By Josh Cosford, Contributing Editor
The line that separates the performance of servo and proportional valves has blurred in recent years. Some may consider a servovalve to be any valve capable of accurately positioning your actuator with closed-loop control. However, in everyday hydraulic circles, many industry professionals describe a servovalve as a valve with a motor drive, where proportional valves use the traditional spool and core-tube armature setup.
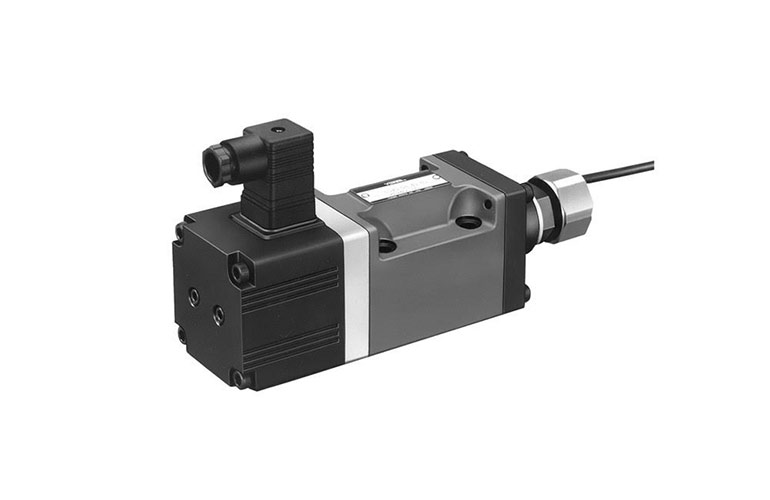
Older proportional valve designs employed a spool valve with metering notches and PWM-ready coils to infinitely vary the spool position. The performance level of these proportional valves left much to be desired but was the least expensive method to vary hydraulic flow and direction simultaneously. Having no way to control accuracy in the face of changes in pressure drop, the actual flow rate through a “dumb” prop valve will vary based on changes in flow, system pressure and load pressure.
Conversely, servovalves offered highly accurate and responsive control right out of the box. The standard torque motor design that employs a flapper-style pilot valve offers the user inherent feedback to ensure accurate flow regardless of upstream or downstream pressure variations. As the servovalve’s mainstage spool wanders out of position due to flow forces, the linkage attached to the spool directs the flapper to open the opposing pilot passage. Pressure against the spool increases until it centers itself with the flapper. This internal feedback system ensures the servovalve always flows true to the input signal regardless of pressure variations.
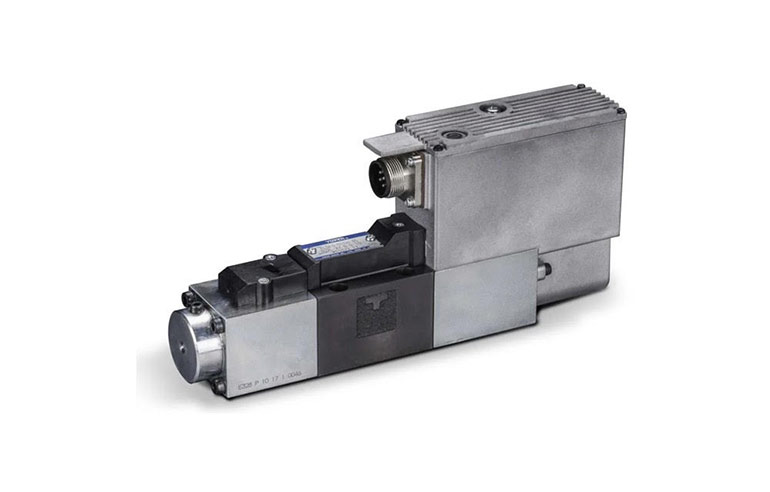
For proportional valves to achieve any level of performance close to a motor-based servovalve, advanced electronic control was required. Because a standard coil-powered prop valve was still susceptible to flow forces, a feedback method was required to maintain the spool in its desired position. Linear differential transducers came to the rescue to monitor spool position down to microscopic distances. The transducer signal feeds back into the valve’s onboard electronics, and when it senses the spool outside of its desired position, the valve adjusts the PWM output to the appropriate coil to bring it back in line with the desired position.
Proportional valves have evolved to be quite sophisticated. The frequency response, accuracy and hysteresis come close to flapper valve performance (and sometimes even surpasses them). In fact, a whole new breed of valves called “high response” have taken to the proportional valve to near servo-valve performance.
Proportional and servovalves also differ by the way they use hydraulic fluid to create flow. A servovalve requires hydraulic tension of sorts and operates with very high pressure drop. Many servovalves require 1,000 psi Delta P to flow what a proportional valve may offer with only 200 psi or less to achieve their rated flow rate.
Servovalves are the more expensive of the pair, not just for initial investment cost but for maintenance. The filtration requirements for servovalves are the most extreme for the entire hydraulic industry. Expect to achieve an ISO cleanliness code of 16/13/10 if you expect long performance life from your valve. A proportional valve makes do with 18/16/13, which is orders of magnitude less efficient; however, both valves are worth the investment in filtration. Neither can be considered inexpensive, but even small servovalves may set you back the cost of a used car – definitely worth the price of maintenance.
Filed Under: Fluid Power Basics, Mobile Hydraulic Tips, Valves & Manifolds