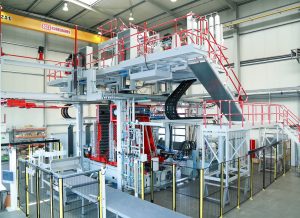
Blow molding plant for plastic products at Roth Hydraulics USA in Watertown, New York.
There were significant challenges when Roth Hydraulics needed to design and install a large new blow molding plant for plastic products at its production site in Watertown, New York. The project connected the manufacturer’s skills in two fields — hydraulics and plastics processing. The design of the new hydraulic accumulator system now permits high-speed production, ample power reserves, and substantial energy savings.
Weighing in at 125 tons and with a clamping force of roughly 300 tons, the blow molding plant is equipped with three extruders. The production plant is also fitted with three sensor-controlled piston accumulator systems for various hydraulic functions in the production process. Roth chose this configuration because hydraulic energy is required to open and close the nozzles, to extrude the plastic tube, and for all movements that the blow molding plant undertakes.
The hydraulics facilitate movement in the plates, the two-part mold, the blow pin and blow needles for letting in air, the mold closing mechanism during the blow molding process, and the control of the wall thickness of the plastic. Both halves of the mold can be moved separately, allowing them to move both in and out of synch and at different speeds. Cylinders fitted with locking devices at the four corners of each mold half regulate the clamping force. Clamping cylinders support the mold as it closes to a precise fit while withstanding blowing pressure of up to 87 psi.

Roth Hydraulics pressure vessel plant with a customer-specific screw joint system.
The mold itself weighs 15 tons (7.5 tons per half) and can open by up to 9,84-ft at a speed of 11.8-in. per second. Each piston accumulator system has a working pressure of 2600 psi and a maximum pressure of 3100 psi. Proportional valves control how the two mold halves close and how the plastic tube feeds into the blow mold.
are available with a maximum operating pressure of 5100 psi, while customized designs can handle up to 17500 psi with variable pre-load pressure.
Filed Under: Accumulators, Fluid Power World Magazine Articles