Efficient farming is top of mind for the agricultural industry, but not at the environment’s expense. Though net-zero targets tend to push OEMs toward fully electric and even autonomous machines, there are ways to partially electrify without overhauling a design. HAWE Hydraulik provides examples of how to increase efficiency by electrifying functions strategically.
Electrify work processes in yard loaders and telehandlers
Electrically driven yard loaders and telehandlers have already been working successfully in agriculture and at transshipment points for some time. The drive concepts are constantly being optimized, and new components are coming onto the market.
However, instead of redesigning the entire vehicle, proven work processes are electrically driven. This usually means starting with measurements on the existing vehicle and a reference cycle definition — a specific, standardized workflow — which is also used to monitor success.
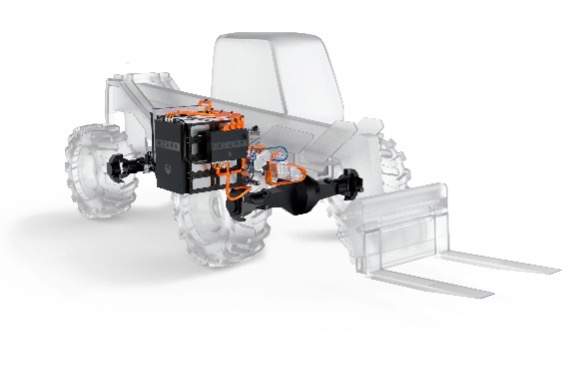
The first step is to separate the drive and hydraulics. The drive’s efficiency can be significantly increased using a direct electrical or electromechanical (with gearbox) travel drive instead of a hydrostatic one. As a result, there is less oil in circulation. In addition, a separate electric drive — which drives the hydraulic pump for work functions, such as lifting, lowering, tilting, and steering — can be reduced to minimum energy consumption or switched off in driving mode. Electrically actuating the transmission brakes and steering and installing a small electrohydraulic steering unit can also increase efficiency without significantly adjusting the working hydraulics system.
The next step is to optimize the hydraulics, focusing on the power requirement when lifting and lowering loads.
From an operational standpoint, since electric telehandlers and farm loaders reduce emissions and noise, they can be used indoors or in areas where exhaust fumes and noise cause problems.
Decentralize hydraulics in harvesters
Highly specialized agricultural machinery uses many ancillary functions and individual modules for work processes. However, not all functions need to be supplied by the central hydraulics. Using small decentralized mini hydraulic power units to drive and control such functions minimizes tubing and simplifies installation close to the control function.
For example, the discharge pipe or ejection flap in combine and forage harvesters or the conveyor belts in potato and beet harvesters can be controlled with mini hydraulic power units installed close to the consumer. The hydraulic power pack works as a self-sufficient unit and only needs to be powered, saving machine builders long hydraulic hose lines, reducing losses, and simplifying commissioning.
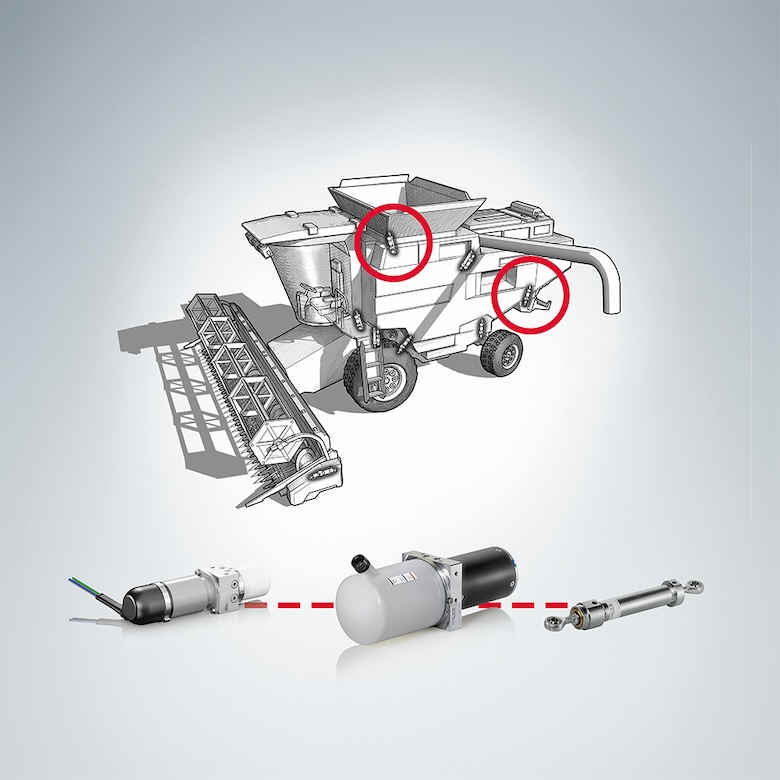
Mini hydraulic power packs can use dc or ac motors, and some can reverse the direction of rotation to make controlling a double-acting cylinder easy, negating the need for an additional directional valve. Units should include an integrated temperature switch for motor overload protection and enable connection to various actuators. Installation is arbitrary for decentralized hydraulic power packs, as the control is unchanged — via a joystick in the driver’s cab, for example. By looking at the machine design with decentralized power generation and low energy consumption in mind, design engineers can find additional functions in which this decentralized drive proves advantageous.
