Material handling machines lead the pack in terms of electrification and autonomy, as their compact designs are a perfect fit to test out sustainable options.
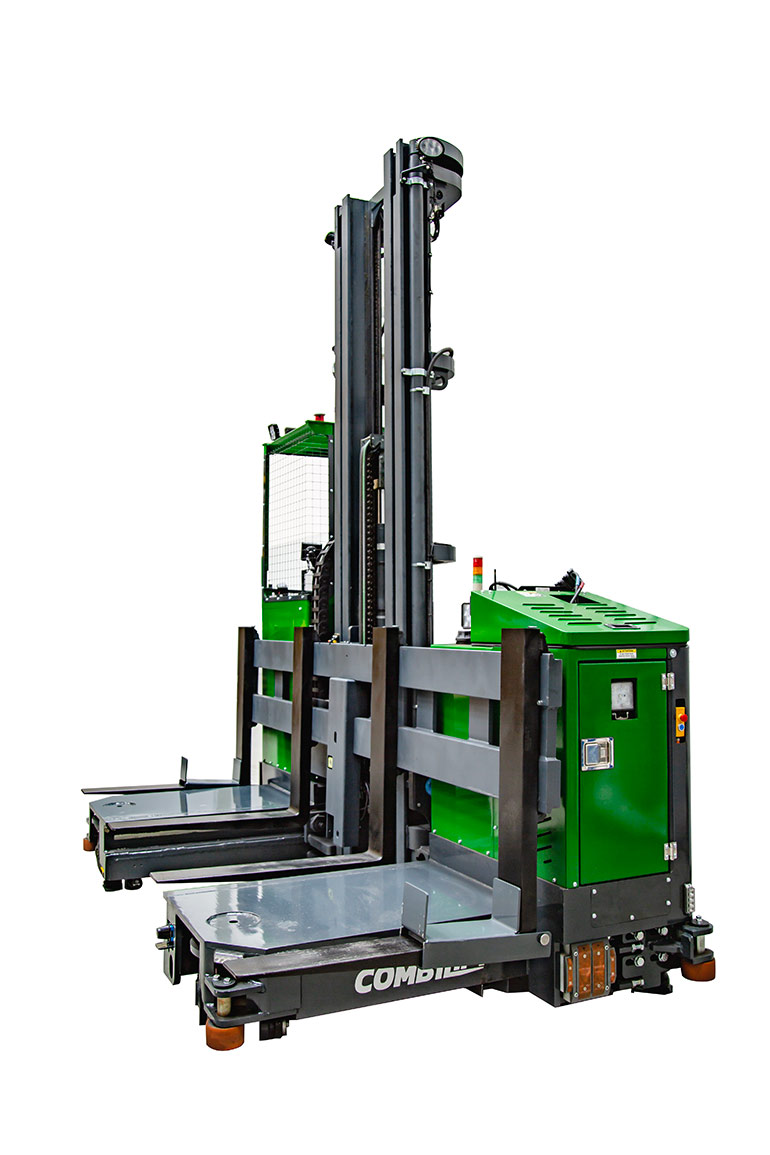
is Combilift’s first autonomous machine. It is a 4-wheel electric stand-on model.
As battery-powered machines continue to grow in the mobile market, one area stands out as an obvious choice for their expansion — mobile material handlers. The smaller size and lower power requirements of mobile material handlers make them well-suited for battery operation. Larger machines, such as heavy construction equipment or long-haul trucks, typically demand significantly more energy, making batteries less practical for their extended operation.
Additionally, the versatility and maneuverability of mobile material handlers align with the advantages of electric power sources. Battery-driven systems provide quick and precise control, which is essential for tasks that involve picking, lifting, and transporting loads in confined spaces, like warehouses or shipping yards. This precision is often harder to achieve with the torque and power fluctuations of traditional internal combustion engines.
Finally, because material handlers are often used indoors or in heavily populated urban areas, they can take advantage of the significantly lower noise and vibration levels of battery-operated machines. Here’s a look at two new electrically-powered forklifts on the market.
Packing a one-two punch: electric and autonomous
Integrating autonomous functions into battery-driven machines further enhances their efficiency and safety. These systems can be programmed to accurately perform repetitive tasks, reducing the risk of human error and enhancing productivity. Autonomous features can also improve safety by minimizing the need for human operators.
