For more than 85 years, rupture disks have served as an effective passive safety mechanism to protect against overpressure or potentially damaging vacuum conditions. The disk, which is a one-time-use membrane typically made of metal, is designed to activate within milliseconds when it experiences a predetermined differential pressure. They can be used as standalone devices or as backups to relief valves.
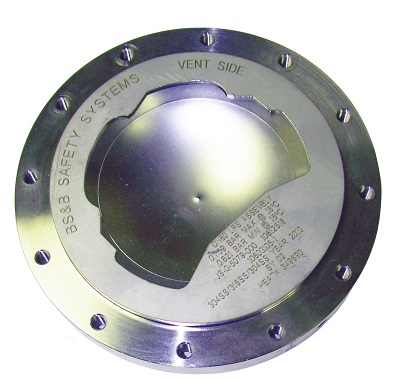
BS&B integrated rupture disk assemblies are generally made of metal components. Due to cost and weight considerations, however, there is increasing interest in housings made of plastics and composites.
Traditionally, individual rupture disks are combined with the manufacturer’s separate supporting holder at the point of use. A quality installation ensures the rupture disk device performs as expected. However, when installed improperly, the rupture disk may not burst at the expected set pressure.
With today’s heightened focus on equipment reliability and safety, OEMs are increasingly turning to integrated rupture disk assemblies as a better option. These assemblies combine the rupture disk membrane, its holder, and a flanged or threaded mounting device into a tightly engineered system. The components are fastened together by welding, bolting, tube stub, adhesive bonding or crimping, based on application conditions and leak-tightness requirements. The one-piece design can be tailored to the application and allows for easier installation and quick removal if the rupture disk is activated. Further, integrated units are certified to perform at the desired set pressure.
Integrated assemblies prevent personnel from using unsafe or jury-rigged solutions to replace an activated rupture disk to save a few dollars or rush equipment back online. And the physical size of increasingly miniaturized rupture disks — as small as 0.12 in. — can make it challenging for personnel to pick up and place the disk into a separate holder.
If you rely on an assembler to insert a loose disk into a holder and then capture it by threading over the top, “unless they follow the installation instructions and apply the correct torque value, there is still potential for a leak, or the disk may not activate at the designed burst pressure,” said Geof Brazier, managing director of BS&B Safety Systems Custom Engineered Products Division, Tulsa, Okla. “When welded into an assembly, the rupture disk is intrinsically leak tight and the set-burst pressure fixed.”
The goal is that the set pressure cannot be altered once the integral assembly leaves the factory. “OEMs are driven to deliver the longest life and lowest cost of ownership to their customers,” he said. “The use of an integral assembly maximizes the longevity, proper function and trouble-free service of the pressure relief technology.”
Rupture disk design
According to Brazier, the most important considerations in rupture disk design are having the right operating pressure and temperature information along with the expected service life, which is often expressed as a number of cycles the device is expected to endure during its lifetime. Because pressure and cycling varies depending on the application, a tailored engineering system is often required.
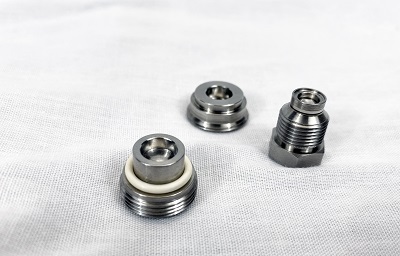
These assemblies are examples of clamped, threaded and torqued designs.
“Coming up with a good, high reliability, cost-effective, and application-specific solution for an OEM involves selecting the right disk technology, the correct interface (weld, screw threads, compression fittings, single machined part) and the right options as dictated by the codes and standards,” he said.
For a wide range of industries, it can be important for rupture disks to have a miniaturized reverse-buckling capability, he continued. In this design, the dome of the rupture disk is inverted toward the pressure source. Burst pressure is accurately controlled by a combination of material properties and the shape of the domed structure. By loading the reverse buckling disk in compression, it can resist operating pressures up to 95% of minimum burst pressure even under pressure cycling or pulsating conditions. The result is greater longevity, accuracy and reliability. In almost all cases, reverse buckling rupture disks outperform the alternatives with respect to service life.
“Where economics is the driver, reverse buckling disks are typically made from materials such as nickel, aluminum and stainless steel. Where aggressive conditions are required, more exotic materials like Monel, Inconel, Hastelloy, titanium and even tantalum can be used,” said Brazier.
“The process industry has relied on reverse buckling disks for decades. Now the technology is available to OEMs in miniature form as small as one-eighth inch burst diameter. Until recently, obtaining disks of that size and performance was impossible,” he said.
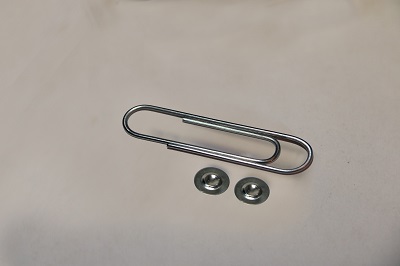
Custom-engineered miniature rupture disk assemblies have diameters as small as 0.12 in.
However, miniaturization of reverse buckling technology presents its own unique challenges. To resolve this issue, BS&B created novel structures that control the reversal of the rupture disk to always activate in a predictable manner. In this design, a line of weakness is typically added into the rupture disk structure, to define a specific opening flow area when the reverse type disk activates, and to prevent fragmentation of the disk “petal.”
Small nominal size rupture disks are sensitive to the detailed characteristics of the orifice through which they burst. This requires strict control of normal variations in the disk holder. “With small-size pressure relief devices, the influence of every feature of both the rupture disk and its holder is amplified,” explained Brazier. “With the correct design of the holder and the correct rupture disk selection, the customer’s expectations will be achieved and exceeded.”
Fluid power applications
The integrated assembly is suited for numerous hydraulic, pneumatic and other low- to high-pressure devices including pumps, piston and bladder accumulators, pressure vessels and piping. And they are used in a wide range of other markets, including OEM equipment for onshore/offshore oil and gas applications, pressure washers, refrigeration systems, fire protection and breathing equipment.
For example, the oil and gas industry uses rupture disks on triplex pumps for many oil extraction and well-servicing operations. These pumps are configured with three plungers. Commonly referred to as “mud pumps,” the devices typically can handle a wide range of corrosive and abrasive fluids and slurries containing relatively large particulates.
Pump pressures depend on the depth of the drilling hole and resistance of flushing fluid, as well as the nature of the conveying drilling fluid, and are typically in the 5,000 to 20,000 psi range. “A three-plunger pump is continuously cycling, so the disk must be able to withstand high pressures with one-million pressure cycles or more easily experienced,” said Brazier.
Hydraulic accumulators that store energy and smooth out pulsations likewise require rupture disks. By definition, accumulators hold hydraulic fluid under pressure. If pressure spikes too high, there is a risk that without a rupture disk the accumulator or system could experience a catastrophic failure.
While OEMs have long relied on rupture disks in their hydraulic and pneumatic equipment, high-pressure, high-cycling environments have been particularly challenging. Fortunately, with the availability of integrated, miniaturized rupture disk assemblies tailored to the application, manufacturers can significantly enhance equipment safety, compliance, and reliability even in extreme work conditions.
BS&B Safety Systems
www.bsbsystems.com
Filed Under: Accumulators, News, Safety