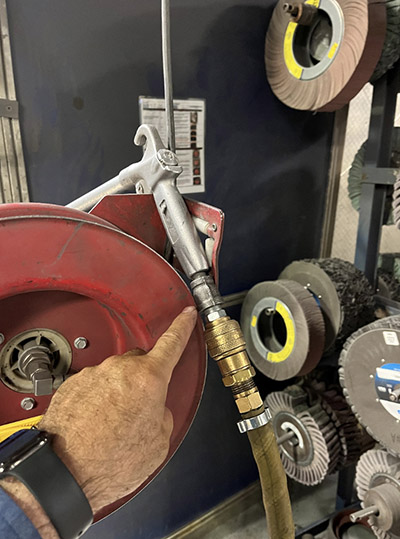
If you have ever done leakage detection with an ultrasonic leak detector you will get to know the common leak locations. If you have no detector, there is no excuse these days, excellent equipment is available for you to purchase at a reasonable price, go get it!
A common sight — or rather sound — is finding leaking hoses that connect to hand tools and blow wands. Red rubber hose is very commonly used in industrial plants and shops, sometimes thousands of these hoses are present, with many leaking in various spots, all usually due to poor installation or wear.
It is very common to find tools installed with fittings that have no thread sealant. It is very important to ensure that steel connectors have sealant applied to stop air leaks. Fig. 1 shows an example. This fitting has likely been leaking from day one, and over time, due to the constant stresses from daily tool use, the fittings have become loose, causing a significant leak flow.
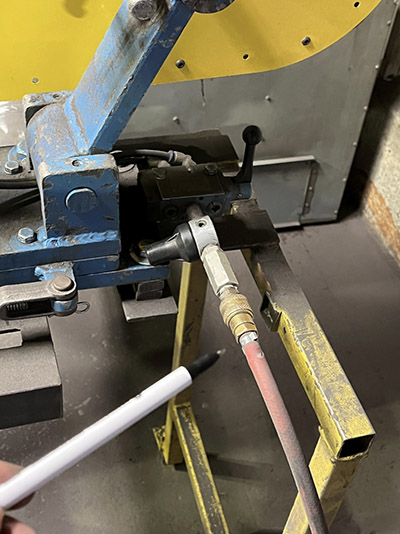
Fig. 2 shows another common problem, the use of old-style crimped connections. These connectors often damage the hose on installation and will loosen as the hose end gets worn from constant use. These connectors and similar screw type bands can become damaged and start to leak if production machinery like forklifts drive over them, distorting the connector. These days push lock connectors and high quality hose are being used in plants that follow Best Practices.
Another common leak location is the quick connect couplers at the end of each hose or the hose itself though pinholes that develop if the hose is damaged or melted due to welding slag.
Keep an eye out for hose and connector leaks. Ensure your hoses are installed correctly.
Filed Under: Components Oil Coolers, Compressed Air Technologies, Pneumatic Tips