What if you could reduce all your leaks without turning a wrench? Well, it is possible with good pressure control. And sometimes it is as easy as turning a knob.
The principle is shown in the following orifice chart, Fig. 1. As the pressure to a leak reduces by 1 psi, the flow consumed by the leak reduces by about 1%. This is significant because most compressed air systems operate at a pressure that is higher than what is needed. Also, it is common to find most pressure regulators installed in a system set higher than needed — or even so high the output is tracking the compressor discharge pressure.
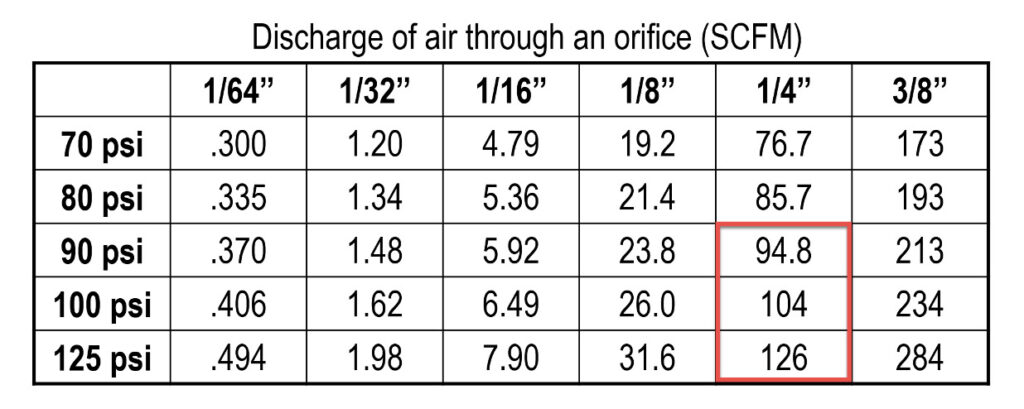
Two common options are available to lower the pressure. The first is to simply reduce the compressor pressure settings, this will reduce the leakage flow (sometimes called artificial demand) and reduce the power the compressor is consuming, a double benefit. The second is to reduce the regulated pressure to the plant (leaving the compressor pressure the same). This can be accomplished using a pressure/flow controller on the main system or by reducing the pressure at local pressure regulators.
An example is the vehicle service shop, the profile of which is shown in Fig. 2. This shop had a main pressure/flow controller already installed but it was not being used due to mis-adjustment. The flow during off hours was 65 cfm — costing $12,525 annually to supply. After the pressure regulator was adjusted to slightly under 98 psi, the leakage flow dropped by 10 cfm, saving $1,925 per year.
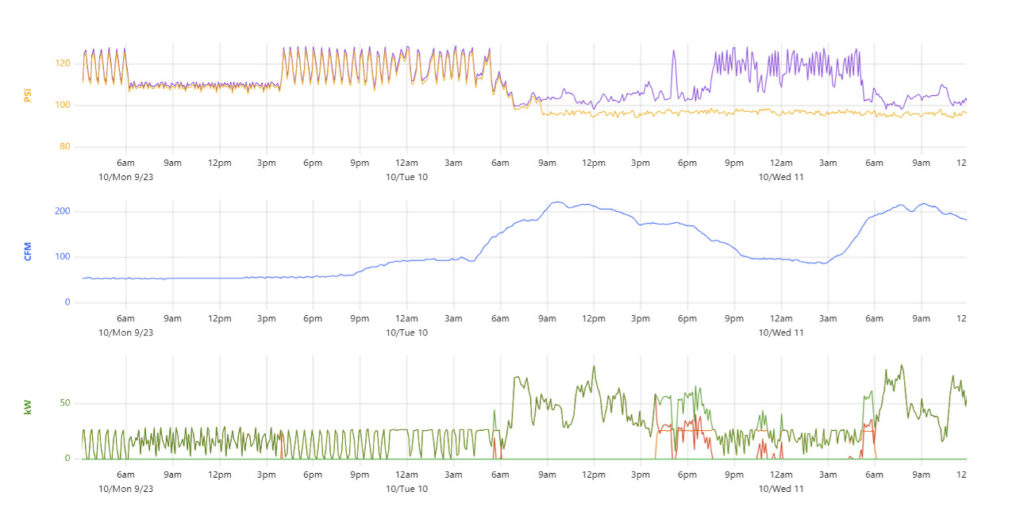
Of course, the most obvious measure that could save even more besides actual leakage repair would be to reduce the plant pressure to zero by turning off the system during off hours. In this case, these hours accounted for about 4,000 hours of system operation, a significant chunk of change.
Reduce your leaks in whatever way you can and save operating costs!
Filed Under: Components Oil Coolers, Compressed Air Technologies, Engineering Basics, Pneumatic Tips