To this end, Irish manufacturer Combilift has launched its first autonomous machine. Developed by Combilift’s dedicated automation team, the Combi-AGT is a 4-wheel electric stand-on model, which is the world’s first autonomous dual operational sideloader for long loads.
The Combi-AGT harnesses the very latest smart technology to meet customer demands for driverless sideloader capability. These were driven in part by safety to eliminate the presence of personnel in aisles, consistency in handling procedures and to maximize order fulfilment, while also having a backup manual mode in case of power outages or internet disruptions.
Combilift’s automation team has spent three years liaising with specialist steel suppliers to identify the best specifications for the Combi-AGT. The new model, with a lift capacity of 5,000 kg/11,000 lb and various lift heights, addresses the requirements of steel service centers and the metal industries, which typically handle long loads. Combilift worked in tandem with IMR (Irish Manufacturing Research) during the development process to enable seamless integration with multiple client warehouse management systems.
Its design is based on the electric manually operated Combi-GTE model which has long been a popular choice for service centers due to its ability to work efficiently in rail guided narrow aisles. The first Combi-AGT unit was supplied to Kansas-based Steel and Pipe Supply 18 months ago, and since then Combilift has collaborated with a number of metal service centers across North America during the development process.
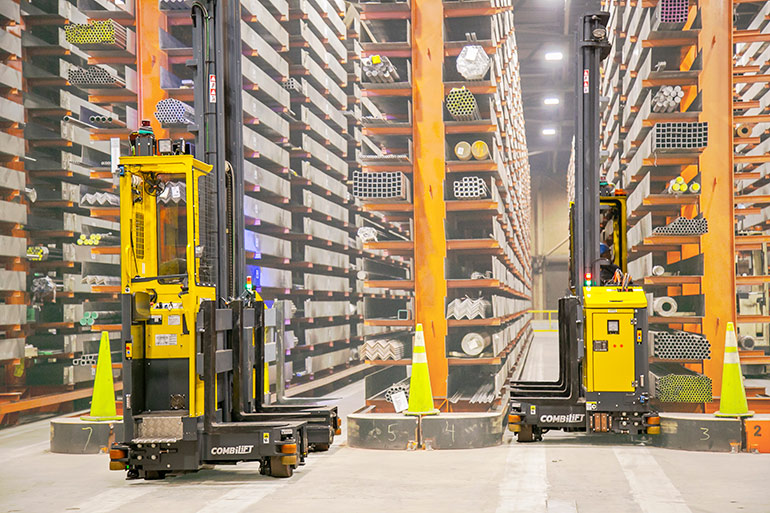
The laser-based sensors, fitted at various positions on the chassis, constitute an anti-collision safety system, as required by the American National Standards Institute. If the machine senses an obstacle or pedestrian that has entered its path, it automatically slows down and will, if necessary, stop in cases of emergency. It will then continue to drive automatically when the obstacle has cleared its safety sensor area. The enhanced adaptive safety system enables the size of the obstacle detection fields to increase or decrease as per the steer angle and speed of the truck.
The natural feature navigation system is superior to traditional methods of truck navigation based on wire guidance or artificial landmarks such as reflectors. Instead, it uses the naturally occurring features in a warehouse – walls, racking and columns for example, avoiding the need to add to or change the warehouse infrastructure.
Its newly developed load dimension detection system (patent pending) operates by performing a laser scan of the load to check that its length matches the task sent to the machine. Similarly, when unloading, it checks that the rack in front has sufficient free space to accept the load.
“We have deliberately not rushed into incorporating autonomous products into our portfolio. As with any new launch we have carried out extensive field tests to make sure it is fit for purpose by liaising with a number of leading customers in the metal service industry during the product development stage,” said Combilift CEO and Co-founder Martin McVicar. “We are fortunate to have a very motivated group within our autonomous team of software and mechatronics engineers who are committed to scaling this business unit. The Combi-AGT signals a new milestone in product development with further expansion of our autonomous range in the pipeline.”
The AGT features hydraulic actuation and variable-speed programmed routes. It has a 72 V battery and opportune battery charging.
Visit combilift.com for more information.
