The term hydrostatic refers to the fundamental concept we hold dear in fluid power, which is that confined hydraulic fluid under pressure exists in equilibrium and balance. Although hydraulic fluid does no more than hold objects stationary without the active application of force through a pumping device, the concept is entirely different than hydrodynamics, which recruits liquid molecules to create kinetic energy to achieve work.
So, if all hydraulic pumps are hydrostatic, what makes a hydrostatic pump different, and when should you use it? Hydraulic pumps, by and large, are used to create hydraulic pressure and flow for hydraulic systems of non-specific applications and purposes. However, the hydrostatic version is still a hydraulic pump but one specialized for closed-loop hydraulic systems.
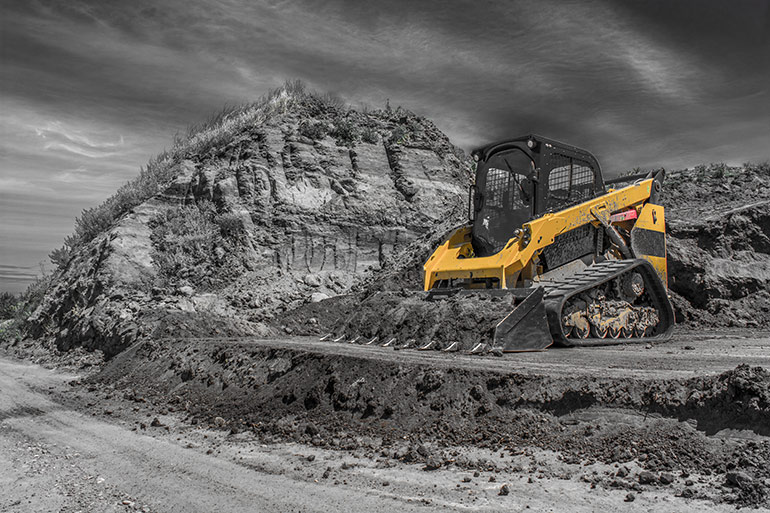
A closed-loop hydraulic system is one where the fluid exiting the pump flows directly to the actuator (usually a motor) to perform work before returning directly to the pump. A hydrostatic closed-loop drive provides a dedicated, controlled source of hydraulic energy to an actuator without the accoutrement of traditional open-loop (fixed flow) hydraulic systems, such as reservoirs, valves and accessories.
The variable displacement, pressure-compensated hydrostatic piston pump includes its own specialized componentry to support such a dedicated and otherwise sketchy task. In fact, at first glance, you would question the decision to river hot, dirty hydraulic oil through a pump motor combination, which would seemingly last only a few hours. Suffice it to say, it’s not that simple, or they wouldn’t exist.
The hydrostatic pump doesn’t operate using a reservoir, per se, because fluid flows through a dedicated circuit to and from the motor, although reservoirs often exist on the machines where these systems are installed. Instead, the drive package has a medium-pressure charge circuit that bleeds off hot oil, filters the fluid and replenishes clean, cool oil to keep it fresh. Cooling systems on mobile machines are robust enough to tackle the high heat load and are often hydraulically driven themselves.
The most common uses for hydrostatic pumps are drives for mobile machinery, such as bulldozers, skid steer loaders, and excavators. Typically, you see two pumps driving two motors, each on either side of the vehicle, which allows the independent operation required for steering. Hydrostatic pumps typically run over center, meaning their flow direction is reversible, allowing backwards travel without any traditional gear-driven transmission. In fact, the drive wheels can turn in opposite directions so the machine can pivot on-center.
Any application that can use a high-powered, efficient and versatile power transmission method is suitable for a hydrostatic pump. From landscaping to agriculture or from material handling to marine, these industries have various machines taking advantage of closed-loop drives. Lawnmowers offer zero-turn functionality, for example, and mobile shredding trucks offer robust, compact systems that run off the truck’s PTO.
Manufacturers have explored using hydrostatic pumps for advanced energy-saving concepts, such as the hydraulic hybrid system for delivery vehicles and garbage trucks. Using a hydrostatic motor that also works as a pump, the kinetic energy of the slowing vehicle attached to the transmission pumps fluid into accumulators as the vehicle flows. These accumulators then release the stored energy as the vehicle accelerates, reducing the demand from the internal combustion engine, thereby saving fuel and reducing CO2 emissions.
If you’re considering a hydrostatic pump for your application, consider whether you need a dedicated drive system or one with various valves and actuators instead. Also, consider if you need variable speed, torque and power from your motor, especially with dynamic changes from moment to moment. Finally, consider cost, as hydrostatic drives are a premium option that puts productivity ahead of price. If these considerations meet your requirements, a hydrostatic pump provides a perfect solution.
Filed Under: Components Oil Coolers, Engineering Basics, Mobile Hydraulic Tips, Pumps & Motors, Technologies