Dust collector systems play a critical role in maintaining compressed air cleanliness for manufacturers. Plant operators are always looking for any incremental advantage to improve pulse jet cleaning in bag (sock) or reverse flow cartridge systems. This is because even the slightest improvement in dust cake contaminate removal can create a cost-improving ripple effect throughout the system by increasing bag life and reducing compressed air consumption (CFM) through less frequent pulsing.
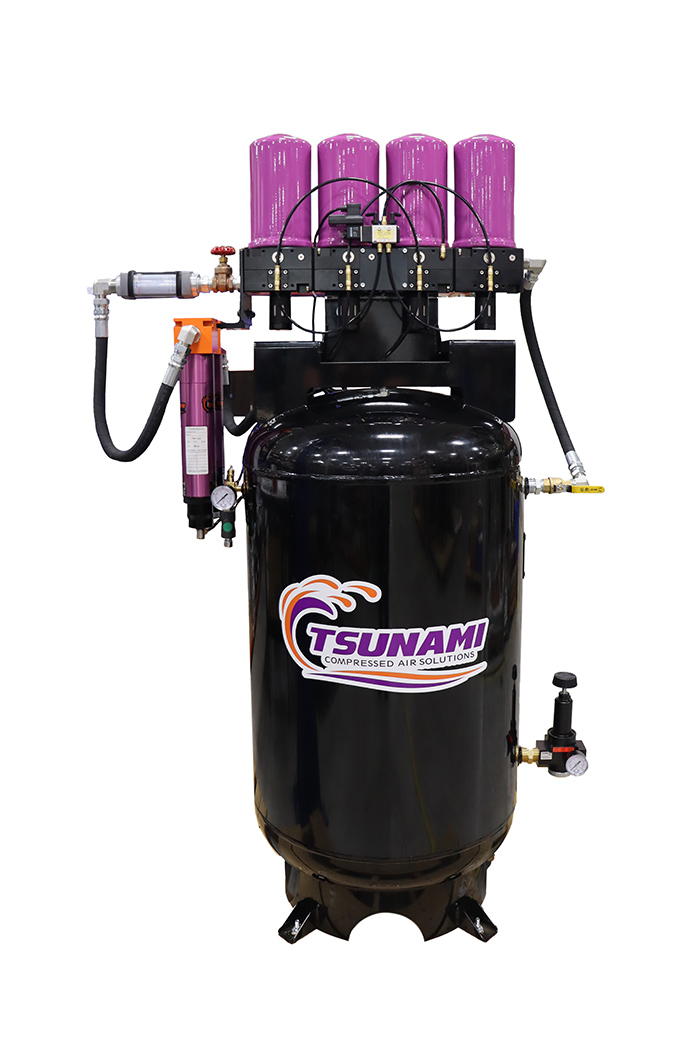
Suburban Manufacturing’s Tsunami Tank-Mounted Regenerative Air Dryer
What if engineers, plant managers, and operators have been missing the key component to radically improving system effectiveness all along? What if there was a total solution available to optimize and protect the entire process? Suburban Manufacturing’s Tsunami Tank-Mounted Regenerative Air Dryer is revolutionizing how manufacturers maintain their dust collector systems for absolute performance at minimal costs.
The challenge faced in every dust collector application is to maximize pulse effectiveness and extend bag life, while minimizing energy consumption in the form of compressed air. The system is optimal when the pulse interval effectively removes dust cake to the point where the filter life meets or exceeds the manufacturers’ specification. Unfortunately, this scenario very rarely occurs, if ever.
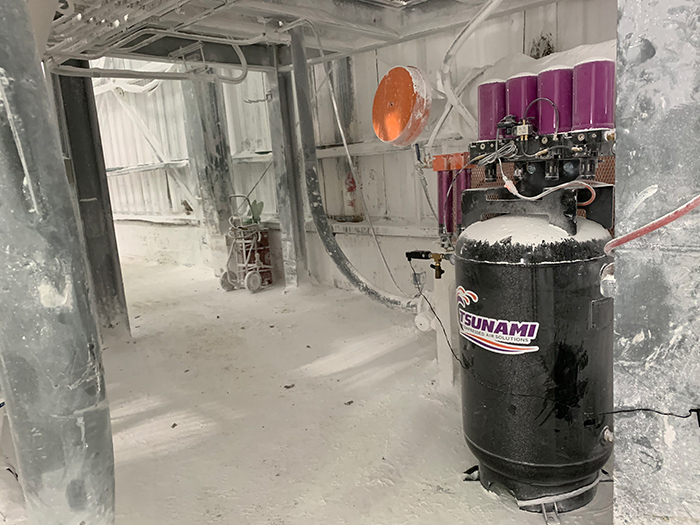
A tank-mounted regenerative dryer at a tire plant helped dry air down to at least a -40°F dew point. This helped the pulse valves clean the bags more effectively, and cycled 50% less often than before the dryer was installed.
