By Josh Cosford, Contributing Editor
Hydraulic hose bend radius, quite simply, describes how tightly circular a hydraulic hose can bend. More importantly, designers and technicians wish to know the minimum bend radius a hose handles while maintaining integrity. Although one might easily force a hose into a tight radius during installation, its design and construction play a role in how long a hose will last at any given tight bend.
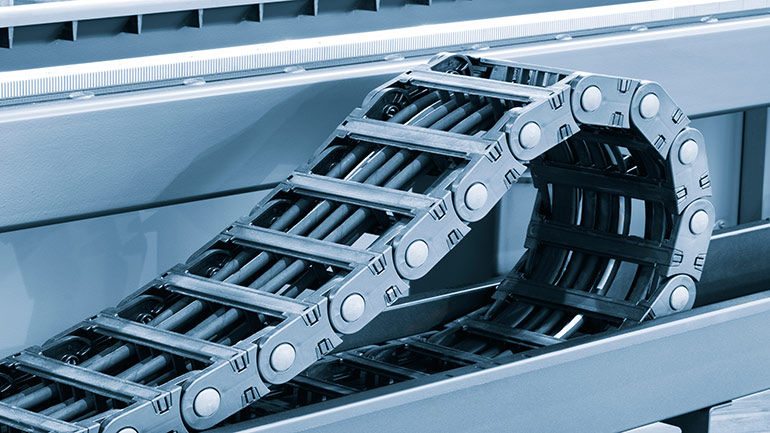
Hose flexibility plays a critical part in the design and implementation of machinery, especially those within tight space constraints or with actuators that pivot or glide. A hydraulic cylinder, for example, may pivot at its base and swing from obtuse through acute angles, requiring the hose to bend tightly as it moves. Additionally, common equipment such as for utilities or injection molding use hose carriers that contain assemblies within a protected channel while moving forward and back. During such an operation, the entirety of the hose bends 180 degrees as it cycles, and with a tight hose bend radius, the carrier can be more compact.
Even when there is no dynamic movement such as pivoting hose or those inside carriers, even a tight bend on a static hose can lead to trouble if you exceed the minimum bend radius. With any pre-stress on the hose because of an excessively taut installation, you have a higher likelihood of failure from pressure spikes, temperature extremes or general fatigue.
Factors that dictate bend radius are hose construction — especially the reinforcement layer — and hose diameter. The two primary construction configurations for hydraulic hose reinforcement are spiral wound steel and braided steel. The high-tensile wire used to help contain extreme hydraulic pressure has excellent bending capability by itself, but the way the wire is wound on the inner tube puts the wire in tension when bending occurs.
Spiral reinforcement wire tends to be less forgiving but provides superior high-pressure capability. Common 6-wire hose easily handles the highest-pressure systems, but the resulting design is extremely stiff. Conversely, the intertwined double-helix windings of the braided design allow diametrical expansion, while the wires can also slide across each other for superior flexibility.
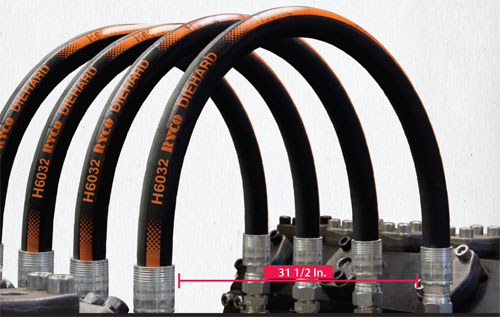
Until recent technological advancements birthed new braided designs, such as SAE 100R17, 100R18, etc., to achieve product-wide working pressure regardless of size, previous technologies, such as 100R1 and 100R2, were entirely dependent on diameter. Small diameter 100R1 hose could have a bend radius as low as 3 in., but as the diameter increased, you might be limited to a 25 in. radius or larger. However, even with 3,000 psi working pressure across all sizes, 100R17 operates down to a 1.5 in. bend radius or smaller while still perhaps twice as flexible as the diameter increases.
Too much wire tension can cause fatigue, resulting in the stretch or failure of one or more strands. The excess tension may occur from extreme pressure trying to bulge the hose or as the hose bends tighter than its minimum radius. The tension from extreme bending occurs on the outside surface of the hose, where it stretches to accommodate the bend. Also, repeated and continuous tight bending cycles will result in heat-induced stress on individual wires. Damaged or broken wires will compound the problem as neighboring wires bear the brunt of the extra load, themselves failing in sequence as each takes on increasing load.
Bend radius is not often an important consideration until it is. Many machine designs don’t have pivoting actuators and hoses fed through carriers. But any time you know your machine employs non-stationary or tightly-bent hoses, become aware of the minimum bend radius you require and select these hose assemblies that best suit your requirements.
Filed Under: Components Oil Coolers, Engineering Basics, Hose & Tubing, Hose Assembly Tips, Technologies