Micro-PLCs with support for Wi-Fi and industrial communication protocols make it possible to add IIoT to any type of machinery in an easy and incremental manner.
Bill Dehner, technical marketing engineer, AutomationDirect
Pneumatically- and hydraulically-operated equipment is found worldwide in machine shops, factory floors, and production sites. While these heavy-duty systems excel at manufacturing and production tasks, they typically lag behind common consumer devices with regards to convenient connectivity and data access. Which is unfortunate, because all sorts of industrial equipment contains a wealth of operational knowledge. End users have become accustomed to remotely accessing and viewing information from consumer devices, and would like some of the same capabilities for their production equipment.
Unfortunately, even ‘intelligent’ equipment is often installed in a standalone, local-only manner (Figure 1). Sometimes data connectivity is possible via a serial or Ethernet connection, but in many cases — especially for hardwired machines — it can be very difficult to obtain even basic information like on/off status. Combined with the fact that end users may use many makes and models of field equipment, it can be complicated and expensive to create a standardized way of obtaining the data needed to improve efficiency.
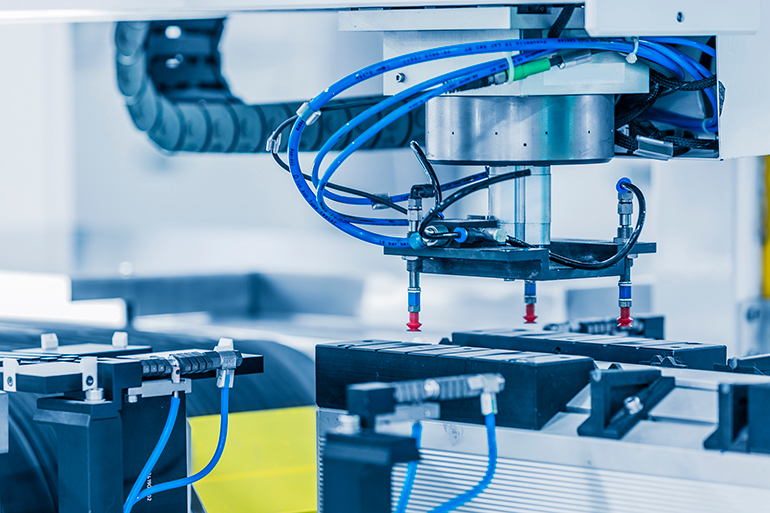
Figure 1: For many types of standalone industrial pneumatic and hydraulic equipment, end users are looking for practical and affordable ways to add IIoT capabilities; modern micro-PLCs are often the best solution. All images courtesy of AutomationDirect
Across most industries, end users are looking for an affordable way to bridge the gap from the plant floor to the cloud. Creating this edge-to-cloud connectivity is a key requirement for industrial internet of things (IIoT) implementations, and there are some sophisticated and complex ways to create these types of systems. However, many end users are finding the best answer is often to leave existing automation systems largely as-is, and to add IIoT capabilities by installing easy-to-use and low-cost industrial controllers that are cloud-capable.
IIoT empowers machines and small systems
Some end users may be intimidated by the thought of adding IIoT connectivity to pneumatic and hydraulic equipment, especially legacy systems. They may think IIoT requires extensive ‘big data’ project expenditures, along with custom code that is difficult to create and support. Sometimes the equipment, and even the automation component, simply don’t offer the required connectivity options. However, the truth is that some IIoT technologies are very scalable and can be easily implemented for just a few data points, and then expanded when it makes sense.
In fact, in many cases a small amount of data can yield great value. For most machines, simply providing visibility (and possibly data-logging) whether the machine is enabled and running, if it is paused due to external conditions, and if there are any faults, can be the first steps toward helping users improve the overall equipment effectiveness. Once the basics are handled, users might move on to monitoring and improving more advanced aspects like fine-tuning throughput and energy consumption. Specific to pneumatic and hydraulic equipment, there can be plenty of other useful on-board data to monitor, such as pressures and cylinder extend/retract times. The best IIoT solutions will allow designers to start small, then scale up once basic concepts are proven.
