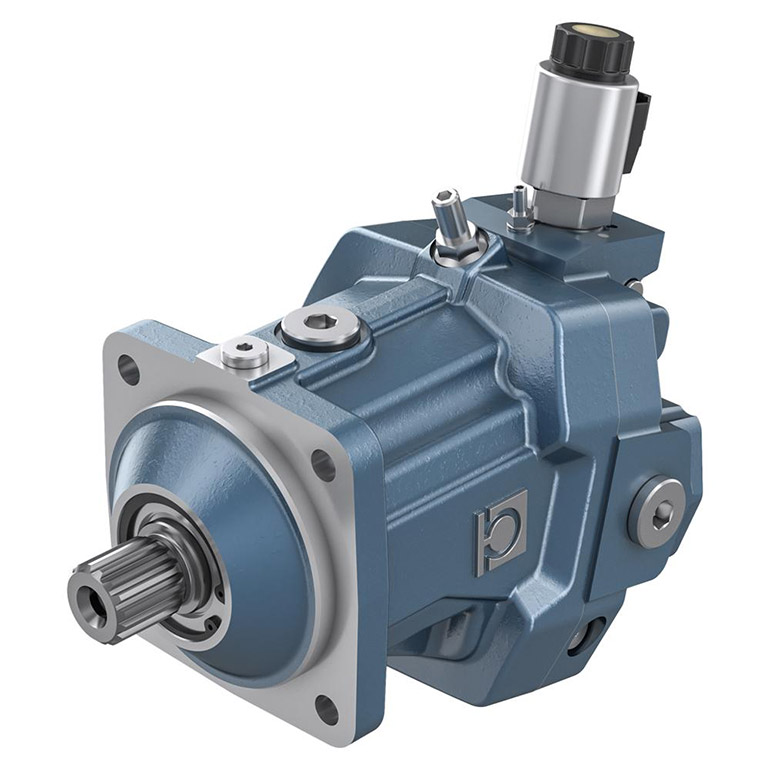
Image Bondioli & Pavesi
A pressure compensator is a relief valve for the control piston of the variable-displacement pump. The compensator is a very low flow component that essentially controls the swashplate angle to modify displacement in such a way as to maintain a set pressure. Any downstream flow demand lowers pressure drop at the pump, causing the pump to increase flow to maintain pressure. So long as downstream flow demand does not exceed the pump’s maximum flow rate, the pump can compensate and remain at full pressure. However, any flow exceeding its maximum rating will be subject to the downstream actuators’ load pressure.
Manufacturers offer various forms of displacement and pressure control. For example, load sensing control allows the pump to read downstream load pressure signals to reduce flow during off-demand periods and at reduced pressure equal to a few hundred psi higher than the highest load. A step further, you’ll find horsepower limiting (sometimes called torque or power limiting), which provides the machine maximum flow and pressure so long as the total demand is less than the prime mover’s capacity. Should a machine, such as an excavator, demand higher flow and pressure than the engine can supply, such as when multiple high-pressure actuators are simultaneously activated, the pump will automatically restrict flow to reduce the total power required.
Regardless of compensator type, each variation achieves its result by varying only the swashplate angle. For axial piston pumps, the swashplate pivots to increase or decrease displacement as required by the compensator as directed by the control piston. As a result, the control piston moves in the same axial plane as the rotating shaft, serving up a compact and powerful package.
Bent-axis piston technology
Although axial piston pumps are easily the most popular, other piston pump designs are offered with variable displacement. You may be aware of the bent-axis piston motor (Figure 1), which is famous for its high power and high-speed reputation. Its shaft and bearing assembly rotate at a taper relative to an axial piston motor. Despite their high-pressure design, the bent-axis configuration offers 25% higher rotational speed than straight-axis motors, and their bearing design is better suited to pulley or gear-driven applications. The force vector from a gear or pulley must oppose the bent direction of the motor (Figure 2), much like your arm pulling against a surgical band from underfoot to do bicep curls.
The tapered, oversized roller bearings inside a bent-axis piston motor provide superior side load protection to resist the steeply angled rotating group side load. For example, a swashplate on an axial piston motor may allow a maximum of 15-22° angle, while the bent axis piston motor operates at 40° or more. This extreme angle allows the motor to achieve high displacement in a small package, resulting in a high radial load on the input shaft. Resisting these side loads requires the heavy-duty tapered bearings like those you see in Figure 3 and explains the necessity to pull from the opposing direction as the motor angle.
