By Ken Korane, Contributing Editor
Food and beverage processors and packagers strive to move goods as quickly, efficiently and safely as possible without damaging the end product. Sometimes the work is done by hand, but automated systems are often preferred to speed throughput and ensure quality. Devices like pick-and-place gantries, delta robots, and SCARA pickers work great when handling one piece at a time. But when moving dozens of parts at a time, vacuum “layer” grippers are often a better option.
These large-footprint systems mount to handling devices like robots or forklifts and take advantage of the physics of vacuum to cleanly and firmly grip, move and place products precisely where needed. What sets innovative designs apart, however, is how these gripping systems are engineered and built.
Modular benefits
Increasingly, package-equipment manufacturers are shying away from expensive, one-off systems with long lead times and only suited for a single task; and from standard, off-the-shelf systems that save money but compromise performance. Instead, design engineers are turning to modular systems as a faster and more-economical approach. These are built from standard components and subsystems, but the end product can be uniquely tailored for size, speed, energy efficiency and, of course, the type of product being moved. In addition, modular units can be quickly changed and adapted to different applications without requiring a major redesign or lengthy lead time.
That’s important because speed and flexibility are the main challenges for today’s industrial packaging processes, according to experts at Schmalz Inc., Raleigh, N.C. Research at Schmalz shows that conventionally designed vacuum grippers are bottlenecks in terms of design, assembly and commissioning of customer-specific packaging and handling machines. That’s due to often-complicated processes involving everything from design to start-up.
Part of the problem is that packaging-industry OEMs and system integrators create concepts and “digital” versions of machines based solely on technical specifications or process descriptions. In many cases, product samples are not yet available, or they are only prototypes and subject to change. Engineers don’t finalize the machine concept and begin design until an order is actually received. And a vacuum gripper is usually only designed after machine details are complete. According to Schmalz’s calculations, this can put a lot of challenging requirements on gripper design.
Another issue is that frequent product changes have become the norm in many industries. Depending on the product life cycle or how a product changes in terms of size, shape, weight and feel, different grippers must be integrated on the machine. A modular approach lets users combine various flanges, connectors and suction pads to create a “new” end effector with relative ease.
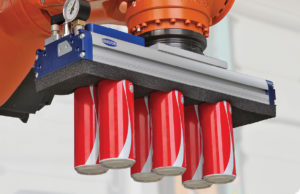
Area grippers are used for standalone tasks, and as building blocks in larger layer grippers.
Layer grippers
As one successful example, Schmalz has developed the SPZ layer gripper system to streamline pick-and-place, palletizing and depalletizing processes. According to Mike Vigoda, manager of the company’s Vacuum Gripping Systems Group, the SPZ is a complete system that includes everything from vacuum cups to the vacuum generator, and all the valves, switches, connectors and controls in between. Its flexible “Lego-like” configuration lets users quickly and easily tailor the unit to meet exact application requirements.
In packaging applications, Vigoda explained, the SPZ helps automate pick-up and transport processes for items that have been sorted and stacked in layers. The gripping system can handle a wide range of products that include cardboard boxes, composite packaging, bottles, cans, glass jars, bags, and shrink-wrapped and loose goods—even chilled and frozen products. (And with different sealing interfaces, SPZ layer grippers can be used for construction materials like wooden boards and beams, ceramic tiles and bricks.)
Manufacturers use the SPZ in a number of ways. One is to move a pallet’s worth of empty cans, bottles or plastic containers and place them on conveyors. From there, the containers feed into a high-speed production system, say for filling with peanut butter or mustard. At the other end of the line, grippers move finished products from holding areas and stack them on pallets, one layer at a time.
The SPZ also lets manufacturers configure the layers as needed for stability, maximum use of space, or other reasons. And the gripping system can handle layers with “chimneys” or gaps, and those that are incomplete or have a mix of products.
Building blocks
Key subsystems for constructing the SPZ are universal grippers called “area-gripping” systems, said Vigoda. They’re versatile, reliable, efficient and suited for a wide range of tasks. Individually, they’re proven grippers designed for handling single parts or just a few items. For larger jobs, multiple area grippers can be interlocked together and networked to build the SPZ.
Two types of area grippers are available. One, called FXP, has built-in vacuum generation via a plug-in ejector. The second, the FMP, is similar in construction but interfaces with external vacuum generators like pumps and blowers. New versions, FMP-S and FXP-S, include integrated vacuum valves for more-compact overall units. (See the related sidebar, “The benefits of built-in valves.”)
All are built of aluminum for high stiffness and low weight. Lower weight often permits higher accelerations for higher productivity and, possibly, results in smaller robots that mean lower overall system costs. Area grippers each measure about 5.1 in. (130 mm) wide. But users can specify length anywhere from 17.4 to 56.4 in. (442 to 1,432 mm) in standard configurations. Custom units in 5-in. increments for FMP/FMP-S (11 in. for FXP/FXP-S) have a maximum length of 236 in. Thus, choosing the number of modules and the desired lengths lets users specify final SPZ dimensions and overall working area. For instance, they can easily handle standard pallets measuring about 40 × 50 in. (1 × 1.2 m) and carry a maximum load of 550 lb (250 kg).
