The AirFlowSaver supplies energy- and cost-optimized compressed air based on unique SmartValve technology.
Contributed by Wolfgang Teichmann, CEO and Markus Koenig, CSO, KTW Technology, Wehr, Germany nad Andy Pott, Vice President, PHIR Technologies, Hartland, Wisconsin
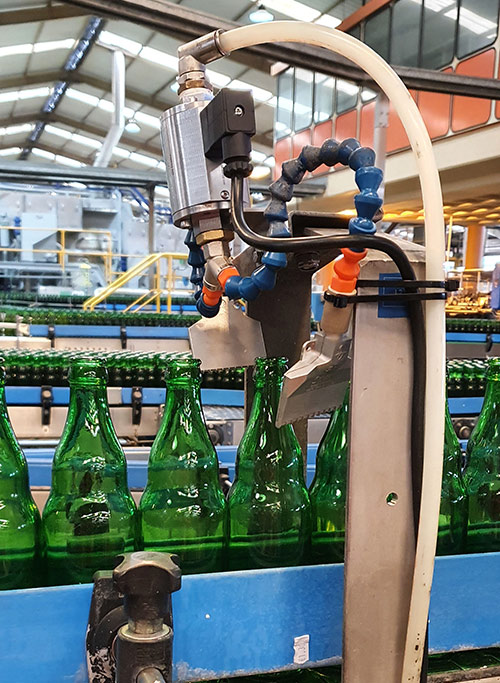
For well over a century, compressed air has been commonly used across many industries because it is a simple, flexible and often indispensable source of energy. Unfortunately, it’s also expensive — in some cases up to ten times more so than electricity.
With growing regulatory and societal pressures to sustainably use resources and mitigate climate change, many companies are looking to reduce the energy consumption in their compressed air systems. Minimizing leaks is one obvious target. And projects to modernize systems and cut costs tend to focus on the generation side, usually by adding new high-efficiency compressors.
Often overlooked but even more important are efforts to optimize consumption at the point of use. Reducing the demand for compressed air in existing applications lets engineers downsize the entire compressed air system, eliminating costly and wasteful over capacities and unnecessary capital investments.
KTW’s AirFlowSaver does just that. It saves energy by reducing the amount of compressed air required by 60 to 90% across a broad range of industrial applications. At the same time, it maintains or improves overall system performance.
Operating principle
The AirFlowSaver (AFS) is an integrated system that cuts air consumption while increasing the output force by converting continuous air flows into sharp and powerful pulses that can last only milliseconds if, for example, a product passes a sensor.
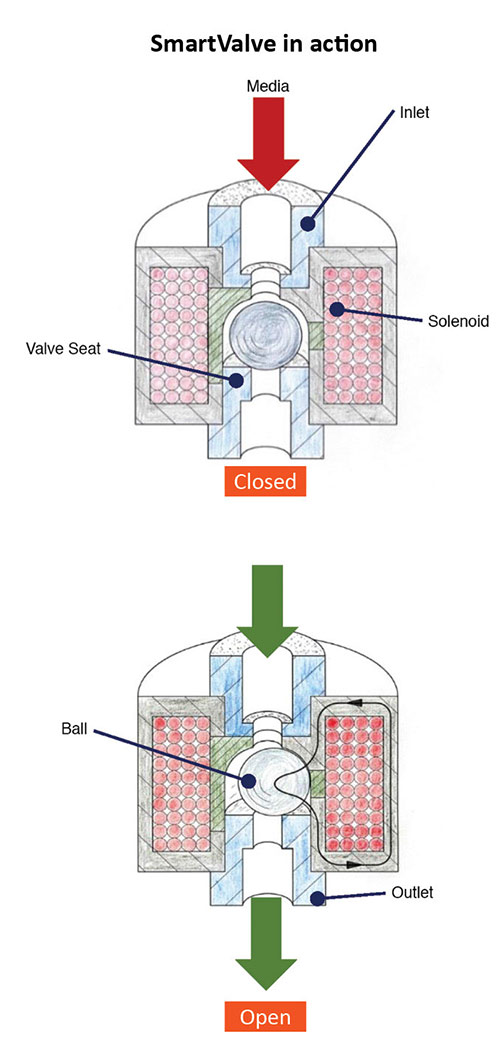
In typical compressed-air systems, initial start-up generates a momentary high-force impulse that quickly decreases as it reaches steady-state conditions. The AirFlowSaver exploits this characteristic by quickly and repeatedly generating high-frequency compressed air blasts. Thus, it maintains a greater force output and lets equipment do more work with faster process times, significantly improving effectiveness in blow-off, cooling, cleaning and drying operations.
