A flow meter is a mechanical or digital device manufactured to measure and indicate flow. The most common flow meter is the mechanical variable area construction type, which employs a spring-loaded orifice-equipped piston. As flow passes the piston, the pressure differential moves the piston assembly against the spring, displaying the flow rate reading.
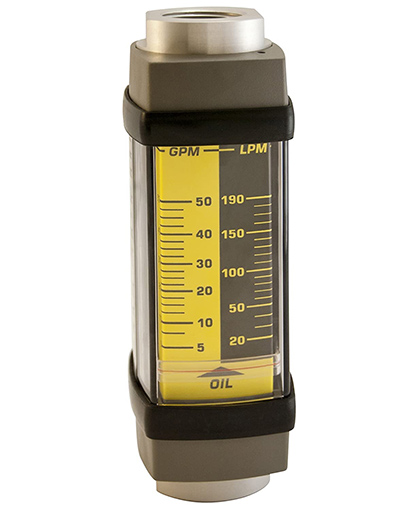
Image courtesy of Hedland
A flow meter should be used or installed anywhere in a hydraulic circuit providing critical operational information for its health and performance. Flow meters may be permanently installed or simply used as troubleshooting components during periods of machine failure. Which installation option employed depends on the initial machine build (and its budget) or the machine build specifications’ depth.
Flow meters are not inexpensive accoutrements, so their location must be thoughtful, especially when large units are required. The cost of flow meters rises exponentially with size, so frequently, only the maintenance team uses them for troubleshooting. Regardless, should the budget exist, a flow meter provides valuable data in various locations.
Installing a flow meter in the primary pressure line(s) of the pump(s) is the first step to understanding your system in breakdowns. I open the conversation to multiple pumps because a grouping run in parallel provides difficulty diagnosing failure when you’re unsure which, if any, of the pumps are not functioning.
The first step to diagnose an unknown stoppage of machine function is first to confirm flow exists. A flow meter installed after a pump confirms pump flow, but also of pump health should the flow reading be reduced. Recording periodic pump flow also provides insight into pump health. If the flow reading drops over time, it may be a sign of pump wear.
Furthermore, adding a second flow meter to the pump’s case drain line provides the maintenance team with additional insight. As a pump wears, its case flow accelerates as more fluid bypasses internally. Regular checks and recordings of the case flow rate will provide clues to pump condition, enable you to change or repair the pump before it fails entirely.
Lastly, flow meters work well in subcircuits with critical functions requiring predetermined flow, especially those related to cycle time performance. High volume production machinery requires 100% throughput. The installation of flow meters before a motor or cylinder circuit allows the production team to confirm that the flow supports the cycle rate. If machine performance drops, the flow meter confirms whether flow to the circuit is the culprit or if they should look elsewhere for the root cause.
Filed Under: Fluid Power Basics