As an added benefit, noted Vigoda, the interlocking area grippers also let users create multiple, independent vacuum zones. Rather than powering the entire surface every cycle, users can selectively direct vacuum only to specific areas as needed—say for moving a half-pallet of goods. That ensures minimal leakage and higher energy efficiency. One SPZ could have two, three, four or more different size and shape suction zones.
To create the zones, a controller or PLC directs onboard valves to selectively control vacuum flow. However, multiple zones do require more I/O. In addition, vacuum switches supply feedback to the controller. They are used to check vacuum levels, determine part presence or signal a fault, letting the controller initiate the next move or halt a process.
Also, users can opt for on-board or external vacuum generation. Built-in, venturi-type units generate vacuum with compressed air, and they are generally for smaller, lower-cost SPZ systems. For larger designs, said Vigoda, it usually makes sense to use an external vacuum blower. That’s because the cost of compressed air is much higher than the cost of electricity to run a blower, making the overall system more economical and efficient.
Another option is to mate a blower with a frequency converter for even higher efficiency. In essence, this variable-speed drive lets the blower produce precisely the vacuum flow needed for a given task, no more or less. This cuts power consumption, and it also helps extend the life of the blower. However, such systems do carry a higher up-front cost, he cautioned.
Cups and pads
Another facet in designing modular vacuum handling systems is specifying the vacuum cups themselves. They’re the critical interface between handling equipment and products. Fortunately, a wide range of push-in or screw-in suction cups and flexible sealing foam are designed for many different types of products and packages.
For example, vacuum cups are available in various geometries including simple, circular types for general-purpose handling; extra-deep cups for round or highly curved surfaces; and oval shapes for picking up long and narrow products. They come in two general shapes, flat and bellows. Flat vacuum cups are best for handling workpieces with flat or slightly curved surfaces. Properly designed, they have good rigidity and stability to handle high shear forces and can withstand forces and accelerations from fast automated-handling movements.
Bellows suction cups, on the other hand, have one or more accordion-like convolutions. This lets them compensate for varying workpiece heights and handle parts with uneven surfaces. Evacuating the bellows also creates a lifting action. They are often used with nonrigid packaged goods or shrink-wrapped products.
The cups also come in various materials to suit a specific application and environment. Typical examples include nitrile rubber (NBR) that’s economical and is a first choice for general-purpose applications, silicone for food-grade applications, polyurethane for excellent wear resistance and high strength, and fluoroelastomers for high chemical and weathering resistance. Depending on the application, vacuum cups might need to tolerate wash-down fluids, steam or extreme cold or heat. Different vacuum cups are rated for operating temperatures from -20 to 400° F (-30 to 200° C), depending on the material.
In addition to the basic version of the modular SPZ, it’s also available with supplemental mechanical clamping. That adds stability and holding power when handling products that are difficult to pick up using vacuum alone.
Examples include PET bottles or loosely packed and partially filled cardboard boxes. Another variant combines mechanical clamping and an additional skirt that creates a vacuum suction chamber around products. It permits handling products in layers that previously could only be transported manually, such as loose cans on cardboard trays.
The benefits of built-in valves
Most universal area grippers that use external vacuum sources require add-on valves to control vacuum flow to suction cups and pads. Schmalz’s newest version, the FMP-S gripper, includes an integrated vacuum-control valve for a more-compact overall unit. Like FXP and FMP grippers, it can be used as a standalone device or as a component on the SPZ layer gripper.
Typical grippers rely on external valves to control vacuum flow. An additional venting valve and an active compressed air line are also needed to ensure quick release of a gripped product. In contrast, the FMP-S connects directly, via hose or tubing, to the vacuum source. The vacuum valve, control valve, electrical connection and air-line connectors are built in.
The result is a more-compact unit with 40% shorter evacuation times and 25% less weight, compared to similar grippers with external valves. This makes the unit well-suited for highly dynamic applications. Packaging the relevant components internally also improves reliability, reduces installation costs, and minimizes the possibility of tooling /robot interference that could otherwise damage the valve.
Vacuum switches and IoT
New VSi series of vacuum and pressure switches from J. Schmalz GmbH lets handling systems communicate with conventional fieldbus systems via IO-Link and also supply readout information to smartphones.
Electronic VSi switches monitor pressure in automation and handling systems and transmit status data to a controller via the IO-Link interface. It gives system operators better access to operating parameters and diagnostic data and quicker response in the event of faults or errors.
The switches come with or without a display, or with an external operating display; and in pressure, vacuum or combined versions. Units can be installed independently of the display, for instance directly on a suction pad. Settings like switching points can be adjusted via the display element and transferred to other switches.
Users can also display information and exchange data via an NFC-compatible smartphone. Users can receive service and maintenance information, such as serial and order numbers or operating instructions, directly on a mobile device. LEDs indicate whether switching points have been reached and power is available.
IO-Link and NFC capabilities open up a host of innovative communication possibilities and makes processes more transparent. Schmalz already uses the technology in a variety of vacuum ejectors, and the vacuum switch can be used on SPZ systems as well.
Schmalz Inc.
schmalz.com
Filed Under: Pneumatic Tips