Contributed by Danny Nghieu, EIT, Colonial Seal
Elastomers are widely used due to their relatively high strength, low abrasion rate, and resistance to water, oils, and other chemicals. The mechanical properties of elastomers, namely their tensile strength and hardness, can change over time when the product is sitting in storage. The storage environment will typically dictate the shelf life of a rubber product. Most rubbers are sensitive to temperature, light, oxygen, moisture, heat, and mechanical load during storage. These factors can prematurely age a rubber product, thus negatively affecting its service life either as a raw material or as a finished product.
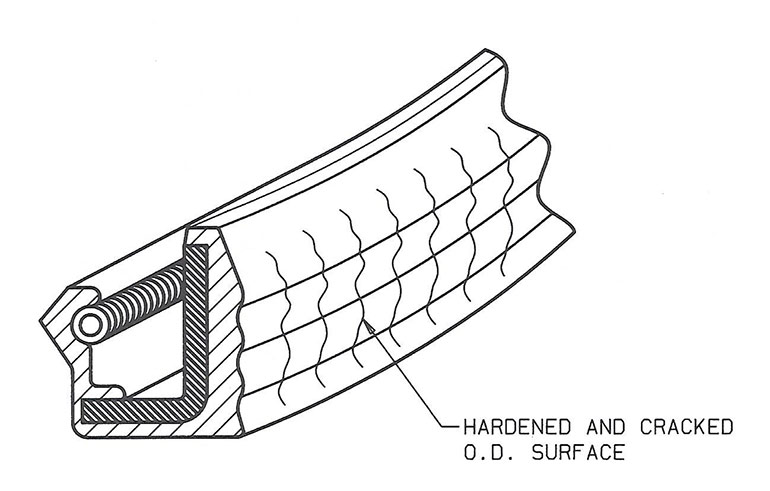
When elastomeric products such as seals are stored for an extended period, they become aged. Naturally, the elastomer will undergo a series of changes that will alter its material properties over time. The molecular chains that make up the elastomer will degrade, a process that starts the day that the material is manufactured. In this article, we will explore how elastomers commonly used in seals can change over time from aging and the effect it has on seal performance. We will also present guidelines on best practices for handling and storing elastomeric products to ensure optimal service life.
Elastomers are natural or synthetic polymers that have elastic properties. The molecular chains that make up elastomers are held together by weak intermolecular forces. Generally, they have low Young’s modulus and high yield strength. They also have the unique property of regaining their original shape and size after being stretched or compressed. Many different types of elastomers can be found in seals such as natural butadiene rubber (NBR), Viton (FKM), silicone rubber (VMQ), or polyurethane (PU).
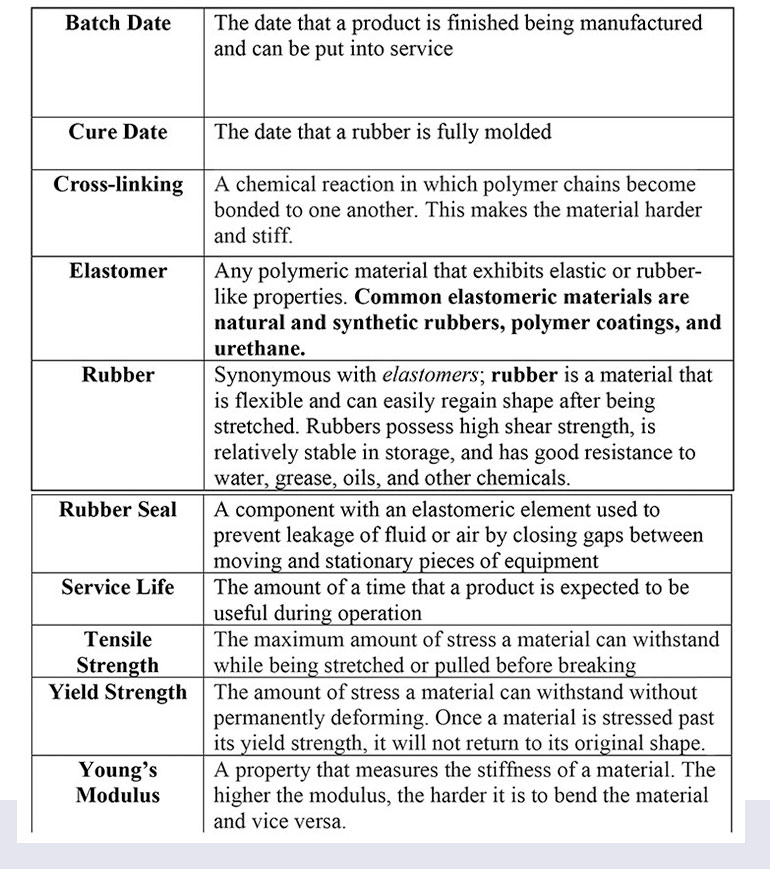
Accelerated aging tests are typically conducted to get a better understanding of how elastomers degrade over time. We will focus on the most common form of elastomer aging observed in industrial applications: thermal aging.