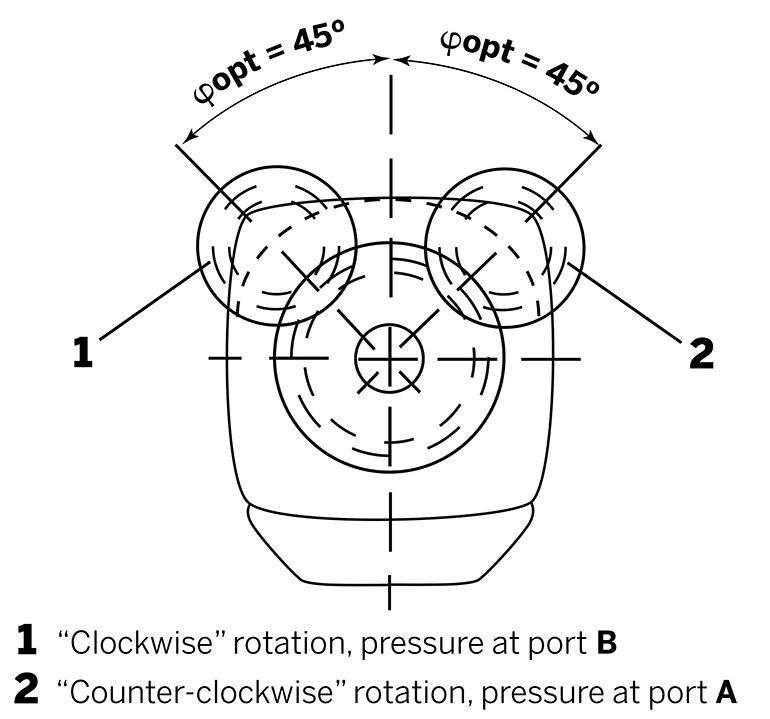
The same benefits of the bent-axis piston motor apply to its pump kin. Superior power density, high-speed operation and high resistance to radial load make these the top choice for mobile hydraulic designs driven directly by diesel or gas engines. In addition, their inherently robust design makes them the top choice for gear or pulley-driven pump applications (as long as the installation recommendations are adhered to). Although the tapered roller bearings provide high side-load resistance, because the bearings are loaded to remove excessive clearances, excessive wear may occur. As a result, you’re more likely to replace the bearings on a bent-axis piston pump than in other designs.
You may be surprised to know that variable-displacement bent-axis piston motors are offered by manufacturers. Unfortunately, their appearance doesn’t seem to offer any place to mount any useful swashplate angling device. Their construction varies significantly from a swashplate variable-displacement pump, where instead of varying swashplate angle, the entire lens plate slides up and down inside the port plate.
A stroke piston opposed by a bias spring and control piston works much the same as in an axial piston pump. The compensator receives a pilot signal from the pressure port to balance the pressure drop at the pump’s outlet, varying the angle of the rotating group as required to maintain pressure.
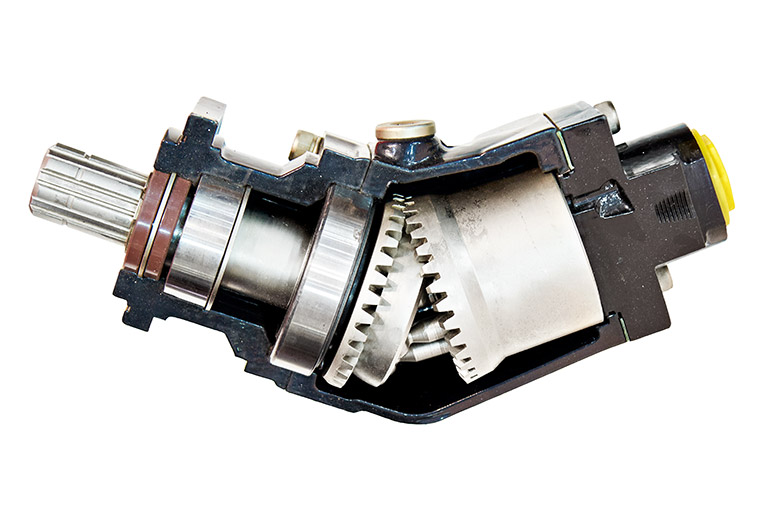
The leading manufacturers of piston pumps offer most, if not all, control options for their bent-axis piston pumps. Basic pressure compensation with no other function often goes by pressure cut-off in product literature (or pressure override). The basic pressure cut-off control simply observes outlet pressure and adjusts the swashplate angle to alter flow rate, thereby maintaining a set pressure drop. So long as system demand is less than maximum flow, the outlet pressure remains at compensator set pressure. However, should demand rise above maximum pump flow, your circuit is at the mercy of the path of least resistance.
To be honest, selecting a pressure-compensated bent-axis piston pump for anything other than high-speed belt or pulley driven applications is an expensive bit of overkill. The control devices of variable-displacement bent-axis piston pumps are often quite advanced; you can expect various advanced controls such as horsepower limiting, hydraulic proportional control or even electro proportional control. I’m aware of one particular manufacturer that offers no less than seven kinds of horsepower-limiting controllers for one pump!
Proportional pump control uses proportional pressure-reducing valves in place of standard pressure compensators. For example, imagine a bent-axis piston pump where the spring offset stroke piston fights against spring pressure by infinitely varying the pressure inside the control side of the piston. Precise pressure observed by downstream transducers offers a closed-circuit feedback loop for the machine controller to adjust the proportional valve setting to match the desired outlet pressure. Some pumps may even take it a step further to include a linear transducer to provide precise displacement feedback, guaranteeing your circuit precise output flow and pressure despite fluctuations from the load, temperature, or viscosity.
With so many pump options on the market, do we really need so many advanced options for a single pump style? My vote is yes because the bent-axis piston pump offers unique advantages over other designs. The variety of control options available ensures that your system, no matter how complex, has the pump design you need.
Filed Under: Components Oil Coolers, Engineering Basics, Mobile Hydraulic Tips, Pumps & Motors