At the same time, because the air stream is pulsating and not flowing continuously and blowing only if needed, it significantly reduces the amount of compressed air required, cutting costs. The AirFlowSaver is suited for more than 70% of all compressed air applications.
Some previous attempts have been made at pulsing control in compressed air systems, with limited success. For example, in the past few years valves with modified solenoids have been promoted as using pulsing to save on compressed air. These devices claim energy savings of almost 50%, but savings are more realistically around 25%. Otherwise, outlet force drops too low to be advantageous in most installations. The units are also highly sensitive to back pressure in the airline, so reliability becomes an issue. And these pulsing systems are limited to about 15 Hz frequency and, thus, too slow to adequately clean or dry parts traveling along fast-moving production lines.
SmartValve technology
The basis for the AirFlowSaver system is KTW’s SmartValve, a new type of flow-control valve that relies on a magnetized ball as the fluid-control element. In addition to use with compressed air, the ultrafast switching valve can handle other gases and liquids in dosing systems, sprayers, injectors and many other applications that demand better control and sizable energy savings.
SmartValve technology was originally developed by the German Aerospace Center (DLR) for the European space mission Rosetta, as a cold gas control valve for the Philae lander – the craft which made the first-ever soft landing on a comet nucleus. Over the last few years KTW engineers have further refined the valve design for industrial applications, produced a range of sizes, and developed the power electronics that provides closed-loop control.
The SmartValve features a simple, robust and reliable design. The only moving internal part is a ball that opens and closes the valve. No other components like springs or membranes are necessary.
At rest, a pressure differential between the valve inlet and outlet keeps the ball on the valve seat. To actuate the valve, electric current energizes a solenoid coil in the valve housing. The resulting magnetic field force laterally pulls the ball off the seat — permitting flow. Shutting off power eliminates the magnetic field, flow forces return the ball back to the seat, and the valve closes. Extremely fast (1 msec), direct and stochastic switching allows for real-time applications. The fail-safe valve closes automatically in case of power loss.
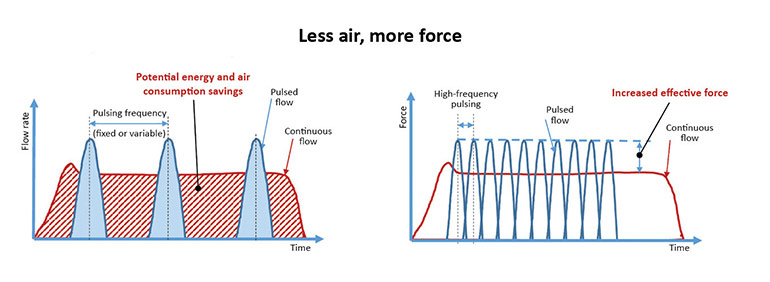
SmartValves typically operate with pressure differentials of between 1 and 10 bar (14.5 to 145 psi), and system pressures can range up to 1,000 bar. Customized versions address special customer requirements. KTW has developed valves to work at pressure differentials of approximately 600 bar and at temperatures as low as -200° C (-328° F) and as high as 400° C (752° F).
Ball and valve seat diameters, and the magnetic system, determine operating characteristics like opening force and switching speed. Varying these parameters lets engineers easily adapt the valve to suit different requirements and applications. For example, applying higher current opens the valve faster, although actual switching speed depends on the fluid and pressure differential. Accuracy depends on the size of the valve and the fluid forces but, in general, pulse-to-pulse repeatability is extremely high, provided that the pressure differential is fairly constant.
The ball, seat and other parts in contact with media are made of stainless steel, and working surfaces are polished. However, certain plastics, such as PEEK, can be used for the valve seat if required. Thanks to the low-friction, low-wear design and minimal mechanical load, the valve has an extremely long service life of more than three billion switching cycles.
The valve resists corrosion and KTW engineers recommend use with particle-free media or installing proper filtration to extract solid contaminants. Unchecked, dirt and debris could lodge between ball and seat and lead to leakage past the valve. Maintenance technicians can remove troublesome contamination by opening the valve and cleaning the seat. Damaged balls and seats are easily replaced.
System considerations
AirFlowSaver performance can be scaled as needed thanks to four standard valve sizes. The smallest offers maximum flow rate of about 14 m3/hr (8.24 cfm); the largest approximately 75 m3/hr (44.14 cfm). Also, a three-ball version produces maximum flow of 85 m3/hr (50.03 cfm).
