A farm implement manufacturer expanded its facility about 15 years ago, and personnel decided they wanted a premium compressed air system. They purchased three very efficient two-stage premium compressors, one being a VSD, and connected the equipment with large piping to reduce pressure loss. Filters were mist-eliminator style to reduce pressure loss. Air dryers were cycling style to save energy due to refrigerant system turn down. A pressure/flow controller was installed to reduce plant pressure to 90 psi, and a large 5,000 gallon storage receiver protected the system from high peak demands.
Site measurements showed that this system was producing air at an optimum 17 kW per 100 cfm specific power, a very low level that reduced the system’s operating cost significantly compared to a standard system.
As the years went by, however, equipment started to wear out. First, one of the fixed speed compressors failed and needed an expensive overhaul. The management staff decided to replace it; however, they looked to get the best deal on the new compressor and purchased a less expensive single stage unit with much higher specific power than the previous unit.
Then one day, the VSD compressor failed. As it was quite old, a replacement was ordered — but again they went with the lowest cost unit, a unit that was smaller than the base units was chosen. This caused a problem called control gap where the base compressors fight with the VSD.
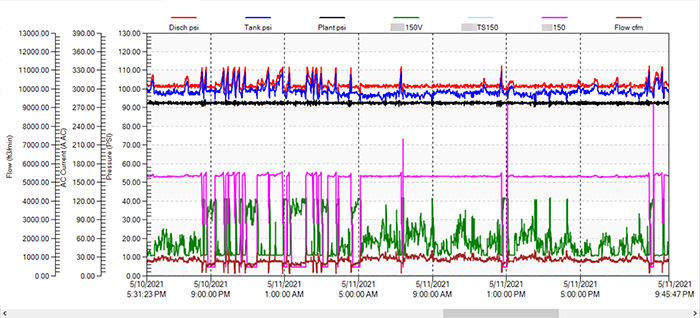
These were 150 hp units. Their compressed air auditor pointed out that for compressors this size, running on a 24 x 7 basis, the difference in specific power can really add up when you calculate the energy costs. For example, the cheapest base units they purchased were consuming about 25 kW more than the premium choice compressors while producing the 800 cfm average flow. This consumed about $21,000 a year more in electrical costs, working to about $105,000 in extra costs over the last 5 years! This higher annual cost quickly consumed any savings they gained in purchasing the cheaper models.
In compressed air systems, remember that pinching pennies on equipment purchases sometimes can cost you a bundle.
Filed Under: Components Oil Coolers, Compressed Air Technologies, Pneumatic Tips