A large automotive service shop had two 100-hp compressors, one being a VSD, both available to supply the compressed air they needed for painting and body assembly of large vehicles. The load was full of peaks, and the maintenance staff needed up to 400 cfm to provide flow to paint booths and breathing air hoods during peak periods. However, there were long periods of time where almost no compressed air was used; then, the loading would fall to 40 cfm, well below the minimum speed of the VSD.
VSD compressors, or even fixed-speed units running load/unload, have trouble with light loads. This is because very little heat is generated within the compression elements, as the units are running mostly unloaded. And because of this screws would run under-temperature water that would accumulate in the compressor lubricant, causing serious maintenance problems. Furthermore, the energy efficiency of the lightly loaded compressors was very poor, sometimes reaching greater than 40 kW per 100 cfm (normal is about 20 kW per 100 cfm).
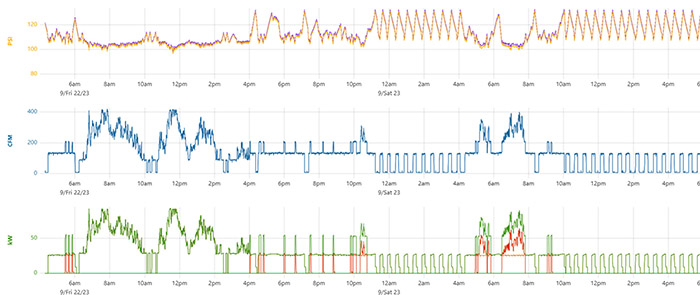
To counter this problem, a compressed air auditor suggested that a small fixed-speed “pony” compressor be used during evenings and weekends instead of the large compressors. For this facility, these low-load periods added up to more than 50% of the total operating hours.
A unit was purchased with the help of a local utility incentive program. This compressor, combined with large storage, ran in start/stop mode with very little unloaded run time, producing air at about half the specific power of the previous operating mode. Within the compressor controller was an automatic scheduler that would bring the compressor on during lightly loaded periods. This operation greatly reduced the operating hours of the VSD compressor and prevented it from running so many hours below minimum speed. This keeps the service man happy!
The more efficient operation, which saves more than $10,000 per year, and lower maintenance costs, will quickly pay back this compressor purchase in less than 2 years.
It is good to have a compressed air auditor look at compressed air systems, especially if you take their advice.
Filed Under: Components Oil Coolers, Compressed Air Technologies, Pneumatic Tips