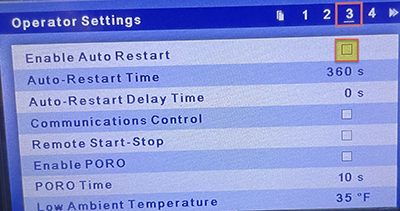
One little button click can save thousands of dollars in wasted electrical and maintenance costs on air compressors.
Recently, a compressed air auditor encountered the same problem in two different plants; operators had failed to select “Auto Mode” on their compressors. Both units were 150-hp lubricated screw compressor installed in a system of multiple compressors.
These units were set up to run on a standard cascaded pressure band arrangement where the units were only needed if the others with higher priority couldn’t keep up with the compressed air demand. The problem was, if Auto mode is not selected, the compressors will run continuously in the unloaded condition even when they are not needed. This was consuming significant power and accumulating maintenance hours, but producing no compressed air.
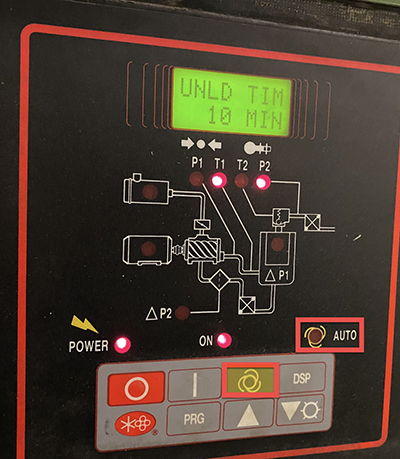
An unloaded compressor in continuous run mode will consume about 30% to 35% of its full load power. For these compressors, the unloaded power consumption was 45 kW, worth about $450 in wasted power for every 100 hours of unloaded operation.
If the Auto Mode was selected by simply checking the box or pushing the Auto button the compressors would time out and turn off — saving power but remaining armed to start should the compressor be needed to supply the peak plant demands.
For this system to work, there must be some significant storage receiver capacity present to slow down the pressure fluctuations. The Auto timer settings need to be long enough to prevent excessive motor starts but short enough to turn off the compressors to avoid wasted energy. These compressors are set at 6 minutes and 10 minutes respectively, which is typical.
Both compressors had run in excess of 15,000 hours unloaded during each lifetime due to this problem! This represented about $67,000 in lost power costs at each plant over the life of each compressor.
If you have this problem and your compressors have high unloaded run time, it may be wise to exercise your pointer finger and give Auto mode a try.
Filed Under: Components Oil Coolers, Compressed Air Technologies, Pneumatic Tips