Simplify attachment controls in tractors
The agriculture industry is increasingly interested in networking and automating machines and work processes. For example, modern tractors are equipped with telemetry systems and wireless communication, allowing the tractor and implements to be controlled and monitored remotely. This increases efficiency and offers the opportunity to optimize productivity and crop yield further.
Each attachment control has different requirements depending on the function. In particular, the hydraulic control is flexible and has high power density, dirt resistance, and a good price-performance ratio. By pairing the hydraulic control with electronic intelligence, such as a directional control valve block with a CAN bus, the entire valve block can be connected to the onboard electrical system with just one plug. System feedback and parameter adjustments are carried out directly in the CAN head of the valve block, relieving the main control and bus systems.
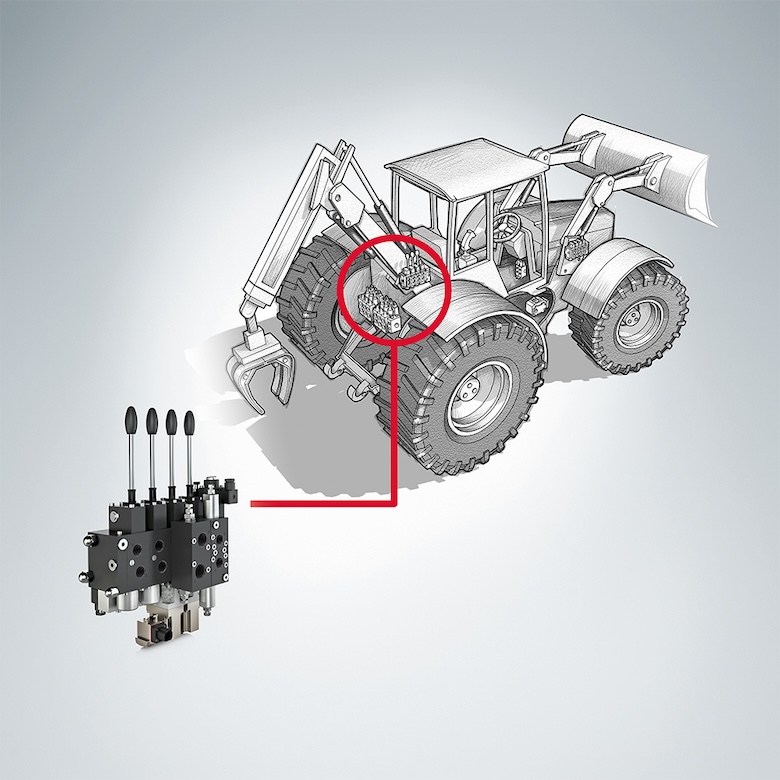
These electronic control systems enable operators to control tractor attachments via electrical signals from the cab — or even run them autonomously. This makes it possible to pre-select different settings and working modes in hydraulic controls. Sensors can also be integrated to record information about soil conditions, crop yields, and other relevant parameters and pass data to the main controller or control center. In self-regulating systems, the tractor can automatically react to changing conditions and improve work efficiency. The hydraulic controls offer many solutions for this, which are also energy-efficient and weight-optimized.
HAWE Hydraulik
hawe.com
Filed Under: Components Oil Coolers, Mobile Hydraulic Tips, News, Pumps & Motors, Trending