Any data capable of being monitored and transmitted to on-site or cloud-based databases can be logged, visualized, analyzed, and used as the basis for reports. In particular, cloud access makes it possible to compare multiple machines installed at one or many locations. An end user company with multiple sites can identify best practices at any location and implement these across all plants and facilities. An OEM can develop performance information of an entire fleet of like equipment installed at multiple locations and operated by a variety of end users.
New options are available so users can easily create an IIoT connection at any machine without affecting the underlying hardwired or automation platform. These users can follow a consistent hardware and software approach to add IIoT to any systems in their facility.
Affordable IIoT implementations
Brand-new machinery and equipment may be available with PLCs or other built-in provisions for establishing IIoT and cloud connectivity. Some of the latest sensors and even pneumatic manifolds are intelligent devices capable of providing a wealth of information. But new installations number far less than the thousands of existing systems, and it is rarely practical or cost-justified to retrofit existing operational assets with new automation.
For these reasons, it is far more attractive to install a device at existing systems to add IIoT functionality without impacting basic operation. A device used for this service should have several key characteristics:
- Built for industrial installations, yet economically priced.
- Offer basic wired I/O signals for connection to any type of field signals.
- Include connectivity for typical industrial busses — like Modbus, EtherNet/IP, and ASCII — so data can be gathered from intelligent edge devices.
- Support Ethernet for high-performance connection to a supervisory network.
- Support Wi-Fi so the device can be quickly installed without the expense of network cable runs.
- Support Bluetooth so users can configure the device wirelessly.
- Use the low-bandwidth MQTT protocol, which is ideally suited for transmitting IIoT data through site-based firewalls and up to the cloud.
- Provide a degree of on-board programming to manage the gathered data.
- Have an on-board microSD card for local data logging.
- Configurable with easy-to-use and free software.
- Include enhanced security measures since the device will be network connected.
Until recently, PLCs could only meet a few of these requirements. While industrial PCs could address some of the other points, this involved expense and complication. What has changed today is the availability of micro-PLCs incorporating some or all the capabilities listed above, and available at a reasonable price (Figure 2).
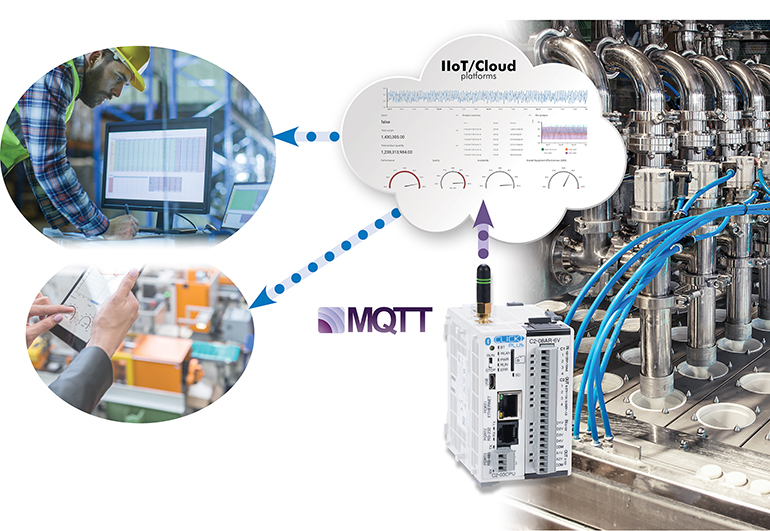
Figure 2: The AutomationDirect Click Plus PLCs combine a compact industrial form factor with advanced connectivity, Wi-Fi, and cloud connection capabilities, for an easy to use and low-cost link to IIoT platforms that can be added to any type of automated equipment.