Reduced energy use with lithium batteries
The new battery-powered B-X Series from Hyundai forklift is complete with truck, lithium battery and charger, with an option to apply a conventional lead acid battery. Available in 5,000-to 7,000-lb capacity, the heart of the B-X Series is a design that dramatically reduces energy consumption to cut the cost of ownership. Plus, the B-X Series can take advantage of Lithium-Ion Battery Technology, that provides longer run times, reduced charging time, and lower energy costs with zero emissions. Throughout these rugged machines are innovative features that improve reliability, simplify servicing, enhance safety, and offer a high level of operator comfort.
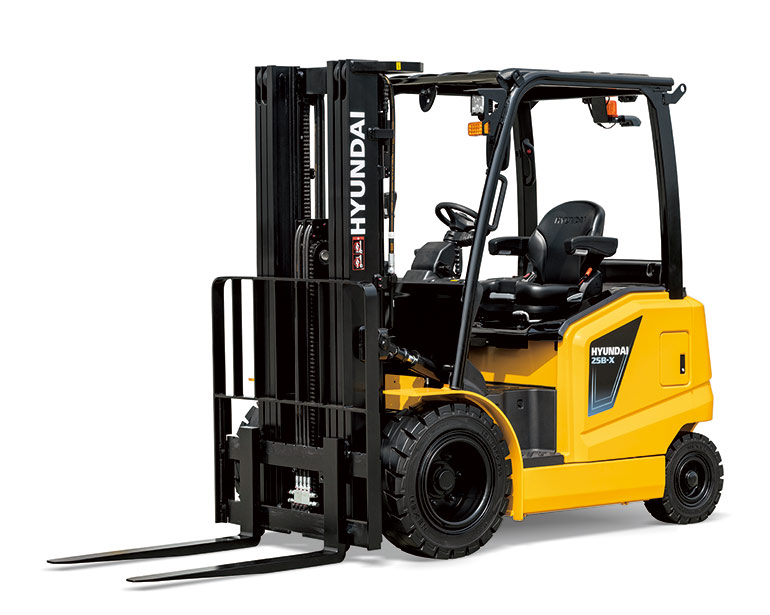
The machine offers a 17% increase in energy efficiency, with a 4.6 dB reduction in noise levels. In addition, hydraulic noise at idle state and hydraulic noise during lifting operation were significantly reduced.
Battery replacement is simple. A deep drop type battery can be easily and quickly removed and installed (through the side of the forklift) using the fork of a 3.5 ton (or less) forklift or 1.5 ton hand pallet truck with a dedicated pallet, without the need for expensive equipment. When the battery has to be charged after using the vehicle, you directly connect the charger connector to the connector which is separately provided on the left side cover and the charging will begin.
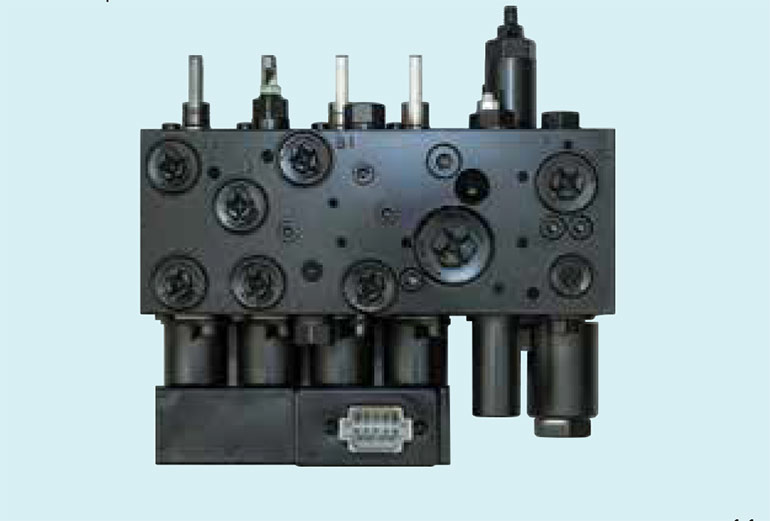
The BX series still takes advantage of hydraulics. A state-of-the-art hydraulic control valve controls the hydraulic motor so that its output is in proportion with the movement of the spool detected by a non-contact Hall sensor. It uses SASA sensor-type HPS system in which the output of the hydraulic motor varies in direct proportion to the turning speed of the steering handle and the amount of movement of the lift lever, and a Hall sensor type MCV value which is linked to the load. This ensures high vehicle reliability.
Visit hyundaiforkliftamericas.com for more information.
Filed Under: Mobile Hydraulic Tips, News, Trending