By Josh Cosford, Contributing Editor
Cartridge valves are a type of compact hydraulic valve that slips or screws into the machined cavity of a ported manifold or block. Unlike other valves, such as monoblock lever valves or stackable industrial valves, the manufacturer leaves the porting for you to decide.
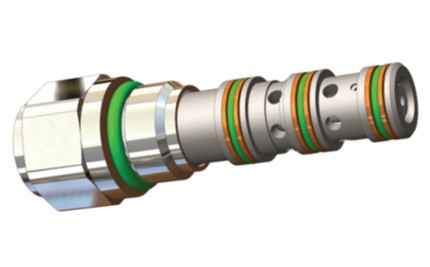
Cartridge valves still use poppets or spools, but rather than move inside of a machined body to open flow paths, they move inside of an integrated cage. Each section, or port, of a cartridge valve is separated from the other through O-rings inside a groove, where the cage itself seals against the machined cavity.
How do you install cartridge valves?
Cartridge valves are installed into their cavities in one of two ways. Screw-in cartridge valves have a thread at their upper shoulder area, and you slide the cartridge into the cavity carefully until you can engage the thread and then tighten it by hand. Once the cartridge bottoms by hand, you use a torque wrench to apply the appropriate tightening force, careful not to overtighten.
Slip-in cartridge valves are also very easy to install. Simply insert the valve into its machined cavity, and then install the cover plate to hold the valve in place. Slip-in cartridge valves are similar to each other in construction, and it’s the cover place that dictates the function of the valve underneath. The very same valve could operate as a directional, pressure or flow valve depending upon the nature of its cover.
What are the advantages of cartridge valves?
Cartridge valves offer near-infinite combinations to provide unique, creative and compact circuits possible no other way. The major cartridge valve players offer dozens, if not hundreds, of versions of their valves. In addition, there are simply some creative functions that are nearly impossible to achieve with traditional inline, monoblock or stackable valves. For example, a post-compensation circuit (also called flow sharing) using a 1 gpm valve alongside a 30 gpm valve could not be achieved any other way.
Also, cartridge valves are compact and inexpensive. In fact, some manufacturers of such valves refer to their products as compact hydraulics. Their compact size permits installation into custom ported hydraulic manifolds housing the entire hydraulic circuit, including the ports and “plumbing” from one valve to the next. In addition, multiple directional, pressure and flow valves make their home in a single machined block, reducing the hydraulic circuit’s size, complexity and leak points.
What are the disadvantages of cartridge valves?
Cartridge valves require a separate body or manifold to operate. Manufacturers offer standard inline, ported bodies, but if your desired port thread isn’t in stock, you’ll have to wait. Unfortunately, waiting is often what you’ll do if you’re in the market for cartridge valves. Because cartridge valves are manufactured to order, unless your local distributor has their own stock, you’ll likely have to wait quite some time.
Cartridge valve manifolds and circuits take some advanced knowledge to apply correctly, especially with slip-in cartridge valves. The beginner designer simply doesn’t have the experience to combine the correct mix of valves, pilots and orifices to make the circuit function correctly.
Screw-in cartridge valves are much more neophyte-friendly, but their performance is less advanced than spin-in valves or many other designs. In addition, their flow is often restricted and is sometimes subject to high leakage rates, both of which are conditions that affect spool-type directional valves, for example.
Filed Under: Engineering Basics, Mobile Hydraulic Tips, Valves & Manifolds