These PLCs provide many familiar capabilities, such as stackable and expandable modular I/O and convenient ladder logic programming via free software. In conjunction with support for multiple communication protocols, they include improved security measures like a strong password requirement, the ability to disable unused ports, ping disable, and more.
Streamlined IIoT in reality
One manufacturing company used many makes, models, and vintages of pneumatically-operated assembly equipment. There really was no effective way to monitor the production floor other than walking around and observing the machines.
To gain the desired remote visibility, they installed Wi-Fi capable micro-PLCs one at a time on their most important machines (Figure 3). These micro-PLCs were added in parallel to existing automation systems, using traditional I/O points to monitor the running status, any trouble condition, and cycle count. Each installation was performed quickly during a period of brief machine downtime, and then the data points were transmitted to a cloud service.
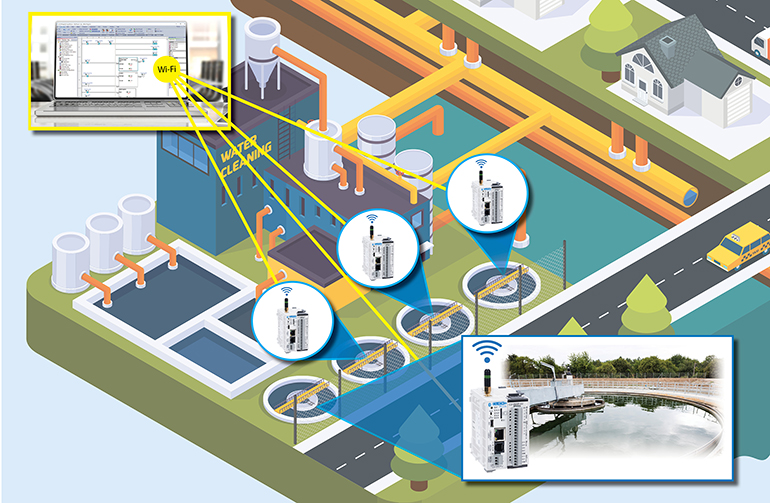
Figure 3: Wi-Fi capable micro-PLCs like the AutomationDirect Click Plus are easily distributed throughout a site on machines and automated systems to create IIoT connectivity.
At first, this simply made it possible for operators to use a mobile tablet for visualizing which machines were operating properly. But as more machines came online, it was possible to analyze other situations. For instance, if a downstream machine was experiencing trouble and delaying an upstream machine, the condition was alerted. Or, where multiple similar machines were connected using this IIoT solution, the lead operator was able to compare the machines and look for any with substandard performance.
Another system integrator took things a step further using a micro-PLC platform as a solution for local data logging and a data source for a database. They connected a micro-PLC analog input to a local temperature sensor, and configured the micro-PLC to log the temperature and a date/timestamp to a microSD-located CSV file, based on a periodic time trigger. Using free SQLite running on a PC connected to the wireless micro-PLC, they created a database table with DATETIME and temperature columns. The source temperature tag was connected to a MQTT host on the PC, and then Node-RED running on the same PC was used to inject timestamped temperature readings to the database. In this way a low-cost micro-PLC and free software was used to capture the latest information, and this scheme could be extended to other equipment as needed.
Edge to Cloud, simplified
Manufacturing and production companies everywhere typically operate many legacy machines, but they are challenged with obtaining a birds-eye view of performance. Traditional methods of adding typical PLCs, PCs, and software can be used to address this issue, but this often requires a level of cost and effort exceeding the benefit.
New micro-PLCs — with on-board Wi-Fi, industrial protocols, and other related features — have improved upon this situation. These micro-PLCs can be quickly added anywhere to monitor a few points, or even an intelligent device, and then transmit data to the cloud wirelessly. End users can follow this approach as a standardized way of adding IIoT capabilities to any of their machines and production systems. With the right data accessible, users can improve the efficiency of their operations.
AutomationDirect
automationdirect.com
Filed Under: Industry 40, IoT, Trending