Hydraulic motors and pumps are used in outdoor environments that are often dusty and dirty. These environments can be damaging to shaft seals simply because grit will work its way in between the shaft and sealing area. Once started, this begins to abrade the elastomer, altering the shaft surface finish in the sealing area. Seal failure will eventually occur. Replacing the seal requires removing the pump motor, disassembling and repairing it. This results in significant system downtime increasing operating expense.
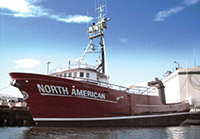
The workboat pictured uses an Overhung Load Adaptor for transmitting engine power to hydraulic pumps.
Seals are often identified as the Achilles heel of a hydraulic system. They are critical because they seal in the necessary case flow that is used to lubricate the internal components and carry heat away from the pump or motor. Often taken for granted, these seals need protection from undue stress and wear because they can make the difference between smooth functioning, trouble-free operation and failure.
When seals are subjected to small amounts of wear, they may begin to slowly weep. This can be subtle and not easy to detect. When weeping begins, it may be tiny and undetectable. Yet, even a small leak tends to attract dirt and can lead to more wear. Once significant wear occurs, the pump or motor seal will need replacement. Replacing damaged shaft seals is laborious and costly because multiple hydraulic components must be disconnected to get at the seal failure. Once the seal is replaced, multiple components in the system have to be reconnected before the system can be restarted.
The time to protect from seal damage is early in the system design stage, before problems occur. The best option is to include an intermediate connection and component stabilizer between the motor and the pump in the hydraulic system. This intermediate connection provides an extra layer of protection to the shaft seals and is called an Overhung Load Adaptor (OHLA). This intermediate positioning device provides a rigid platform that absorbs both internal and external stresses. It ensures that the connected hydraulic components stay in alignment and that the integrity of the seals is maintained.
Commercial fishing vessels like the North American benefit with major energy savings from the Gen-Tech power generation system, which connects to the workboat’s main engine. The Gen-Tech system uses an OHLA for protecting the hydraulic connecting seals and increasing motor durability and life.
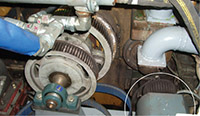
The Overhung Load Adaptor provides an intermediate, rock solid platform for protecting the hydraulic connecting seals and increasing motor durability and life.
The Gen-Tech system eliminates the need to run a separate auxiliary engine for generator operation when the main engine is in travel mode. When equipped with the OHLA, the two hydraulic pumps connected to the primary engine work effortlessly, providing generator power so auxiliary engine operation is unnecessary. A fuel cost savings of $2,300 or more in an 8-day fishing excursion is typical using this system.
In the Gen-Tech system, the OHLA supplies a solid, permanent mounting surface. It transmits rotary motion from the main engine to the hydraulic pumps. This also eliminates the need for a secondary gearbox to operate the hydraulic pumps, which can be more costly. The OHLA also adds more stability in the drive train, protects connecting seals and enhances motor operation. In high seas, violent shifting motion multiplies powertrain stress and contaminants in the air, so the OHLA’s stability role is even more important.
The OHLA (Model 1036S) is belt-driven off the main engine (Caterpillar Model 399-1125 hp) by a 2.8:1 speed ratio using a Gates polychain drive. With a SAE-D face mount, the OHLA has a 132-spline input, a 21⁄4-in. output shaft and a 7-in. pitch diameter on the OHLA’s pulley. For added durability, spherical bearings were selected for this application. Extra rugged to meet all operating conditions, the OHLA housing is made of 25,000-psi tensile cast iron with shafts of 130,000 psi stress-proof steel.
Zero-Max
www.zero-max.com
Filed Under: Fluid Power World Magazine Articles, Sealing