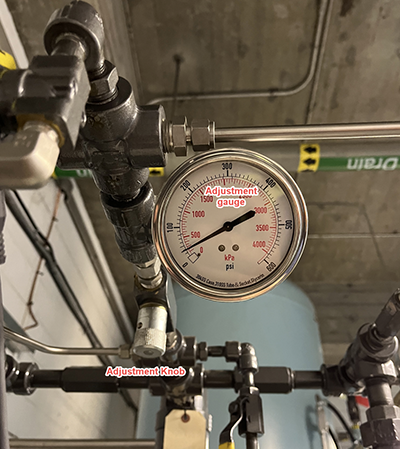
An industrial compressed air user was having a difficult time with their high pressure compressed air system. The compressed air demand required instrument quality air, so a heatless desiccant air dryer was installed.
The dryer uses activated alumina within its chambers to strip off the moisture from the compressed air flow using an adsorption process to reduce the dewpoint to -40°. To achieve this, the dryer dries with one of its two chambers and regenerates the desiccant in the other chamber by passing a flow of already dried compressed air through the regenerating beads. The flow of air normally consumes about 15% to 20% of the dryer full flow rating. Every 5 minutes, the dryer switches sides so the desiccant within always remains activated.
The customer called in an auditor to take a look at the dryer, as it was causing compressor problems—and wasn’t drying the air adequately. They noticed when the dryer was online, the main and the backup compressors ran, but when bypassed only one compressor was needed to keep up with the air demand. They had already replaced all the dryer control and check valves and had a service technician in numerous times … but the problem remained.
The auditor placed a flow meter on the dryer mufflers to measure the purge flow. Despite having a correct pressure reading on the dryer purge adjustment gauge, the dryer consumed about 6 times the expected flow, more than the capacity of the main compressor. A quick adjustment of the purge adjustment valve reduced the flow to a normal level, correcting the problem.
It turns out that a purge orifice, normally installed in the purge flow path, was missing. Thus, the purge gauge could not be used to do a proper adjustment. Previous service personnel used the gauge, but this resulted in a much higher flow due to the missing part, overloading the compressors and causing them to overheat.
Sometimes a different perspective is needed to solve a vexing problem.
Filed Under: Components Oil Coolers, Compressed Air Technologies, Pneumatic Tips, Technologies