Thermal aging tests are performed to check the ability of a product to withstand elevated temperatures. The tests are typically conducted by placing elastomeric samples inside of a hot air oven. The samples are hung on a turntable inside the oven and rotated slowly to heat evenly and can spend days or weeks in the oven at a high temperature (100 °C+). Physical properties of the samples, such as shore hardness and tensile strength, are then measured and analyzed.
Two primary chemical reactions occur when rubber ages: hardening and softening. Hardening occurs when the polymer chains that make up a rubber start to bind together. Most elastomers found in seals (NBR, FKM, VMQ, EPDM, POM, etc.) will harden with age due to cross-linking (See Table 2). The tensile strength of the material will also decrease, which results in the elastomer becoming brittle (See Figure 1 and 2). Some materials, such as natural rubber or isoprene polymers, can soften with age due to weakening in their molecular chain, but these materials are not often used in sealing applications.
Applications and Testing
Elastomer seals are vital components in most industrial machines. They keep lubrication in and contaminants out. To be effective, the seal should have a proper lip construction and the material should be free of defects. What would happen if you put an aged oil seal into service? Lip materials are typically soft so that they may easily stretch and move into surface imperfections and seal on rough surfaces. If the material ages and becomes hardened, it will reduce friction on the system but may lose its sealing ability. Additionally, because of the strength decrease, it will also be more susceptible to damage and will likely have a shorter service life.
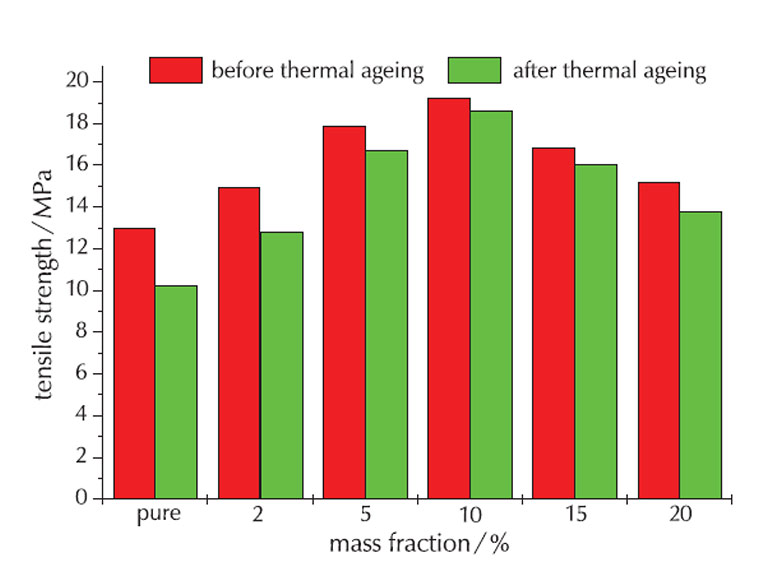
Here at Colonial Seal Company, we have conducted our own independent study on the effects of aging on rubber seals (See Figure 3). Two standard “A” style NBR oil seals were tested on an endurance testing machine. Both seals were stored in a climate-controlled warehouse and kept in original packaging until testing. The test was conducted at 2,000 rpm, 200°F, and kept at a constant 7 psi. Testing ran for 24 hours per day until leakage was observed. An approximate 13% of reduction in useful life was observed in a 6-year-old seal compared to a newly manufactured seal.