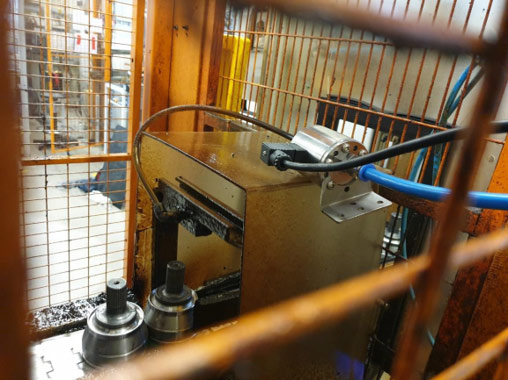
In addition to the SmartValve, other essential AirFlowSaver components include the valve controller, power supply, and sensors that initiate start/stop actions (trigger event). Also critical to overall system performance are application-specific output nozzles and air knives that come in numerous shapes, types and sizes. They optimize flow output, reduce noise and direct the pulsating compressed airstream to the desired target.
All the components are functionally fine-tuned to match the system’s flow, force and efficiency strategy and offer maximum benefits in each specific application.
The AirFlowSaver has three operating modes:
- Continuous pulsing at a predetermined frequency over a fixed time.
- Continuous pulsing with a frequency that varies over time.
- Event-controlled, for example initiated by a sensor signal.
High-performance applications in terms of frequency and flow need closed-loop current control to ensure precise and repeatable valve behavior. KTW’s proprietary Controller Output Stage operates SmartValves at high speeds (reaction time from trigger input to switch of valve = 1 msec) and short switching cycles (from fully closed to fully open to fully closed within 1.5 to 2.0 msec). Depending on the size and media, customized valves can run at frequencies of up to 3,000 Hz.
Duration and frequency of the pulses can be adjusted via parameters in the Output Stage, and pulse-width modulation can control flow linearly. Between fully closed (zero flow) and fully open (maximum flow) every flow rate value can be adjusted by varying the pulsing length and frequency – which means the unit can serve as a proportional valve.
Fast opening and closing of the valve requires a high operating voltage. The Output Stage combines an operating voltage of up to 48 V with closed-loop current control of up to 12 A per channel. Alternatively, it supplies 24 V for lower performance/lower speed applications (two valves per output stage). The Output Stage incorporates the latest MosFET technology to guarantee high output power of over 2 × 500 W. However, actual power consumption is relatively low (≈20 Whr at 10 Hz) because maximum power is only required for the very short duration needed to overcome pressure forces and lift the ball off the seat.
The current control loops also rely on Hall-effect current sensors and FPGA-based state machine logic. A 32-bit microcontroller enables customizable parametrization to match a customer’s individual needs. Communication with the system is via intuitive software (USB interface) or a CANbus network. Thus, users can manipulate valve/pulsing parameters in real time.
Application benefits
Experience at customer installations shows that the AirFlowSaver reduces compressed air-consumption by 60% to 90% — resulting in significant energy savings along with a corresponding reduction in CO2 emissions. Just as important, it improves process quality, as the pulsed beam generates about 15 to 20% higher impulse force compared to a continuous flow. That, in turn, can speed processes and improve productivity.
Depending on the installation, it lets users downsize the compressed air system and avoid unnecessary capital spending. Long service life of the solenoid valve (>3 billion switching cycles), high reliability and a maintenance-friendly design equate to increased equipment and plant availability. And energy efficiency upgrades may qualify for tax benefits. All told, investments in the AirFlowSaver show payback (ROI) in less than one year.
The AirFlowSaver can operate as a standalone unit or as part of an integrated system. The modular design permits distributed mounting of individual components and, thus, can be easily configured and adapted to almost any application and any orientation. And the system is readily scalable in throughput and force via the number and size of valves.
It is suitable for a wide variety of uses, such as for blow-off, drying, degreasing, cleaning, material handling and certain pneumatic control tasks. Specific applications where the new pulse system shows tremendous promise include:
Drying packaged products or beverage containers. Because they are often discretely moving on conveying lines and spaced apart, an on-off system is of great benefit.
Removing unwanted matter. The inherent scrubbing action can remove sticky material from parts with an oily residue. Or similarly, cleaning rough surfaces like wood, where pulsing action helps dislodge hard-to-remove debris.
Part ejection. The amplified force action can move heavier parts on conveying systems.
Cleaning parts. Combining the pulse system with air knives and static eliminators produces cleaner parts in the semiconductor industry. The same holds in painting operations, in particular those involving plastic auto bumpers, door panels and instrument clusters.
Engineers should consider the AirFlowSaver in any industry that is plagued by high consumption of compressed air. That includes metalworking, packaging and beverage bottling, electronics production, painting, and paper, wood and furniture manufacturing, just to name a few.
PHIR Technologies, Hartland, Wis., represents KTW Technology GmbH in North America
KTW Technology|ktwsystems.com
Filed Under: Pneumatic Tips, Valves & Manifolds