While advancements in pulse valves, filter bags (socks), and pressure differential controllers show supporting data that doctor efficiencies in collector performance, this technology focuses on an incumbent enemy, that if corrected, will dramatically extend the life of all system componentry. Because dust collectors consume less than 30 cfm, on average, operators typically pay little attention to the quality of compressed air being supplied. Even though these collectors have low flow specifications, measured in cfm, the actual volume of air per pulse dramatically exceeds that specification.
What happens to this high volume of air as it rapidly exhausts out the orifice of a pulse valve is the underlying issue termed supercooling — this is what Tsunami addresses with its bag house drying technology.
Supercooling explains the rapid expansion of air that loses heat due to the immediate separation of molecules. Simply put, for every 20°F that air cools, it loses approximately 50% of its ability to hold moisture in the form of vapor, or humidity. In collector applications, this cooling effect converts water vapor to liquid as air quickly expands out of each pulse valve. Damp air hits the bags or elements creating a wet cake substance that prematurely clogs the filter and inhibits air from passing through. Not only does this wet air reduce the life of each filter, it also wreaks havoc on collector systems in climates where freezing may occur.
Having excess storage of ultra-dry air in dust collector applications is necessary for eliminating moisture within the system and increases the life and efficiency on the system.
Tsunami Compressed Air Solutions has designed an all-in-one regenerative air dryer to eliminate air-related issues that prevent a dust collector system from operating proficiently. Let’s examine how the system works.
Air travels into the zero-maintenance water separator where water is removed and particles are filtered down to 10 micron. Before exiting the pre-filters, the oil coalescing element removes aerosols down to 0.001 ppm and particulates down to 0.01 micron.
A gate valve and flow meter, integrated before the inlet of the dryer, helps prevent the collector from overrunning the system.
Pretreated air enters the regenerative dryer where dew points and relative humidity are lowered down to -40° F and 0.01% RH. The technology features self-regenerating towers to eliminate the need for manually changing desiccant. This level of air quality prevents the chance of moisture creation during the supercooling process.
A small amount of dry air is reverse-flowed to purge out the humid desiccant while the bulk of the air is stored in an 80-gal receiver tank. This excess storage of ultra clean, dry air is essential to supply the high surges of flow experienced during pulsing. To accommodate for these spikes in demand, a high-flow regulator is utilized on the tank outlet port.
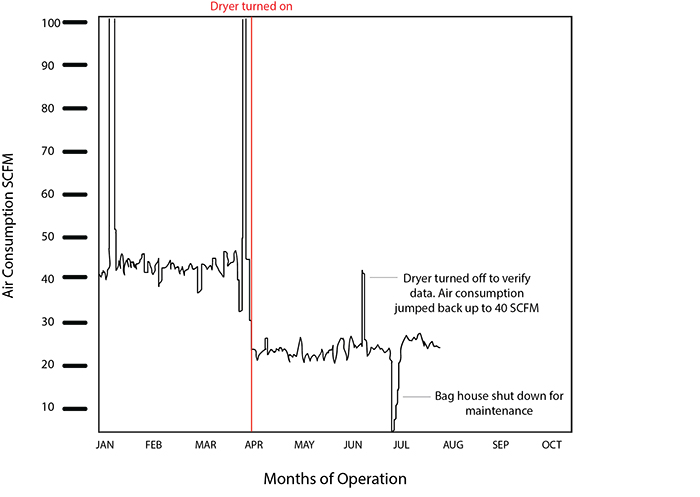
If monitoring compressed air quality is desire, a test port is located on the inlet side of the receiver tank.
In one example, a tank-mounted regenerative dryer was installed at a tire plant and then monitored by use of a data logger. The goal of the installation was to reduce the air consumption and improve bag life. Dust collectors were filtering carbon black and the pulse valves cycled off a photohelic pressure switch that unintentionally robbed the plant’s air capacity.
After just days of being installed, it was discovered that by using dry air with at least a -40° F dew point, the pulse valves cleaned the bags more effectively, and cycled 50% less often than before the dryer was installed.
The included chart shows the data logger that was used to capture air consumption during the study. The dust collector dryer reduced the amount of air/pulses considerably. The facilities engineer stated that the effectiveness of each pulse extended the filter life by two times and estimated the return on investment to be about three months.
Suburban Manufacturing
gosuburban.com
Filed Under: Pneumatic Tips