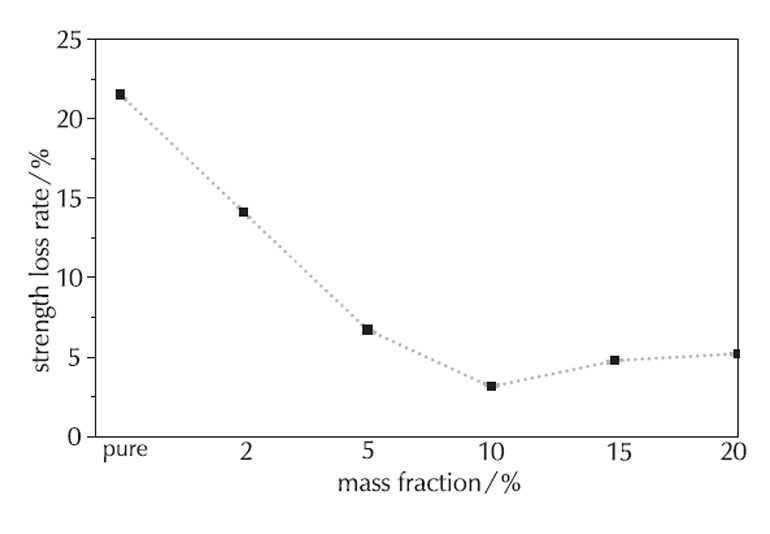
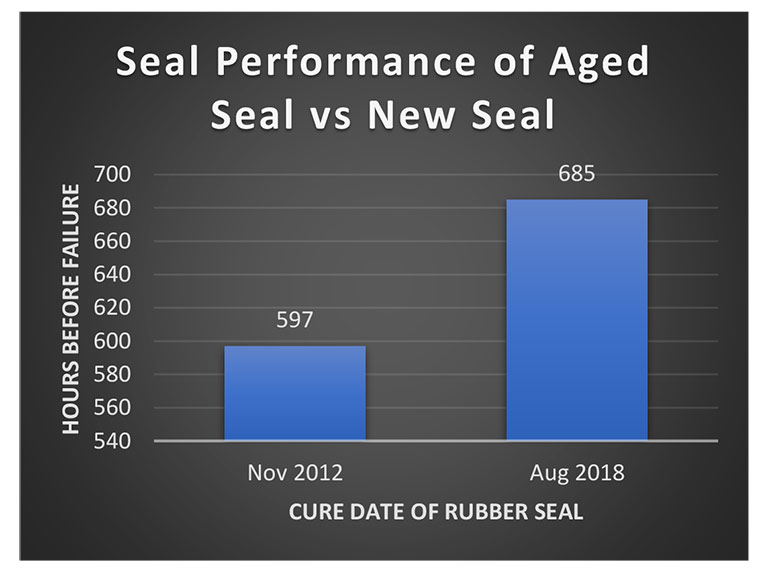
Storage
Elastomers typically degrade at a slower pace if they are properly stored. SAE AS5316 Standard, DIN 7716 and ISO 2230 standards offer best practices for storing elastomer seals. These standards offer the same general guidelines for storage conditions. Ideal storage conditions are as follows:
North American SAE AS5316 recommends a maximum shelf life of:
German DIN 7716 and International ISO 2230 standards are somewhat stricter compared to AS5316. Recommended maximum shelf life per ISO and DIN standards is as follows:
Regardless of which standard is observed, elastomer seals should always be inspected prior to installation. A visual inspection is sufficient to identify dirt, deformations, cracks, tears, discoloration, hardening or softening. Elastomer seals that are in storage should be checked annually. Any products with obvious defects should be disposed of properly.
Summary
An inventory check should always note the inventory age of an elastomeric product. Following an inventory check and inspection, the recommended storage period may be extended. Smaller elastomer seals or seals stored in non-ideal conditions should be inspected more often, perhaps on a semi-annual or quarterly basis. Lastly, FIFO (first in, first out) procedures are recommended to push out old stock and reduce obsolete inventory. This also ensures that when the seals are put into service, they will have an optimal service life.
Colonial Seal
colonialseal.com
References
Chandrasekaran, V. C. (2010). Rubber Properties for Functional Seal Requirements. Rubber Seals for Fluid and Hydraulic Systems, 7–22. doi:10.1016/b978-0-8155-2075-7.10002-4
Korane, Ken. “Storage and Cleaning of Elastomer Seals.” Fluid Power World, 18 July 2018,
Li, Fei-Zhou, et al. “Investigation of Ageing Behaviour of Nitrile-Butadiene Rubber with Added Graphene in an Accelerated Thermal Ageing Environment.” Kemija u Industriji, edited by Nenad Bolf, no. 1–2, Croatian Society of Chemical Engineers/HDKI, Jan. 2018, pp. 29–37. Crossref, doi:10.15255/kui.2017.042.
- Heller, J. Legare, S. Wang and S. Fukuhara, “Thermal stability and sealing performance of perfluoroelastomer seals as a function of crosslinking chemistry,” J. Vacuum Society & Technology A, vol. 17, pp. 2199-2124, 1999.
Y.S. Duh, T.C. Ho, J.R. Chen, and C.S. Kao, Polymers 2, 174-187 (2010)
Filed Under: Sealing, Sealing & Contamination Control Tips