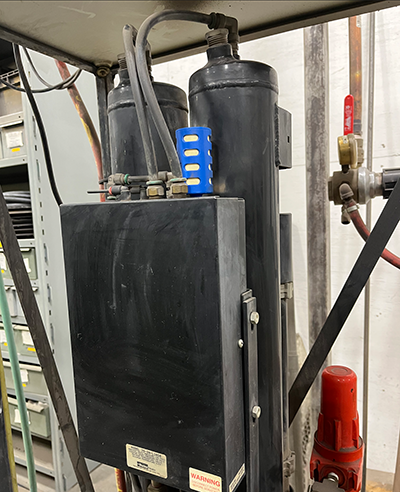
A metal processing company had a laser cutter installed in its manufacturing plant to produce accurately fashioned pieces from metal sheets. This machine requires compressed air that is dried to about 35° F for general use but requires a small amount of air to keep the beam path clean —this avoids contaminating the expensive positioning mirrors (which cost $800 each). This cleaning application requires about 1 cfm of 35 psi compressed air, dried to instrument quality to supply an air purge.
The main system in the plant has a refrigerated air dryer that is transported through main plant piping to the laser dryer infeed. On the laser infeed is a refrigerated air dryer to process the compressed air input. Further to this, the air is passed through a membrane dryer to produce an instrument air quality flow. And finally, just in case, the air is passed through a fixed cycle heatless desiccant air dryer before being sent to the laser. The air that is feeding the beam purge is dried four times!
Measurements showed that the laser dryer system was consuming 22 cfm of air, which was about 45% of the total air flow in the plant. The plant only has an 8 hour, 5 day per week production shift. However, the compressed air system was kept on 24 hours, 7 days a week so the laser beam purge can be running constantly. This means the dryer system runs full time, even though the laser is used only a few minutes per day.
Estimated equivalent energy costs for the dryer system is $4,400 per year. The cost to feed the additional plant leakage during non-production hours, measured at 28 cfm nights and weekends, is estimated at $4,160 per year. Plus, due to the high number of hours on the air compressor, the plant recently received a service bill of $15,000 for a rebuild. The Plant Manager’s jaw hit the floor when presented with these costs. Let’s put this in perspective — all this incurred to avoid the unlikely failure of an $800 laser mirror.
This case represents an extreme level of waste for a small plant drying system. An engineering review is underway to make improvements.
Filed Under: Components Oil Coolers, Compressed Air Technologies, Pneumatic Tips, Technologies